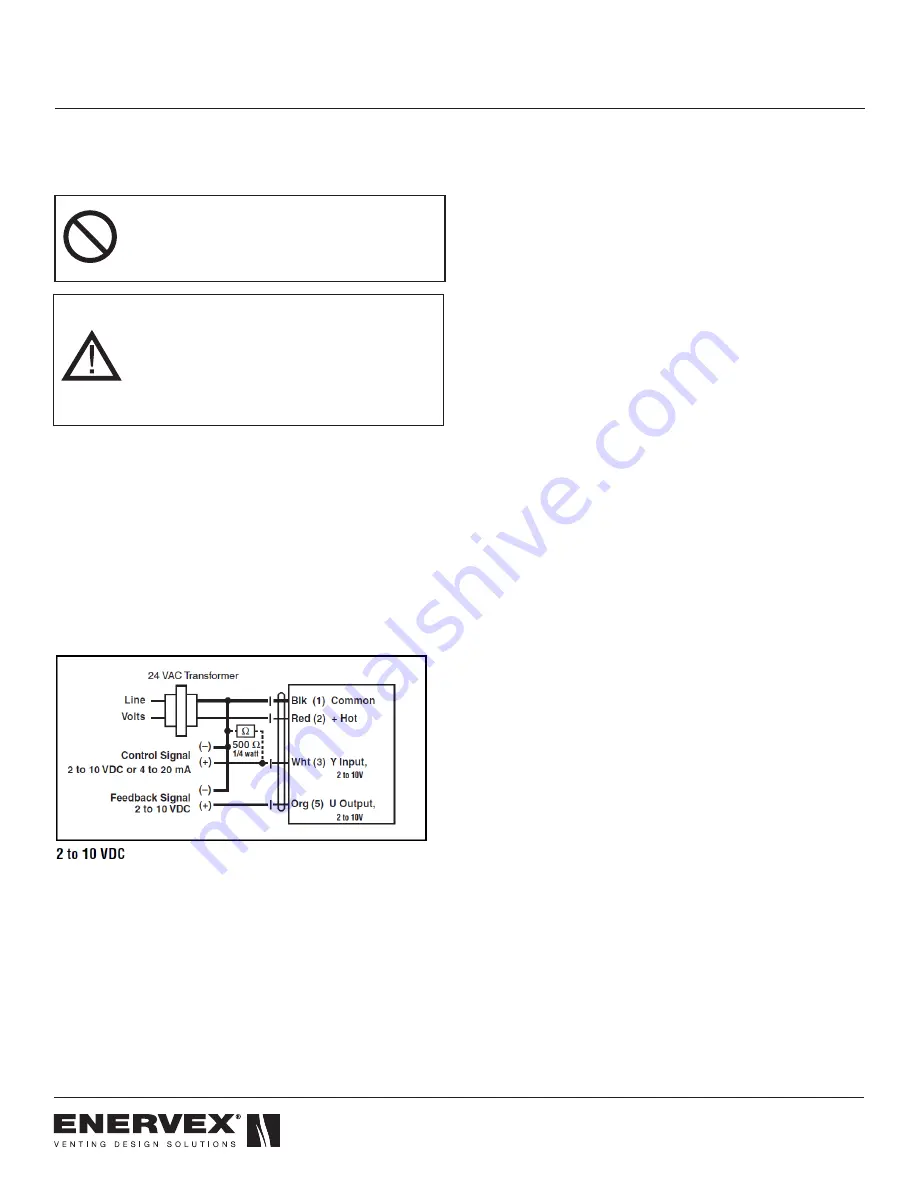
14
010.4150.0720 08.21
6. ELECTRICAL INSTALLATION
6.1 GENERAL
All wiring must be in compliance with the local codes, or, in
their absence, the National Electric Code, NFPA70. All wiring
should be appropriate Class 1 wiring as follows: installed in
rigid metal conduit, intermediate metal conduit, rigid non-
metallic conduit, electrical metallic tubing, ir be otherwise
suitably protected from physical damage.
6.2 MODULATING BYPASS DAMPER
The only electrical part of the VHX-DR is the actuator
serving the Modulating Bypass Damper. The actuator can
be controlled by a 0-10VDC signal either from an ENERVEX
HRC80 or from a third-party supplied controller.
DANGER
Turn off electrical power before servicing.
Contact with live electric components can
cause shock or death.
NOTICE
If any of the original wire supplied with the
system must be replaced, use similar wire
of the same temperature rating. Otherwise,
insulation may melt or degrade, exposing bare
wire.