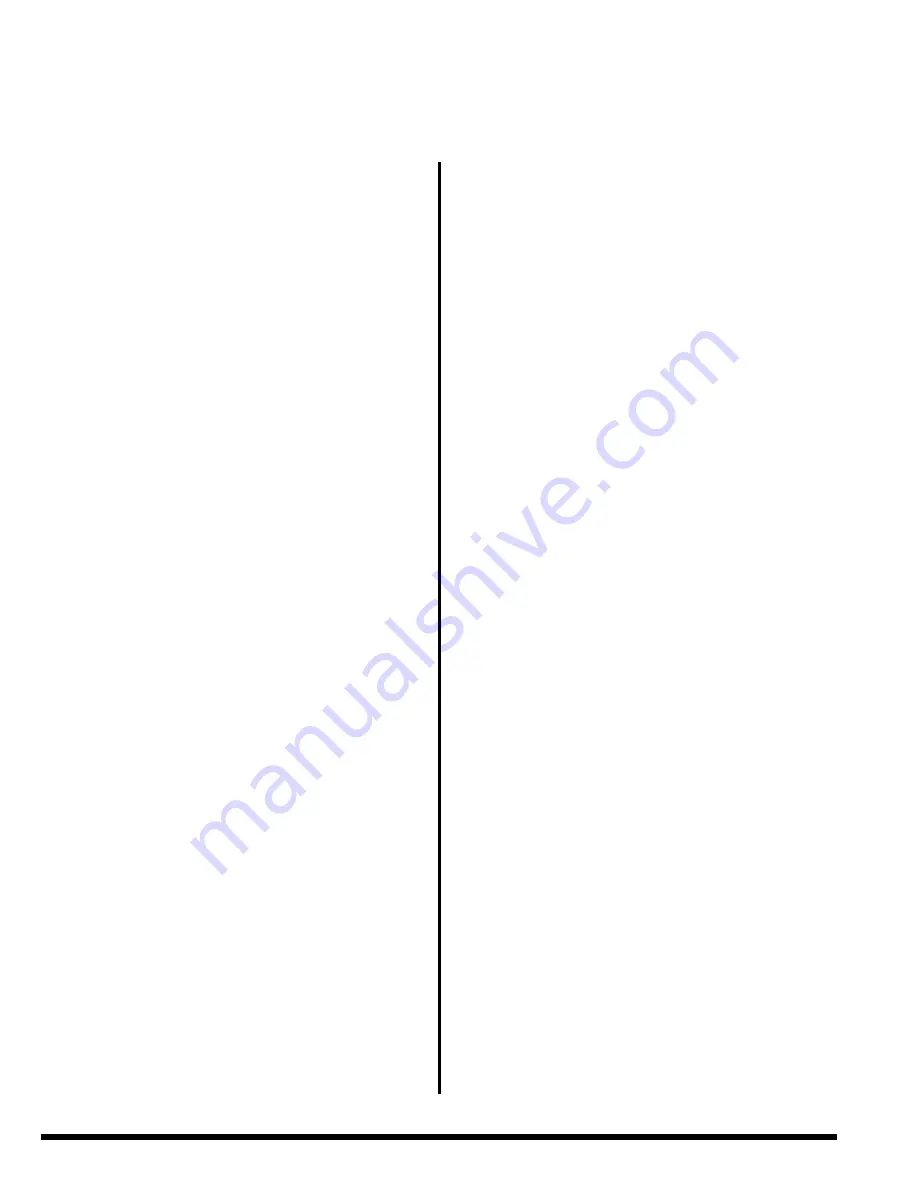
4
A. GENERAL
The Model 1250 provides protection to down stream
processing equipment by detecting the presence of
potentially damaging metal objects. It is specifically
designed for use on conveying sys tems in the food,
plastics, forest, agriculture, rubber, recycling and
mining industries.
The Detector makes use of the latest in solid state
technology, incorporating programmable logic
known as EPROM (Erasable Programmable Read
Only Memory). The design includes a number of
innovative features: self-test circuits that monitor
the performance of the detection circuitry; light
emitting diodes (L.E.D.’s) which indicate the status
of the test circuits; wide programming capability to
custom tailor the Detector to suit specific applica-
tion requirements; and solid state relays to provide
reliable arc-free switching.
B. METhOD Of OpERATION
During normal operation, the transmitter coil is
energized to produce a pulsed electromagnetic
signal. These signals produce a field that locally
permeates the conveyed material. A piece of metal
entering this field absorbs energy emitted from the
transmitter coil. The metal particle then releases the
energy and this change is detected by the receiver
coil. This technique provides opti mum discrimination
between tramp metal and the conveyed material;
product effect is non-existent or minimal.
Having detected metal by a waveform change, the
signal generated is amplified and filtered. The sig-
nal is then compared to a threshold determined by
the size of metal that must be detected. When the
signal exceeds this threshold, the Detector, at the
appropriate time, triggers solid state relays. These
solid state relays in turn switch the line voltage
to the Detector’s output alarm terminals. Various
combinations of alarm horns, belt stop relays, alarm
beacons, etc., can then be activated by the switched
alarm outputs
The Detector is influenced only by change. There-
fore, stationary structural members, metal belt cores,
symmetrical idlers and other objects which do not
represent a moving mass to the field are not detect-
ed. Metal belt repair clips are passed by the unit with
an optional clip detector sensor and inhibitor circuit
which is properly adjusted to the clip signal.
C. phySICAL DESCRIpTION
MAIN CONTROL ENCLOSURE
This enclosure houses and protects the Electronic
and Interface Modules and also serves as a junc-
tion box for conduit and cables running to and from
the Detector. As standard, the control is housed in
a steel NEMA 4 enclosure. Other en closures are
available as options.
Visible and accessible on the front panel are:
Power On/Off Switch, Green Power “ON” Indicator
Lamp, Red Trip Indicator Lamp that lights when
the unit has detected metal and a Reset Button.
See Figure 1.
Type: JIC NEMA 4
Size: 16" x 14" x 6" (406 x 356 x 152 mm)
Weight: 33 Lbs (15 kg) (Includes All Electronics)
ELECTRONIC/LNTERfACE MODULES
All the electronics and controls for the Detector
are contained in two modules, the Interface Module
and the Electronic Module shown in Figure 2. The
Electronic Module houses the elec tronic circuitry
and components associated with metal signal
processing and analysis. Visible on the front panel
of the Electronic Module are the metal sensitivity
control knob, clip override control knob and L.E.D.
status indicators used to monitor the status of the
Detector’s self-test circuits. By removing the front
panel of the module, all of the electronics are ex-
posed for calibration and troubleshooting. All con-
nections for the Electronic Module are made through
a 36-pin connector located along the bottom edge
of the module. When the modules are in place, this
connector mates with a connector on the Interface
Module.
part I - Operation & Description
Summary of Contents for 1250 ANALOG
Page 6: ...6 Part I Operation Description cont FIGURE 1 MAIN CONTROL ENCLOSURE NEMA 4 4X 7 OR 9...
Page 7: ...7 Part I Operation Description cont FIGURE 2 ELECTRONIC MODULE...
Page 11: ...11 Part II Installation cont FIGURE 3 SWING AWAY FRAME ASSEMBLY FIGURE 4 FIXED FRAME ASSEMBLY...
Page 13: ...13 Part II Installation cont...
Page 20: ...20 TABLE 6 PROGRAMMING CONTROLS SUMMARY Part IV System Programming cont...
Page 21: ...21 Part IV System Programming cont...
Page 23: ...23 Part V Troubleshooting cont TABLE 7 ELECTRONICS MODULE STATUS INDICATOR SUMMARY...
Page 24: ...24 Part V Troubleshooting cont FIGURE 5 PROGRAMMING CONTROLS AND TEST POINT LOCATIONS...
Page 25: ...25 Part V Troubleshooting cont TROUBLESHOOTING FLOW DIAGRAM 1 INSUFFICIENT METAL SENSITIVITY...
Page 26: ...26 Part V Troubleshooting cont TROUBLESHOOTING FLOW DIAGRAM 2 FALSE TRIPPING...
Page 27: ...27 Part VI Maintenance 1 10 Amp Fuse 2 Spare Bulbs 1 1 16 Allen Key Wrench 1 5 64 Allen Key...