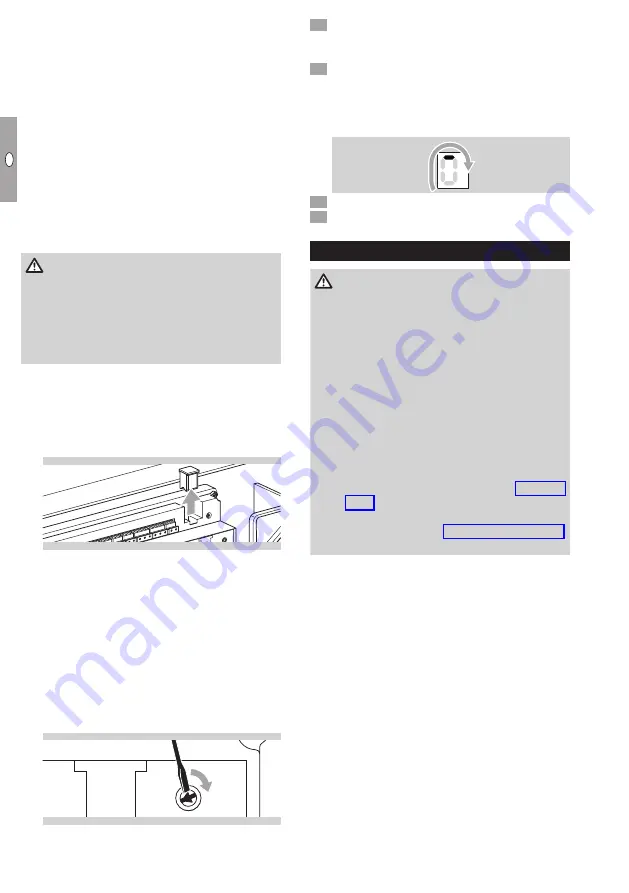
GB-6
D
GB
NL
RUS
PL
F
E
UA
CN
▷
MFA , status signal
(max. 2 A)
Possible parameterization options:
– Fault NO (default setting):
For example, the input for a horn can be set to
NO.
– Fault NC:
The input on an environmental control computer
can be set to NC (e.g. to indicate a cable dis-
continuity).
– Operation
– Standby
Burner Chip Card (BCC)
▷
All the data relevant to the device are saved
on the BCC and the internal device memory
(EEProm). In addition, the parameters are saved
on the BCC.
WARNING
Danger of electric shocks!
– Before working on possible live components,
ensure the unit is disconnected from the power
supply.
– If the BCC is removed from the burner control
unit, the heater will be non-functional.
▷
In the event of faults which cannot be rectified
by authorized trained personnel, contact the
supplier.
▷
The BCC can be removed from the burner control
unit and submitted for diagnostic purposes by
agreement with the supplier.
BCC
+
Delay
▷
If no other fault is active, the heater can be read-
ied for use again by inserting a new BCC. The
BCC must be compatible with the heater, the
version and the gas type used.
Setting the switch-on delay
▷
If multiple heaters switch on at the same time,
there can be a gas and/or power shortage on
individual devices. To avoid this happening, ad-
just the switch-on delay using the potentiometer
on the burner control unit.
▷
The potentiometer is set to 0 s at the factory.
– +
▷
If necessary, a switch-on delay of 5 to 10 s can
be set between the devices.
6
After completing the wiring, close the cover
and the housing cover on the burner control
unit again.
7
Switch on the power supply.
▷
If a switch-on delay has been programmed, a
circulating dash will be displayed when the volt-
age supply is switched on to indicate that the
switch-on delay is running.
8
Release the gas supply.
9
Commission the heater.
Commissioning
WARNING
To avoid damage to the heater, please observe
the following:
– Ensure that the heater, gas pipes, mains voltage
supply and room thermostat have been installed
by authorized trained personnel according to
the regulations.
– The Burner Chip Card (BCC) must be compat-
ible with the heater, the version, the gas type
used and the factory default parameters.
– The heater may only be operated with the gas
type specified on the type label.
–
If the device needs to be converted to be oper-
ated with a different gas type:
1. Use the correct nozzle, see page 22 (Spare
2. Set the appropriate pressure on the burner,
see table on page 8 (Adjusting the heater),
and then seal the gas pressure setting.