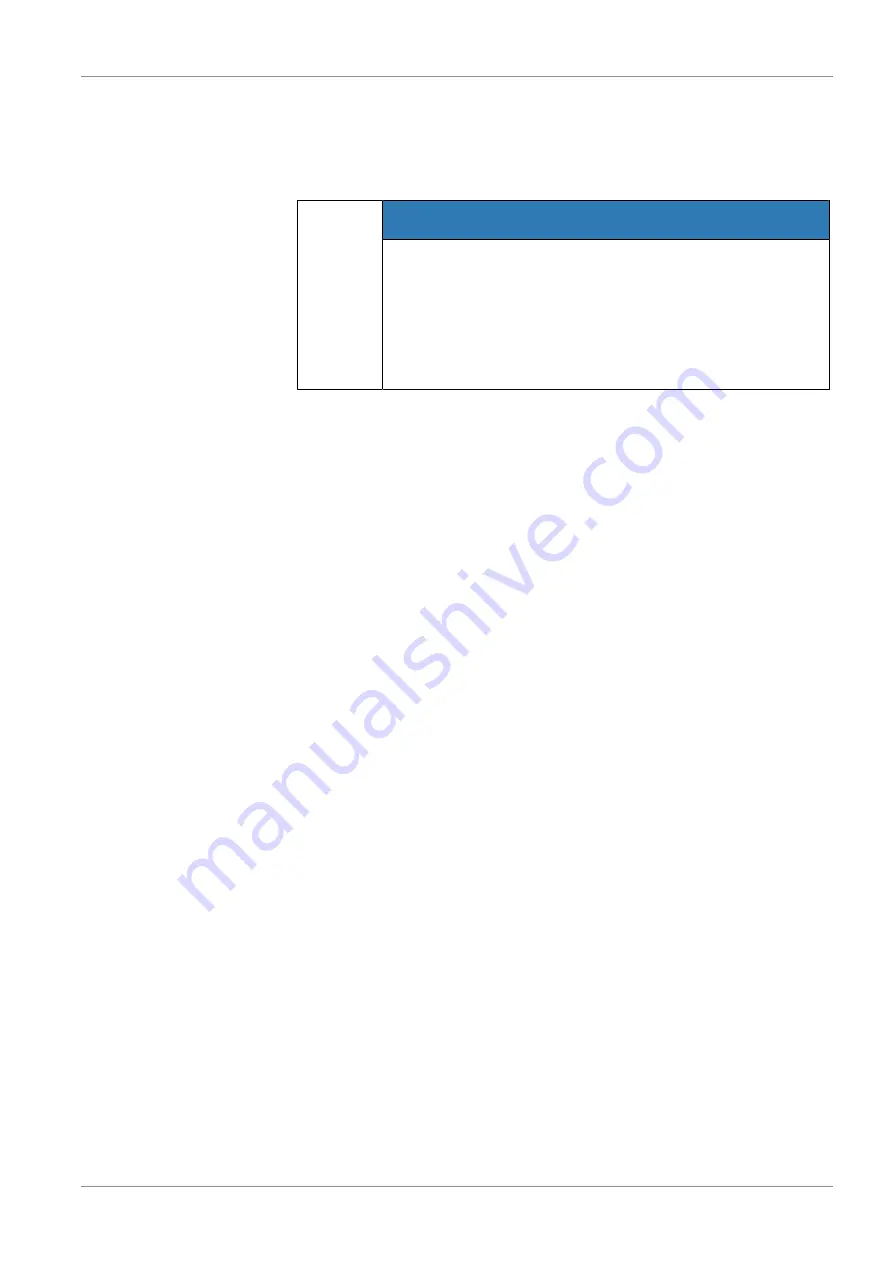
Erme AG
Maintenance | 10
Table models professional
61 / 66
10.6 Description of the maintenance work
10.6.1 Service program
NOTICE
Possible damage to the vacuum pump.
Water vapour that forms during the vacuum process contaminates
the oil, diminishes the vacuum power and can result in pump
damages in extreme cases
4
Run the service program monthly.
The service program is used to remove condensate from the oil circuit. The pump is
heated to operating temperature and aerated in pulses. Slight odour emissions may
occur while the program is running. Make sure the room is sufficiently ventilated.
Proceed as follows to start the service program:
1 Press the "HOME" button.
The main menu is displayed.
2 Using the "^" and "v" buttons, select the "General settings" menu item and press
the "ENTER" button.
3 Using the "^" and "v" buttons, select the "Service program" menu item and press
the "ENTER" button.
The service program is loaded.
4 Once the corresponding information is shown on the display, start the program
by pressing the "ENTER" button.
ð
After the program has run (duration approximately 20 minutes), the machine
automatically switches into standby mode.