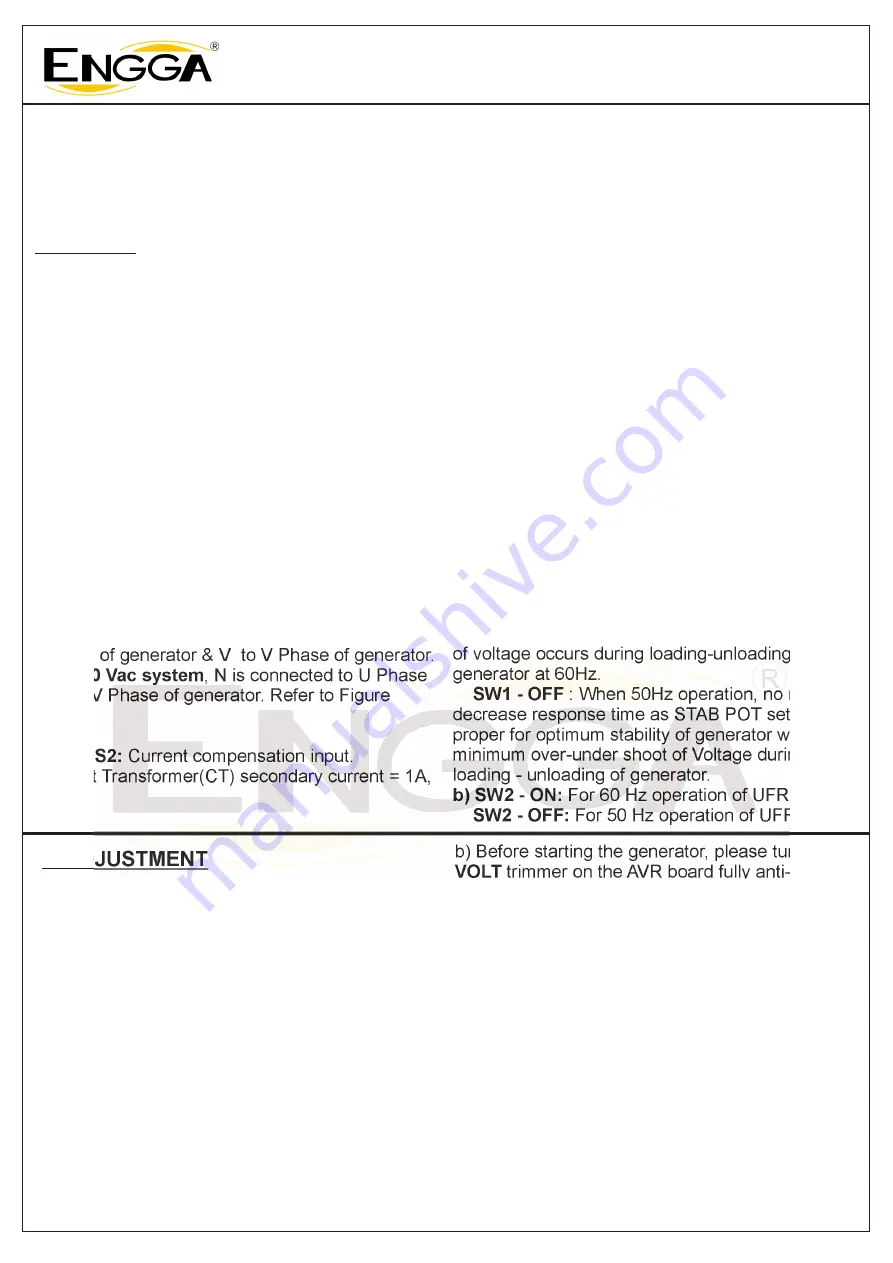
OPERATING MANUAL FOR AUTOMATIC VOLTAGE REGULATOR
MODEL NO : EVC300i
AVR can be mounted directly on the generator, switchgear or control panel that conforms to the
mounting specification.
All voltage readings are to be taken with an average-reading voltmeter. Meggers and high-potential test
equipment must not be used with AVR connected to generator. Use of such equipment could damage
the AVR.
5. WIRING
1. V - V
- V
: Sensing Input Voltage.
V
output voltage 220Vac
output voltage 400Vac
2. F+. F- : Excitation Output
3. Power Input:
For 400 Vac system
For 220 Vac system
4. S1 - S2:
220
380
Sensing Input is between
&
(220Vac) or
&
(400VAC). For 2 Phase sensing one
phase is connected to
terminal of AVR and
second phase is connected to
or
as
explained below:-
- For generator
, connect
sensing phase to terminal
.
- For generator
, connect
sensing phase to terminal
.
The sensing should be connected
“
Line to Line
”
from generator output. Refer Figure 3 & 4.
.
Connect the brushless exciter field to terminals F+
and F-. Be sure to observe polarity.
AVR power input is between N
& V.
N is connected to
Neutral of generator & V to V Phase of generator.
, N is connected to U Phase
& V to V Phase of generator. Refer to Figure
3 & 4.
Current compensation input.
Current Transformer(CT) secondary current = 1A,
0.8 PF.
V
V
V
V
V
V
V
V
220
380
220
380
220
380
External Voltage Adjustment.
If an external voltage adjust control is being used,
connect a 100 K / 1 watt potentiometer to
terminals
and
as shown in Figure 3 & 4.
If not in use then let VR1 & VR2 is left open.
: Analog Voltage Input.
Fully isolated analog voltage from PF controller or
any other type of Digital (PLC) controller can be
injected into AVR for variation of generator output
voltage. Analog voltage range is ± 5VDC maximum
and can be connected to A+ & A- terminals for
at least 10 % variation in terminal voltage.
When 60Hz operation, AVR response
time needs to be reduced. For that turn ON Switch1
so that extra fixed response time is now added with
STAB POT setting such that no over or under shoot
of voltage occurs during loading-unloading of
generator at 60Hz.
: When 50Hz operation, no need to
decrease response time as STAB POT setting is
proper for optimum stability of generator with
minimum over-under shoot of Voltage during
loading - unloading of generator.
For 60 Hz operation of UFRO
For 50 Hz operation of UFRO
5. VR1 - VR2:
VR1
VR2
6. A+ & A-
7. DIP SWITCH:
a) SW1 - ON:
SW1 - OFF
b) SW2 - ON:
SW2 - OFF:
6. ADJUSTMENT
All trimmer build in back of the AVR board, except
the
and
Trimmer. The trimmers include
as shown in
Figure 2. For
Trimmer and
Trimmer refer
to Figure 1
The generator output can be altered by
adjustment of the
trimmer on the AVR board,
or by the external trimmer (100K ohm 1W) if fitted.
a) The terminals
and
must be left
unconnected if no hand trimmer is required.
O/L
TRIM
DROOP, UFRO, STAB and VOLT
O/L
TRIM
1. VOLT: Voltage Adjustment.
VOLT
Vset is factory set for 400 Vac , If Vset is
disturbed and set value is not known then
proceed as below :
VR1
VR2
.
Connect a voltmeter to generator output voltage
terminals.
d) Start the generator set and run on no load at
nominal frequency 50 - 53 Hz or 60 - 63 Hz.
e) If the red Led is illuminated, refer to the under
frequency roll off adjustment.
f) Carefully turn volt trimmer clockwise until rated
voltage is reached.
Stability Pot is factory set for optimum performance
& is advisable not to disturb. But if required then
with the generator in ON Condition, rotate STAB
POT clockwise direction till voltage start oscillating
fast.
b) Before starting the generator, please turn the
trimmer on the AVR board fully anti-
clockwise.
c)
VOLT
2. STAB: Stability Adjustment.
Page 3 of 7
Updated on 02 Feb2015