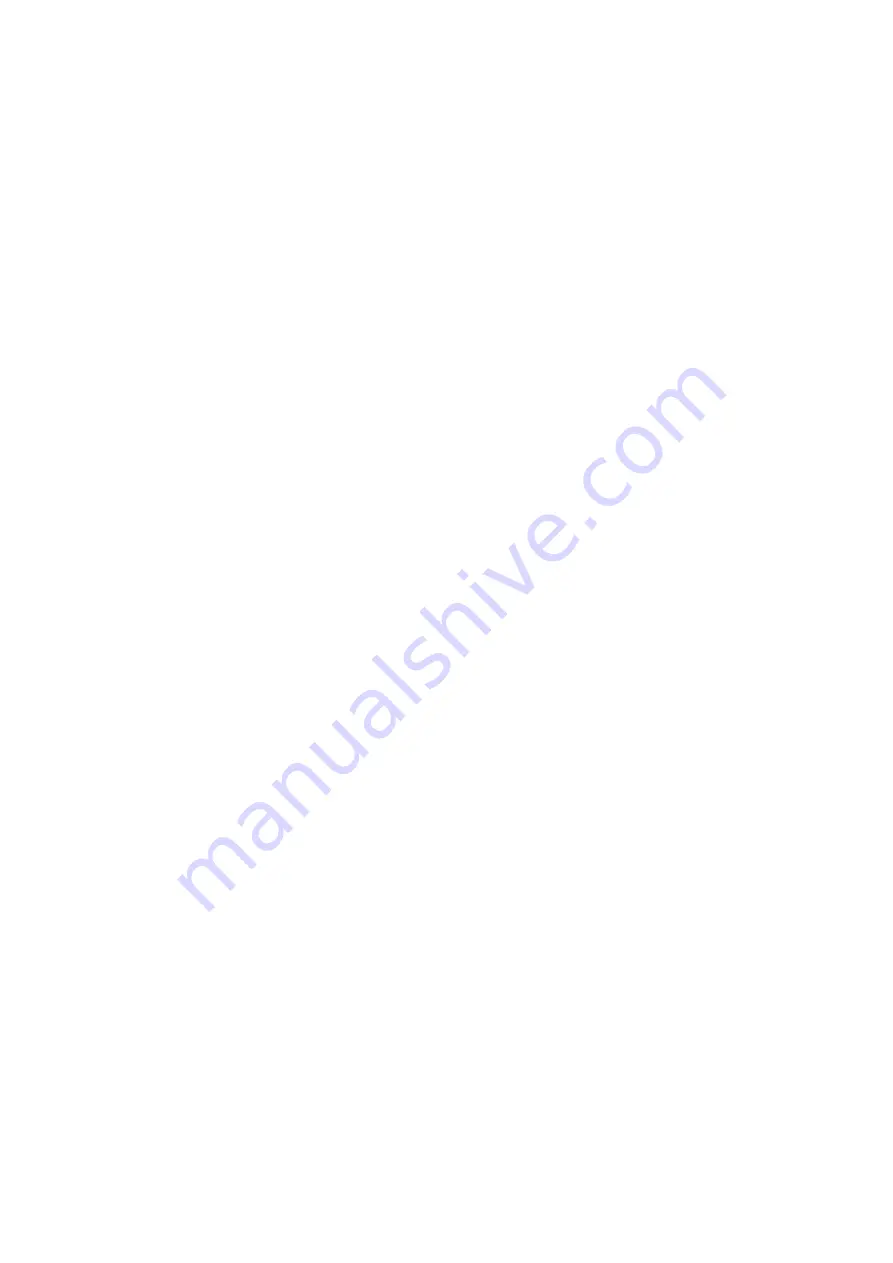
26
• Check hydraulic oil for condensed water and replace if necessary.
• Start up the truck (see 3.2 Operate and run the truck P13).
lf there are switching problems in the electrical system, apply contact spray to the
exposed contacts and remove any oxide layers on the contacts of the operating
controls by applying them repeatedly.
Perform several brake tests immediately after re-commissioning the truck.
5.5
Safety checks to be performed at regular intervals and following any
unusual incidents
Carry out a safety check in accordance with national regulations. We have a special
safety department with trained personnel to carry out such checks. The truck must be
inspected at least annually (refer to national regulations) or after any unusual event by
a qualified inspector. The inspector shall assess the condition of the truck
trom
purely
a safety viewpoint, without regard to operational or economie circumstances. The
inspector shall be sufficiently instructed and experienced to be able to assess the
condition of the truck and the effectiveness of the safety mechanisms based on the
technica! regulations and principles governing the inspection of Pallet trucks.
A thorough test of the truck must be undertaken with regard to its technica! condition
trom
a safety aspect. The truck must also be examined for damage caused by possible
improper use. A test report shall be provided. The test results must be kept for at least
the next 2 inspections.
The owner is r sponsible for ensuring that faults are immediately rectified.
A test plate is attached to the truck as proof that it has passed the safety inspection.
This plate indicates the due date for the next inspection.
5.6
Final de-commissioning, disposal
Final, proper decommissioning or disposal of the truck must be performed in
accordance with the regulations of the country of application. In particular, regulations
governing the disposal of batteries, fuels and electronic and electrical systems must
be observed.