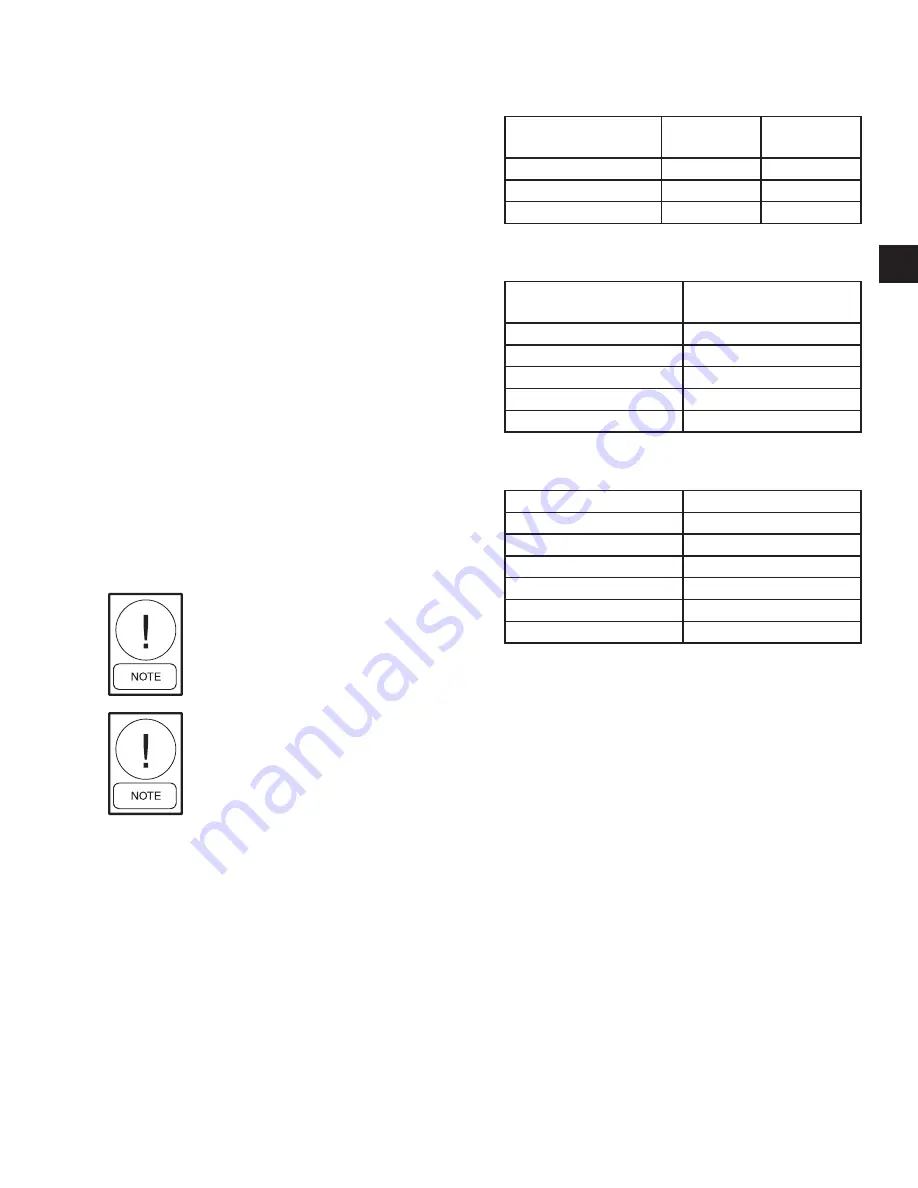
4
3.
Use a portable vacuum with HEPA filtration to re
-
move the loose dirt and organic matter. The filter
should be 99.97% efficient at .3 micron particle
size.
4. If no microbial growth (mold) exists, thoroughly
clean the fan and associated components with an
industrial cleaning solution. Carefully follow the
cleaning solution manufacturer instructions re-
garding use and disposal of their product.
5. If microbial growth (mold) is present remove the
contamination, and thoroughly clean the affected
area with an EPA-approved sanitizer specifically
designed for HVAC use. Carefully follow the san-
itizer manufacturer instructions regarding the use
and disposal of their product.
6. Rinse the affected surfaces thoroughly with fresh
water and a fresh sponge to prevent potential cor-
rosion of metal surfaces.
7. Allow the unit to dry completely before putting it
back into service.
8. Use caution to assure that any contaminated ma-
terial does not contact other areas of the unit or
building.
Properly dispose of all contaminated ma-
terials and cleaning solutions.
Important: If the microbial growth (mold)
was found, the cause of the contamination
must be determined and action taken to
assure it does not reoccur.
Fan Bearings
Bearing Set Screw Alignment
Align bearing setscrews. See
Table 1 on page 22
for
bearing setscrew torque.
Fan Bearings should be lubricated with a lithium base
grease which conforms to NLGI Number 2 for consis-
tency. See
Table 2 on page 23, Table 3 on page 23,
and Table 4 on page 23
for recommended greasing
intervals, operating range, and bearing grease capacities.
TABLE 2 -
RECOMMENDED GREASING
INTERVALS OF FAN BEARINGS
OPERATING
CONDITIONS
-20°F TO
+140°F
140°F TO
200°F
Clean, Dry
3-6 months
1-3 weeks
Dirty, Dry
1-3 months
1-4 weeks
Dirty, Wet, High Humid
1-4 weeks
1-14 days
TABLE 3 -
RECOMMENDED GREASES FOR VARI-
OUS OPERATING RANGES
RECOMMENDED
GREASES
RECOMMENDED OPER-
ATING RANGE
Texaco-Multi Fak #2
-20°F to +250°F
Shell Alvania #2
-20°F to +250°F
Mobil Mobilux #2
-20°F to +250°F
Exxon Unirex #2
-20°F to +250°F
Exxon Beacon
-65°F to +250°F
TABLE 4 -
FAN BEARING MAXIMUM GREASE
CAPACITY
SHAFT SIZE IN INCHES
CAPACITY IN FL. OZ.
1/2 – 3/4
1/8
7/8 – 1-3/16
3/8
1-1/4 – 1-1/2
5/8
1-11/16 – 1-15/16
7/8
2 – 2-7/16
1-1/4
2-1/2 – 2-15/16
2
Lubricating the Fan Bearing
To lubricate the fan bearing, complete the following:
1. Disconnect all electrical power to the unit, tag and
lock out power source.
2. Check grease lines for tight connections at the
grease fitting.
3. Using a manual low-pressure grease gun, add
grease until a light bead appears at the bearing
grease seal. Turn the fan wheel manually while
adding grease.
Motor
General Inspection
Inspect the motor at regular intervals, approximately
every 500 hours of operation or every three months,
which ever occurs first. Operating conditions will vary
the frequency of inspection and lubrication. Table
5 (
Table 5 on page 25)
lists recommended motor
ENVIRO-TEC
23
SECTION 4 - PERIODIC MAINTENANCE AND SERVICE
FORM ET102.19-NOM1 (0521)