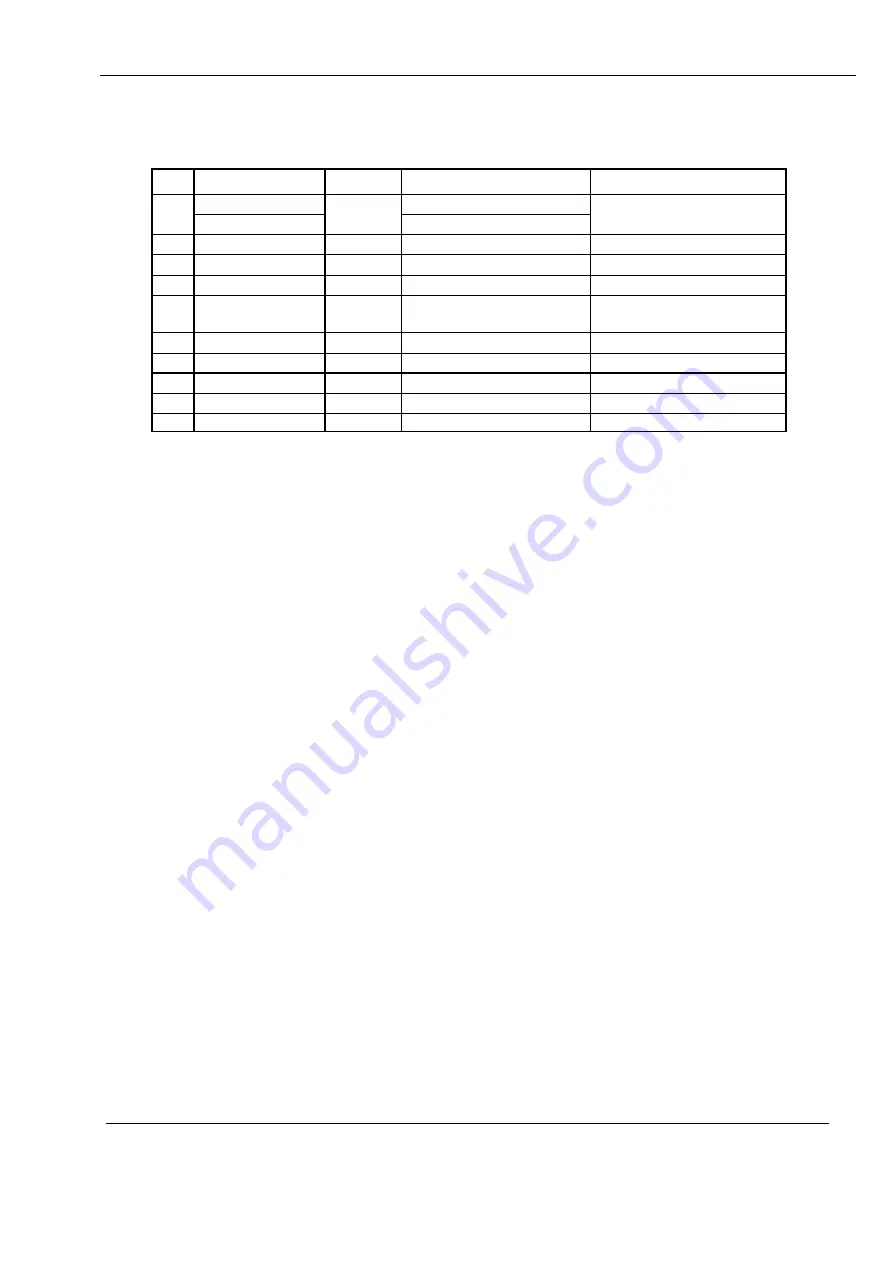
Operating Instructions for ERHARD NON SLAM Nozzle Check Valve
Parts list for ERHARD NON SLAM Nozzle Check Valves DN 350 – 600
with standard materials
Item Description
Qty.
Material
Notes
Body 350 - 400
EN-JS1030
Body 500 - 600
EN-JS1025
2
Internal body
1
2.1050.01
zinc-free bronze
3
Threaded pin
4
A4
stainless steel
4
Bush
8
High-performance polymer
5
Piston ring
1
1.4404/EPDM
vulcanised
EPDM
rubber-
coating
6
Guide rod
4
1.4057.05
stainless steel
7
Pressure spring
4
1.4310.07
stainless steel
8
Threaded bush
4
A4
stainless steel
9
Washer
4
NBR or EPDM
10
Cover
1
2.1050.01
zinc-free bronze
ductile cast iron
1
1
Corrosion protection for DN 80 – 600:
The body is internally vitreous-enamelled and externally EKB coated (synthetic epoxy
coating). All other parts are made of stainless materials.
Recesses are provided at the centering of the internal body in the main body so that the
transitions between the uncoated and coated surface can be filled with sealing agent.
This protects and seals these critical areas against the flow medium.
1.3 Performance and Mode of Operation
The ERHARD NON SLAM Nozzle Check Valve is a flow-controlled non-return valve
with centrally and axially moved obturator. This obturator with the shape of a valve disc
(DN 80 – 300) or a valve ring (for DN 350 and larger) is guided by means of one (four) a
guiding stem(s) in an internal body. The closing movement of the valve is spring-
assisted (one or four springs).
The ERHARD NON SLAM Nozzle Check Valve is resilient-seated, with tight closure
according to DIN EN 12266 / 1074 – leakage rate 1 (0 drop per minute), at a minimum
back pressure of 4.0 mWC (400 mbar) and larger for DN 80 – 300 and a minimum back
pressure of 8.0 mWC (800 mbar) and larger for DN 350 – 600.
The valve starts opening at incipient velocity and is fully open at a velocity of approx. 2
m/s. The opening process can be influenced by a special spring which is designed for
special cases of application.
The standard design is suitable for installation in horizontal pipeline and for vertical
pipeline and for vertical upward flow. When the valve is installed in a vertical pipeline
with downward flow, the ERHARD NON SLAM Nozzle Check Valve has to be equipped
with a special spring. Moreover, a remachined internal body is used which is designed
with additional bores for drainage of the internal body (see fig. 1.1 and 1.2).
BA43E000
Juli 2009
Rev.9
ERHARD GmbH & Co. KG
x
D-89502 Heidenheim
x
Postfach 1280
Telefon: (07321) 320-0
(07321) 320 491 E-Mail: info
@
erhard.de
Internet: http://www.erhard.de
Page 8 of 18