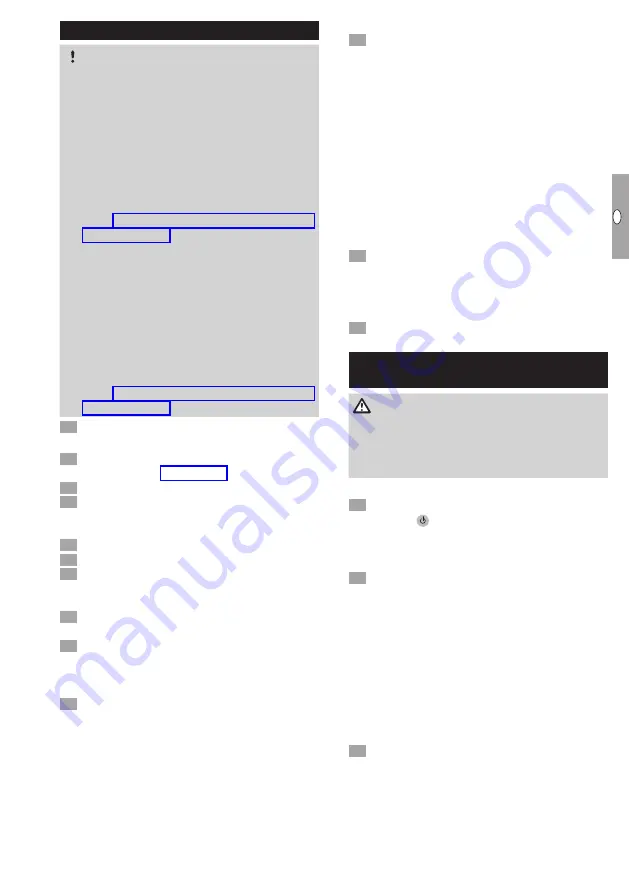
GB-19
D
GB
F
NL
I
E
Maintenance
CAUTION
To ensure that no damage occurs during operation
and maintenance, please observe the following
instructions. Otherwise, injuries or damage to the
device may occur and/or the function of the device
may be impaired. The supplier/manufacturer cannot
accept liability for damage resulting thereof.
– Have the heater cleaned at least once a year
by qualified maintenance personnel.
– Have the safety functions checked at least once
a year by qualified maintenance personnel, see
page 19 (Checking the safety functions and
burner operation).
– Check the chimney once a year with your local
chimney sweep to find whether the flue gas and
air supply routes are clear.
– Sharp-edged metal sheets. Always wear protec-
tive gloves.
– After cleaning or repair work, check that the
components on and in the heater are in good
condition. The device may only be restarted
if all safety devices have been installed and
the safety functions have been checked, see
page 19 (Checking the safety functions and
burner operation).
Switch off the burner control unit.
Visual inspection
Check all heaters for dirt and clean them accord-
ingly, see page 11 (Cleaning).
Check all heaters for damage and loose parts.
4
The rubber seals between the electrodes and
electrode plugs may be displaced by the water
jet. Check whether the seals are fitted correctly.
5
Check the wiring.
6
Check the cable glands.
7
Depending on the number of operating cycles,
we recommend that the ignition electrode and
ionization electrode are replaced once per year.
8
Check the seal on the housing cover of the burner
control unit. Replace it if necessary.
9
Check the inside of the housing cover for traces
of dust, dirt or moisture. If you find such traces,
the cause must be rectified at all times, e.g. by
sealing an open cable gland.
0
Check the cable harness and wiring for signs of
damage.
Number of operating cycles
Check the number of operating cycles (heat-
er ON): the number of operating cycles can be
displayed by pressing and holding the RESET
button. The number of operating cycles is com-
posed as follows in alternating displays:
The first character (X.) stands for X,000,000 op-
erating cycles, the second character (Y) stands
for Y00,000 operating cycles. For example, the
first character is the number 2: the unit has ex-
ceeded 2,000,000 operating cycles. The second
character is the number 3: the unit has exceeded
300,000 operating cycles. The total number of
operating cycles is composed of the numbers
2 and 3. This gives a total number of operating
cycles of 2,300,000.
Disconnect the system from the electrical power
supply.
▷
The heater may only be disconnected from the
electrical power supply once the device has been
switched off and post-cooling is complete.
4
Shut off the gas supply.
Checking the safety functions and
burner operation
WARNING
Risk of explosion!
– If these checks are not carried out, the gas
valves might remain open allowing non-com-
busted gas to escape.
Safety functions
Switch off the heater during operation. Press
ON/OFF
OFF
1
2
3
4
5
AUTO
+AUT
MODE
(RESET)
ON/OFF
O
.
▷
The flame goes out < 1 s.
▷
The main fan cools the heater down until it
reaches switch-off temperature.
Remove the valve plug on the combination con-
trol during operation.
▷
The gas valves close < 1 s.
▷
The flame goes out.
▷
The burner control unit displays the fault message
“The flame has gone out during operation”. Fault
code
F.
and
2
flash alternately.
▷
If a restart has been programmed, the burner
control unit will initially attempt to restart and
will then perform a fault lock-out. Fault code
F.
and
1
flash and indicate the fault message “No
flame has been detected during the safety time”.
Shut off the inlet pressure during operation.
▷
The burner control unit performs a safety shut-
down: the gas valves are disconnected from the
electrical power supply.
▷
The flame goes out.
▷
The burner control unit displays the fault message
“The flame has gone out during operation”. Fault
code
F.
and
2
flash alternately.