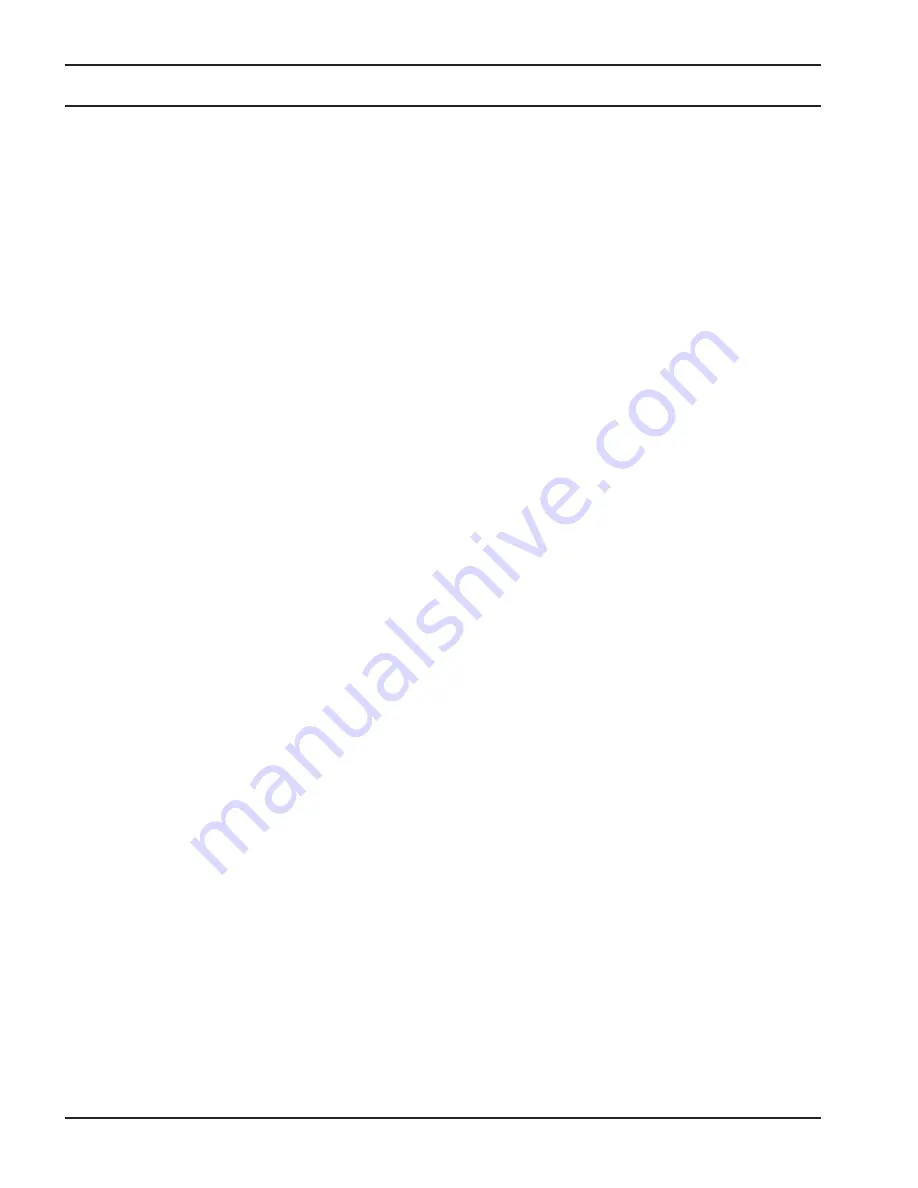
BetrieB
36
Betriebsabfolge
Am EPP-362 ist kein Ein/Ausschalter eingebaut. Für dieses Stromaggregat dient der Leistungsschalter an der Wand als
Schalter. Sobald der Wandschalter geschlossen wird, geschieht Folgendes:
1. Der Steuerungstransformator T2 wird mit Strom versorgt. Dadurch werden die Platinen mit Strom versorgt: PCB1,
die Steuerungsplatine‚ und PCB2, die Treiberplatine. Der Hauptmikro auf der Steuerungsplatine (PCB1) stellt die
digitale Kommunikation mit CNC/Prozesssteuergerät durch den Verbinder DB25 über CAN oder eine analoge
Schnittstelle her.
2. Pumpenmotor (M2) wird auf EIN geschaltet. Kühlmittel wird an den Brenner gefördert und kehrt jeweils durch
Kühler, Filter, Flusssensor und IGBT-Kühlplatte in den Tank zurück.
3. Die Steuerungsplatine führt eine Störungs-/Fehlerkontrolle durch. Sind keine Störungen/Fehler vorhanden, geht
die Anschaltabfolge weiter.
4. Die Stromzufuhrleuchte (PL) auf der Fronttafel leuchtet ständig, was anzeigt, das Stromzufuhr vorhanden ist, und
die Störungsleuchte ist AUS (OFF), was anzeigt, dass keine Störungen/Fehler vorhanden sind.
5. Die Stromversorgung erlaubt es Relais K4 zu schließen, wenn im Stromaggregat keine Störungen/Fehler vorhan-
den sind und keine Unterbrechung in der Stromversorgungs-Freigabekette an der Schneidmaschine bestehen.
6. Sind die obigen Schritte ausgeführt, schließt der Bus-Vorladekondensator (K2) und lädt den Busfilter-Kondensator
(C1) in jeder Phase durch einen 2 Ohm-Widerstand auf.
7. Ist der Bus bis an einen Schwellenwert von 200V DC vorgeladen, gibt die Steuerplatine den Befehl, den Haupt-
schutzschalter (K1), Hauptgebläsemotor (M1) zu schließen und K2 zu öffnen. Dies erlaubt es dem Busfilter-Konden-
sator, sich bis auf die volle Spannung von 360V DC aufzuladen.
8. Der Bus ist an sobald der Wand-Leistungsschalter geschlossen ist und in der Stromversorgung keine Störungen
bestehen. K1 und M1 bleiben 5 Minuten lang im Leerlauf EINgeschaltet und schalten sich dann AUS; daher leckt
die Busfilter-Kondensatorspannung durch Widerstand R8 (3 kOhm, 100W).
Erhält das EPP-362 den Befehl, den Plasmaschneidprozess zu beginnen, geschieht Folgendes:
1. Sobald das Startsignal gesendet ist, beginnt eine Sanftstartabfolge, wenn der Bus nicht an ist. Die Hauptsteuerplati-
ne (PCB1) gibt den Befehl aus, Busvorladerelais K2 zu schließen. Dieses Signal wird durch Flachbandkabelverbinder
J6 an das Relaisblockmodul (RB1) gesendet. Am Relaisblockmodul wird Relais Eins (RB1-1) mit Strom versorgt. Dieses
reicht 24V AC an die Spule von K2, das Sanftstartrelais, weiter. Dadurch liegt am Haupttransformator (T1) Netzspan-
nung mit einem in Serie geschalteten 2 Ohm-Widerstand (bei jeder Phase), um anfangs die Strommenge zu begren-
zen. Dies geschieht aus zwei Gründen:
a. aufgrund der großen Eingangsfilterkondensatoren ergäbe sich ein sehr großer Strom am Ausgang des Haupt-
transformators
b. zur Strombegrenzung, falls im Gleichrichter, den Kondensatoren oder dem Transformator ein Kurzschluss auf-
tritt.
2. Ist K2 geschlossen, überwacht PCB1 die Busspannung über C1. Der Hauptmikroprozessor auf PCB1 wartet, bis die
Busfilter-Kondensatorsp200V DC erreicht oder 500 ms abgelaufen sind. 200V DC an, leitet der Mi-
kro Befehle ein zum Einbeziehen von Hauptkondensator K1, Einschalten von Hauptgebläse (M1) und öffnet dann K2.
Nach Einbeziehung von K1 wartet die Stromversorgung wenige Millisekunden bis der Bus seine volle Spannung von
360V DC erreicht hat. Erreicht die Busfilter-Kondensatorspannung keine +200V DC bevor der 500 ms Abschaltung,
sendet die Stromversorgung über CAN Fehler 15 an CNC/Prozesssteuergerät und schaltet die Störungsleuchte (FL)
auf der Fronttafel auf 50 % Einschaltdauer.
3. Wenn der Bus voll geladen ist und der Hauptmikroprozessor über CAN-Kommunikation alle entsprechenden Ströme
und Einschaltzeiten vom CNC/Prozesssteuergerät gelesen hat, gibt der Hauptmikroprozessor das PWM-Startsignal
an den Servomikro aus, der dann 25 kHZ- Frequenzimpulse an die IGBTs abgibt. An diesem Punkt überwacht der
Hauptmikro die Leerlaufspannung (OCV) am Ausgang, die 200 ms lang wenigstens 280V DC betragen muss. Mis-
slingt dies, schaltet sich die Stromversorgung ab, stellt die Störungsleuchte um und sendet Fehler 13 an CNC/Prozes-
ssteuergerät.
Summary of Contents for EPP-362
Page 2: ...2...
Page 4: ...EPP 362 Plasma Power Source 4...
Page 7: ...7 Sicherheitsvorkehrungen...
Page 8: ...Sicherheitsvorkehrungen 8...
Page 11: ...Beschreibung...
Page 12: ...Beschreibung 12...
Page 15: ...INSTALLATION...
Page 16: ...installation 16...
Page 28: ...installation 28...
Page 29: ...29 Betrieb...
Page 30: ...Betrieb 30...
Page 38: ...Betrieb 38...
Page 39: ...39 MAINTENANCE...
Page 40: ...Maintenance 40...
Page 44: ...Maintenance 44...
Page 45: ...45 TROUBLESHOOTING...
Page 46: ...46 TROUBLESHOOTING 46...
Page 53: ...REPLACEMENT PARTS...
Page 54: ...Replacement Parts 54...
Page 56: ...Replacement Parts 56...