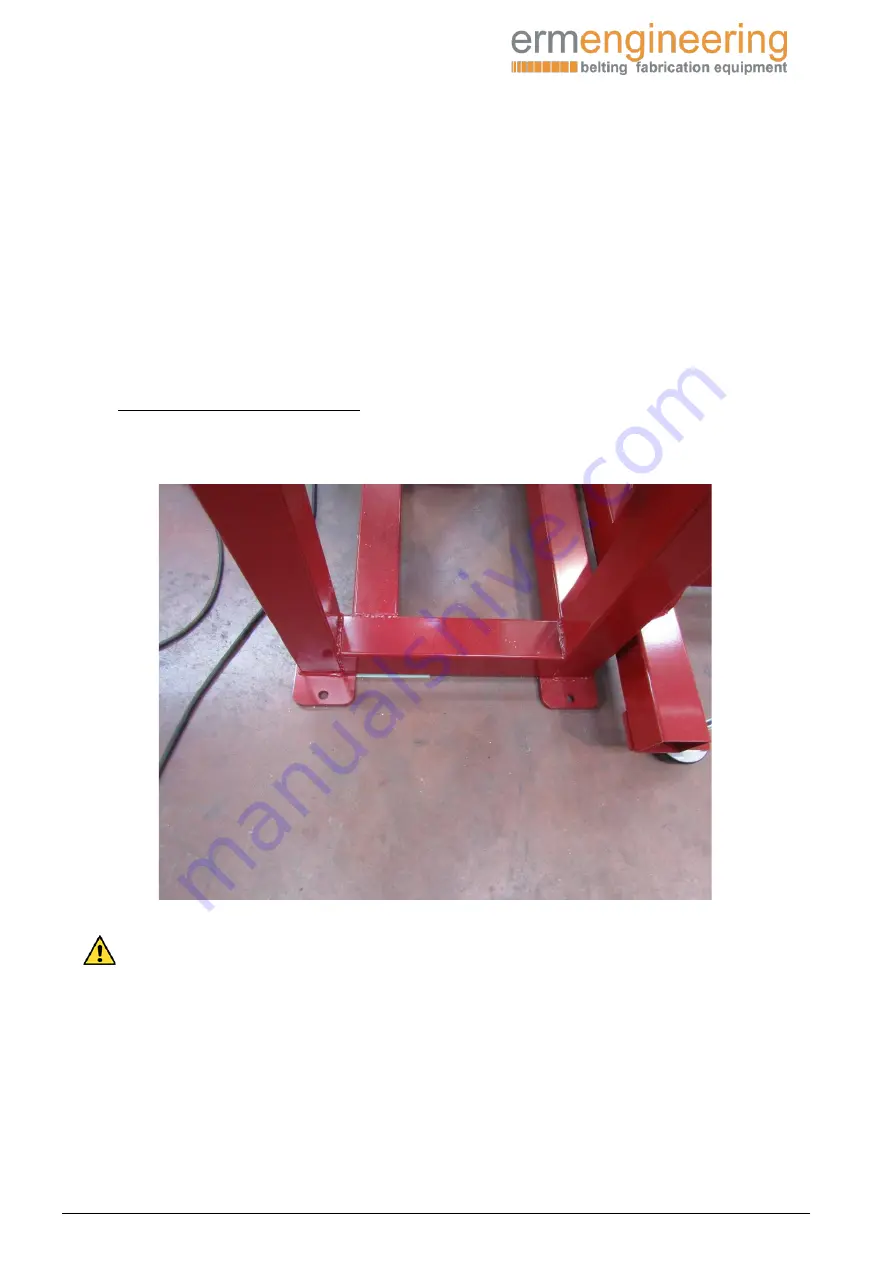
Use and maintenance manual
Timing belt welder
Model: LRSE-180
_______________________________________________________________________________________________________________________
P a g . 5
−
During use of the machinery and industrial use, people are subject to the risk of damage or
injury by mechanical elements in linear or gyrating movement, high voltage electric
components and static components under high temperature, due to which, during design
and construction of its equipment, ERM Engineering. has aimed to reduce and minimise
those risks by including protection devices and safety systems based on the European
Community Council Directives.
−
Pay special attention to the following danger, prohibition and obligation signs located at
different places on the machinery:
-
Installation and start-up
:
Site the machine in working area and fix the two-
back mast with metallic’s bolts on floor.
ATTENTION: DO NOT USE THE MACHINE IF NOT FIXED ON FLOOR; RISK OF
FALLING.
Install a vacuum cleaner and connect the milling head tube.
Connect power supply cable 3 phases 230V: