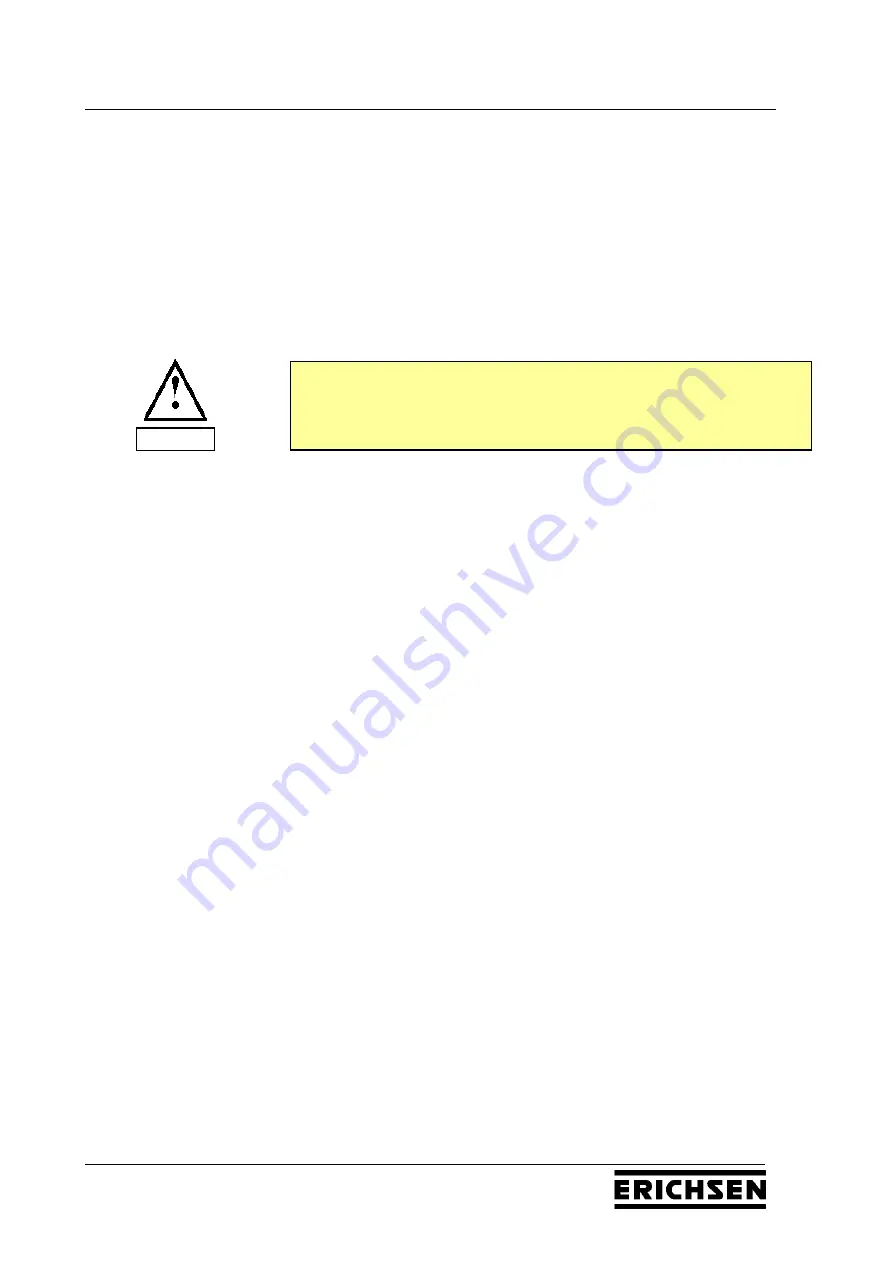
Scratch Hardness Tester LINEARTESTER 249
8
BAE 249
2.4
Dangers from Electrical Energy
Work on the electrical supply may only be done by
qualified
electrician.
The electrical equipment of the instrument must be checked
regularly. Loose connections and cable damaged by heat
must be corrected immediately.
2.5
Points of Special Danger
2.6
Care, Maintenance, Correction of Faults
Carry out maintenance and inspection at the correct
intervals.
Inform operating personnel before starting with
maintenance or repair work.
The instrument must be isolated from the elctrical supply
whenever maintenance, inspection or repair work is done.
2.7
Modifications to the Equipment
No modifications or additions or alterations to the instrument
may be made without permission from the manufacturer.
All measures involving modifications require written
confirmation of approval from ERICHSEN GmbH & Co. KG
Instruments not in fault-free condition must be switched off
immediately.
Use only replacement parts from the original supplier.
- If parts from other sources are used there is no guarantee
that they are designed to take the loading and meet the
safety requirements.
2.8
Cleaning of the Instrument and Disposal of Materials
Materials must always be used and disposed of correctly.
This applies particularly when cleaning with solvents.
There is a special point of danger in the working area of the
instrument
:
Do not move hands into the radius of action of the working
stylus.
Danger