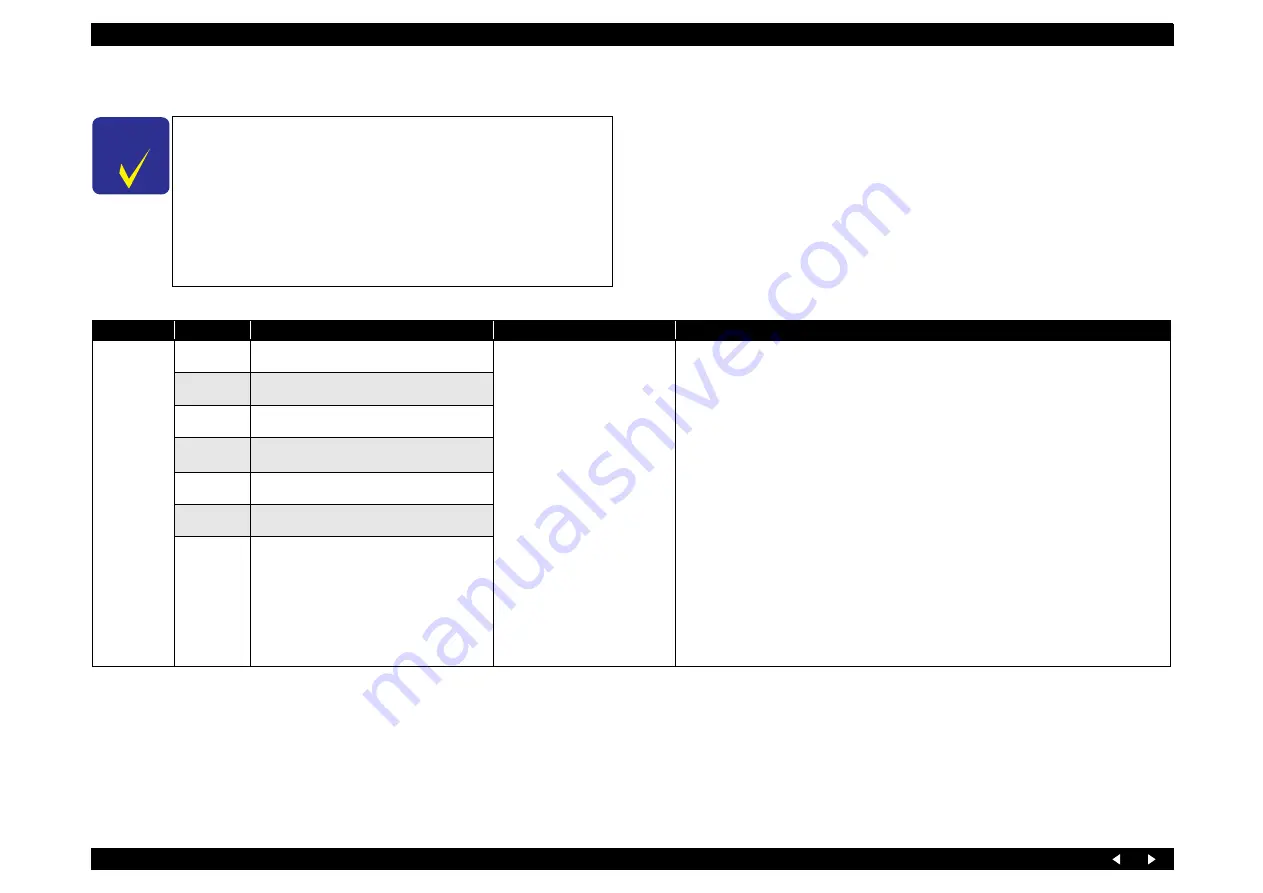
Troubleshooting
Troubleshooting When There is Error Display
3.2.3 FATAL Error
C H E C K
P O I N T
The EEPROM (Address: 3CH) stores the error code of the
latest fatal error.
The latest fatal error can be identified using the adjustment
program.
In case any fatal error (such as memory check) other than those
in the Printer Mechanism occurs, all the LEDs (x5) flash
without any indication on the LCD. Pressing the Change View
button during flashing will display the error code, so that you
can identify the error from the error code.
Table 3-3. Fatal Errors
Category
Error Code
Error
Cause
Remedy
DC error
(CR motor)
01H
CR PID speed over error
An error occurred in the CR
motor operating sequence
Checking the operation of the Carriage Assy;
Move the Carriage Assy by hand, and check to see if it moves smoothly.
Making the following adjustments
♦
Bi-D
♦
Paper feed length with PF Assy
♦
Paper feed length with Eject Assy
♦
PW adjustment
Checking the following parts and replacing the defective one
♦
Checking the head FFC (CN6/7) for disconnection or breakage
♦
Checking the lead wires of the CR Motor (CN3)
for disconnection or breakage
♦
Checking the CR Encoder FFC (CN6) for disconnection or breakage
♦
Checking the printer frame for adhesion of dirt or insufficient lubrication
♦
Checking the CR Guide Shaft for adhesion of dirt or insufficient lubrication
♦
Checking the Linear Scale for adhesion of dirt or damage
♦
Checking the CR Encoder for adhesion of dirt or damage
♦
Checking the PW Sensor for adhesion of dirt or damage
♦
Checking the CR Belt for damage or improper tension
♦
Checking the CR Motor and replacing it if necessary
♦
Main Board
♦
Power Supply Board
02H
CR load positioning lock error
08H
CR PID reverse rotation detection error
0AH
CR load positioning accumulation moving
distance error
0BH
CR load positioning speed over error
0CH
CR PID lock error
0DH
CR PID aveTi max error
Summary of Contents for Stylus Photo RX640 series
Page 1: ...EPSON StylusPHOTORX640 650 Scanner Printer Copier SERVICE MANUAL SEMF05003 ...
Page 8: ...C H A P T E R 1 PRODUCTDESCRIPTION ...
Page 15: ...C H A P T E R 2 OPERATINGPRINCIPLES ...
Page 19: ...C H A P T E R 3 TROUBLESHOOTING ...
Page 40: ...C H A P T E R 4 DISASSEMBLYANDASSEMBLY ...
Page 71: ...C H A P T E R 5 ADJUSTMENT ...
Page 77: ...C H A P T E R 6 MAINTENANCE ...
Page 82: ...C H A P T E R 7 APPENDIX ...
Page 87: ...Model PM A890 Stylus PHOTO RX640 650 Board C608Main Sheet 1 3 Rev D ...
Page 88: ...Model PM A890 Stylus PHOTO RX640 650 Board C608Main Sheet 2 3 Rev D ...
Page 89: ...Model PM A890 Stylus PHOTO RX640 650 Board C608Main Sheet 3 3 Rev D ...
Page 90: ...Model PM A890 Stylus PHOTO RX640 650 Board C608PNL Sheet 1 1 Rev A ...
Page 91: ...Model PM A890 Stylus PHOTO RX640 650 Board C608PNL B Sheet 1 1 Rev C ...
Page 92: ...Model PM A890 Stylus PHOTO RX640 650 Board C608PSB Sheet 1 1 Rev B ...
Page 93: ...Model Stylus PHOTO RX640 650 Board C608PSE Sheet 1 1 Rev B ...
Page 94: ...Model PM A890 Stylus PHOTO RX640 650 Board C608ISN Sheet 1 1 Rev D ...
Page 96: ...400 100 101 PM A890 EPSON Stylus Photo RX640 650 No 1 REV 01 C608 ACCE 001 ...
Page 98: ...544 202 110 109 108 300 200 PM A890 EPSON Stylus Photo RX640 650 NO 3 REV 01 C608 ELEC 001 ...