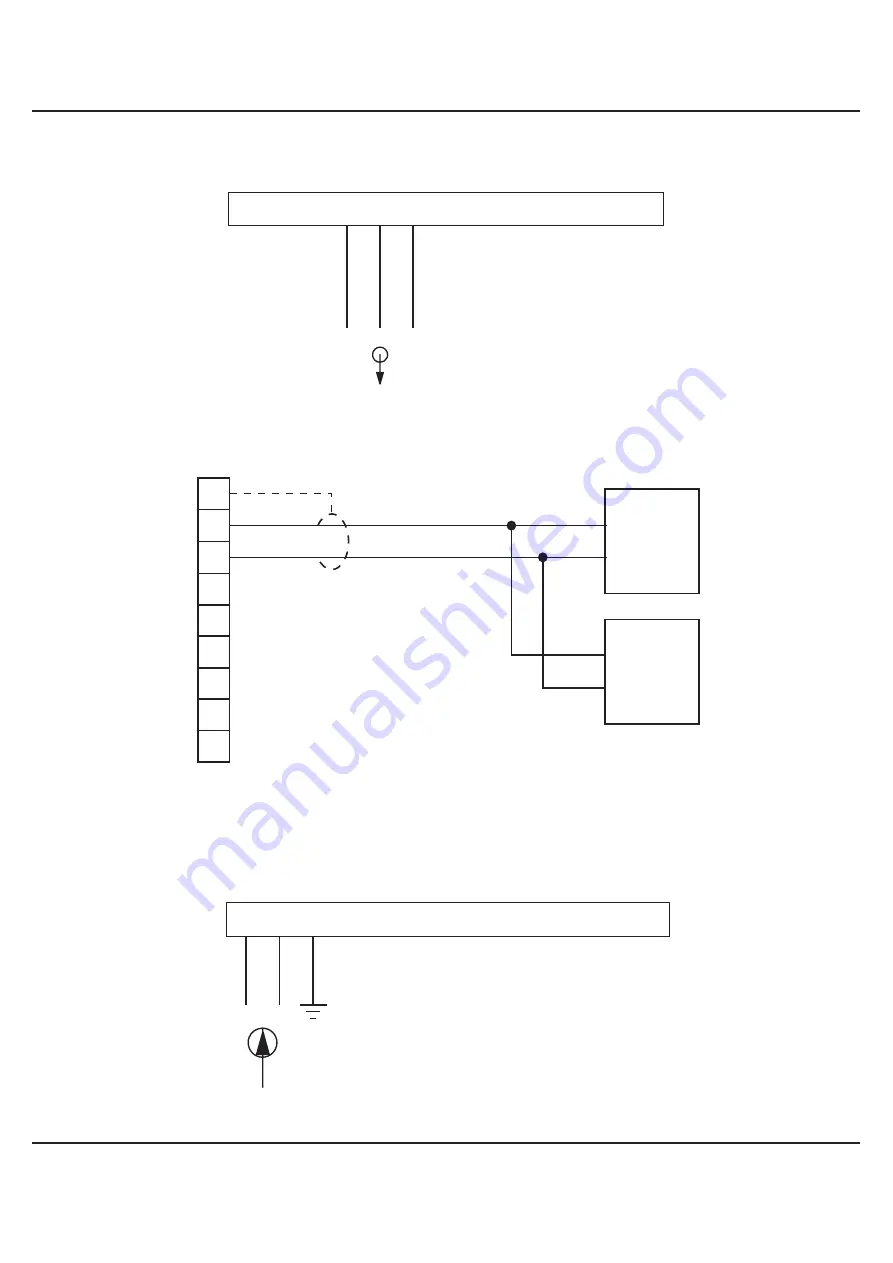
4.7.
Connection of analog output
4.8.
Connection of RS 485 interface
4.9.
Connection of power supply voltage
4.9.1. Supply voltage 18 ... 36 V DC
1
2
5
7
8
9
6
4
3
11 12
10
13
A-
AU+
AI+
1
2
5
7
8
9
6
4
3
11 12
10
13
+
-
A(+)
GND
B(-)
8
9
7
6
5
4
3
2
1
A
B
A
B
4. Electrical connections
ERMA-Electronic GmbH
10
Summary of Contents for SSI 9001
Page 38: ...13 Notices 13 Notices 37 ERMA Electronic GmbH ...
Page 39: ......