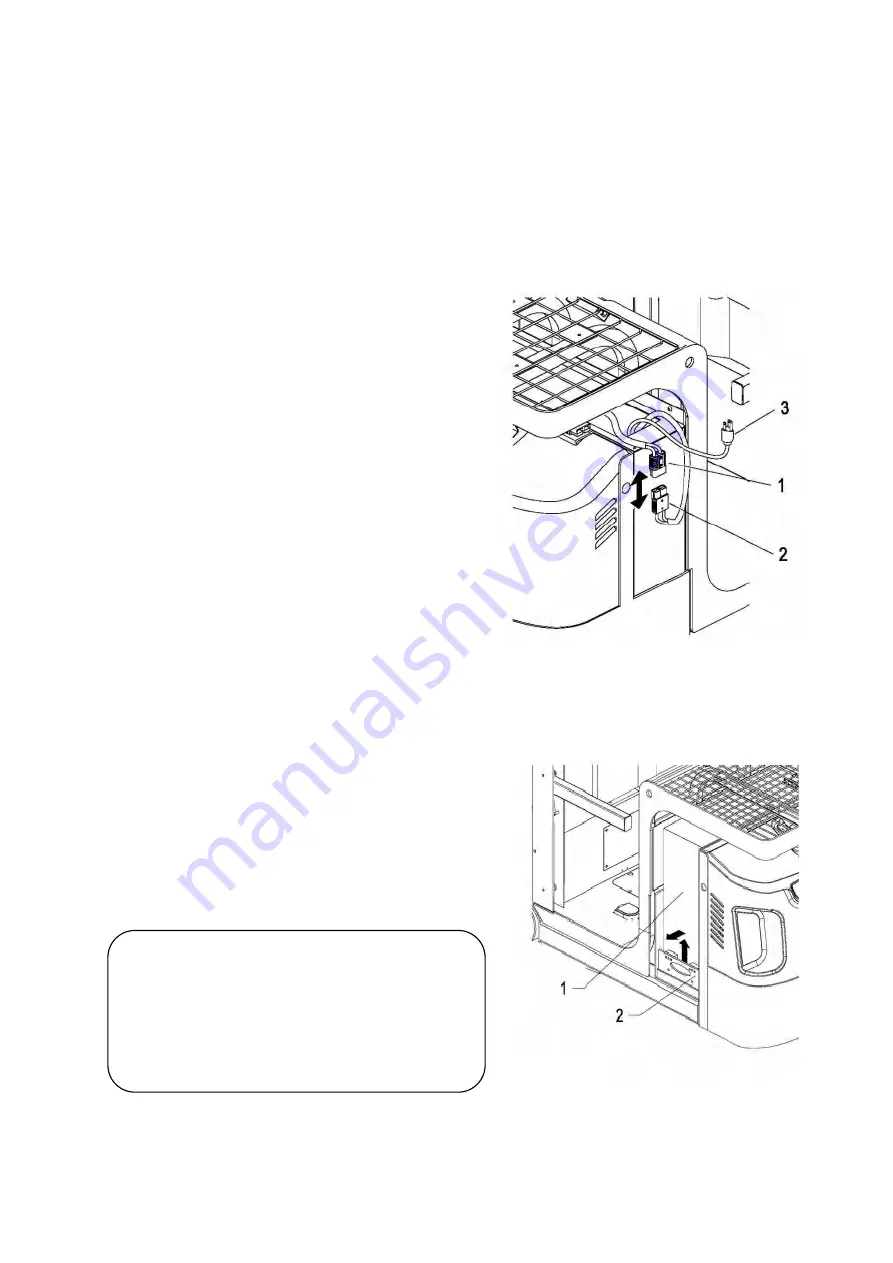
26
4.3Charging the battery
Safety regulations for Charging the battery
• Before charging, check all cables and plug connections for visible signs of damage.
• Before start and finish charging to make sure power is turn OFF.
• It is essential to follow the safety regulations of the battery and charging station
manufacturers.
Charging step
• Check whether the condition is according with
"Safety regulations for Charging the battery".
• Park the truck securely(See 3.5 Parking the
truck securely Page20 ).
• Open the cover plate of the battery.
• Remove the plug (1).Connect the plug (1) with
the charger (2).
• Connect the battery plug (3) with the charging
lead of the stationary charger and turn on the
charger.
4.4 Battery removal and installation
• Park the truck securely(See 3.5 Parking the truck securely Page 21 ).
• Place the battery plug or the battery cable in such a way that they will not get caught
on the truck when the battery(1) is removed.
• .Remove battery baffle(2).Pull the battery out
from the side.
• Installation is in the reverse order of operations.
CAUTION!
The stacker must be parked on level ground.
When transporting batteries using a crane,
ensure that the crane is of adequate Capacity.
The lifting gear must exert a vertical pull so
that the battery container is not compressed.
Summary of Contents for 508000003143
Page 1: ...I Part No 508000003143 V1 10 2019 ...
Page 14: ...7 J1HD ...
Page 15: ...8 1 4 Identification points ...
Page 19: ...12 3 2 Controls and Displays 3 2 1 Control panel controls and displays ...
Page 31: ...24 ...
Page 39: ...32 5 3 2 Lubrication Schedule ...