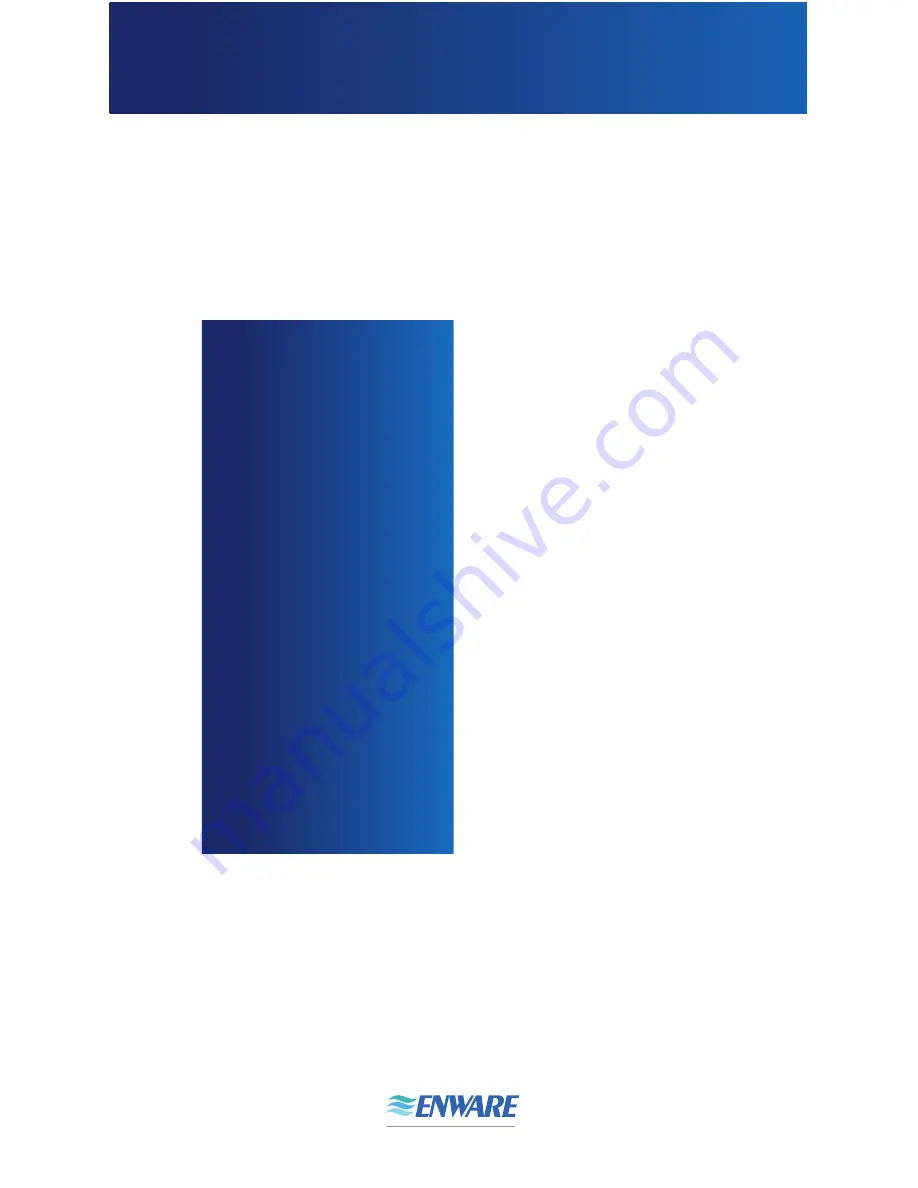
www.enware.com.au
Call 1300 369 273
2
PRODUCT FEATURES
Complies with the
requirements of AS4032.1
-Thermostatic Mixing
Valves
Provides high stability of
mixed water temperature
even under changing inlet
conditions
Ensures rapid shut down
of mixed outlet flow in the
event of hot or cold water
supply failure
Designed for quick and
simple in-situ servicing
Suitable for installation into
AS3500 compliant systems
with hot water temperature
as low as 55°C for
temperature differential
Fitted with a Tamper
Resistant temperature
adjustment mechanism
installing
confidence
Enware reserves the right to change any product specification or information
contained in this publication, at any time and without notice. Every care
has been taken to ensure accuracy in the Preparation of this publication
which has been issued for guidance only. No liability can be accepted for any
consequences which may arise as a result of its application. Enware = trade
mark of Enware Australia Pty Limited.
Aquablend TMV’s are exclusively manufactured for Enware Australia Pty Limited
by Reliance Worldwide, 27-28 Chapman Place, Eagle Farm, Qld, 4009 Australia.
The ENWARE AQUABLEND 2000
Thermostatic Mixing Valve is a
high performance Thermostatic
Mixing Valve suitable for a wide
range of applications. The valve
is designed to comply with
AS4032.1 - Thermostatic Mixing
Valves.
AQUABLEND 2000 THERMOSTATIC MIXING VALVE
CONTENTS
SAFETY
page 3
PRODUCT DESCRIPTION
page 4
RECOMMENDED PRESSURES
AND TEMPERATURES
page 7
FLOW SIZING GRAPH
page 8
INSTALLATION
page 9
COMMISSIONING OF THE VALVE
page 12
MAINTENANCE & SERVICING
page 15
TROUBLE SHOOTING
page 17
SPARE PARTS
page 19
COMMISSIONING REPORT
page 20
SERVICING REPORT
page 23
WARRANTY
page 26
Summary of Contents for aquablend 2000
Page 28: ......