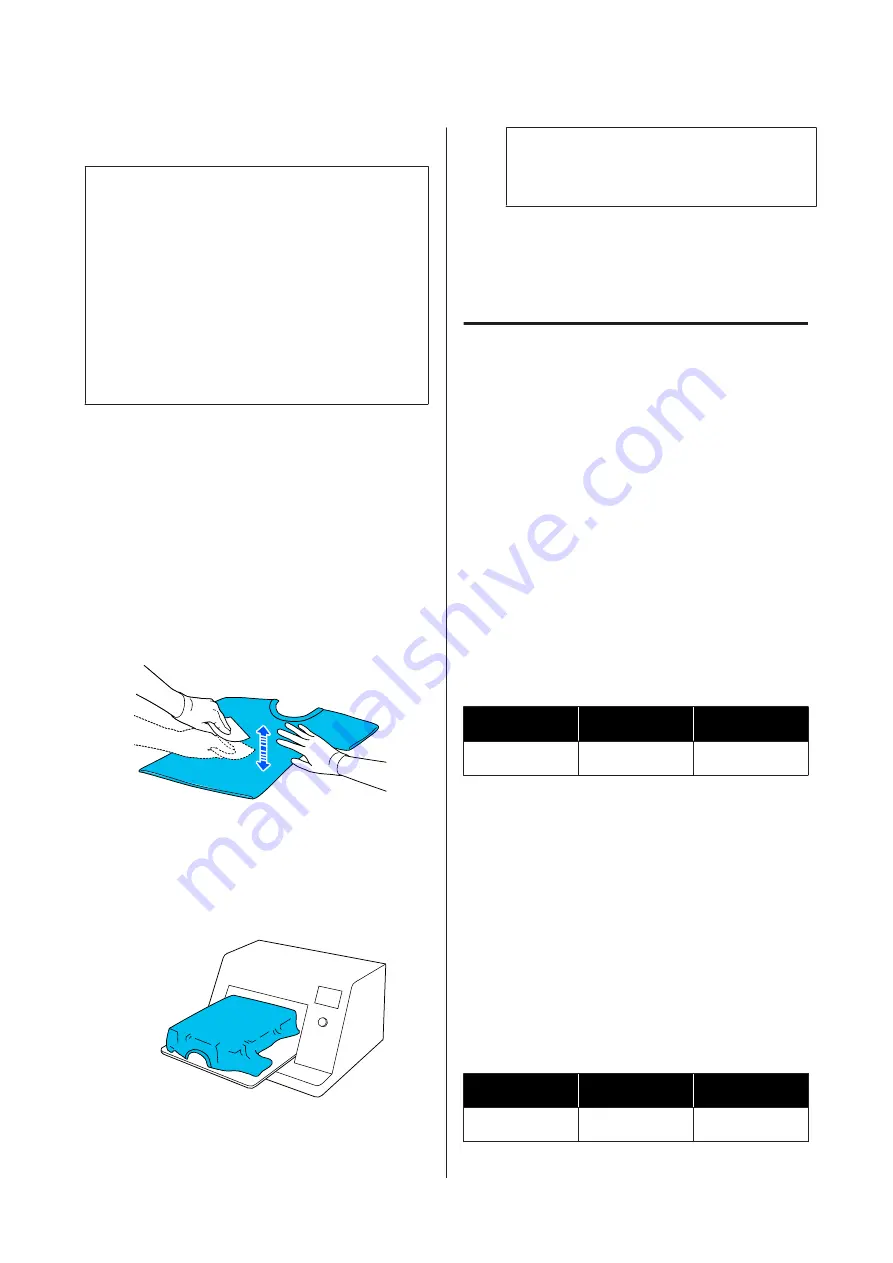
Applying with a sprayer
c
Important:
Depending on the type of sprayer, it may create a
mist when applying the pre-treatment liquid. Wear
a mask, protective eye-wear, and gloves as required,
and make sure the area is well ventilated while
working with the pre-treatment liquid.
Mist could also enter the printer which could cause
a breakdown or malfunction to occur. If necessary,
install the sprayer at a location away from the
printer.
For details on using the sprayer, see the manual supplied
with the sprayer.
A
Pour the pre-treatment liquid into the sprayer.
B
Spread out the T-shirt on a flat surface.
C
Use sticky tape (a roller) and so on to remove lint
from the area to which you will apply the
pre-treatment liquid.
D
Load the T-shirt into the sprayer, and then spray
the pre-treatment liquid evenly over the printing
surface.
We recommend applying to an area larger than
the target print area.
Note:
You can apply the liquid evenly if you run the roller
over the area after spraying.
E
Fix the pre-treatment liquid with the heat press.
U
“Fixing the pre-treatment liquid” on
Fixing the pre-treatment liquid
Use the heat press to remove creases from the T-shirt
and to fix the pre-treatment liquid. Because the oven
does not press the fibers down, the printed surface does
not become even which causes creases and unevenness
in color. When fixing the pre-treatment liquid by using
a heat press, place a heat-resistant release sheet, such as
silicone paper, between the T-shirt and the surface of the
press to prevent the pre-treatment liquid from sticking
to the surface of the press.
As the optimum conditions vary depending on the
amount of pre-treatment liquid, the following values are
only a guide.
Fixing conditions for cotton
pre-treatment liquid
Temperature
Time
Pressure
*1
170 ˚C
45 seconds
*2
4.2 N/cm
2
*1
The optimum conditions vary depending on the
type of heat press such as the manual adjustment
type. Be sure to test the ink fixing result in advance
to find the right pressure.
*2
If the application area for the pre-treatment liquid
is larger than A4, it may not dry even after 45
seconds. Try extending the time up to 90 seconds
while checking if the pre-treatment liquid is dry.
Fixing conditions for polyester
pre-treatment liquid
Temperature
Time
Pressure
*1
130 ˚C
60 seconds
*2
3.0 N/cm
2
SC-F3000 Series User's Guide
Basic Printing
44