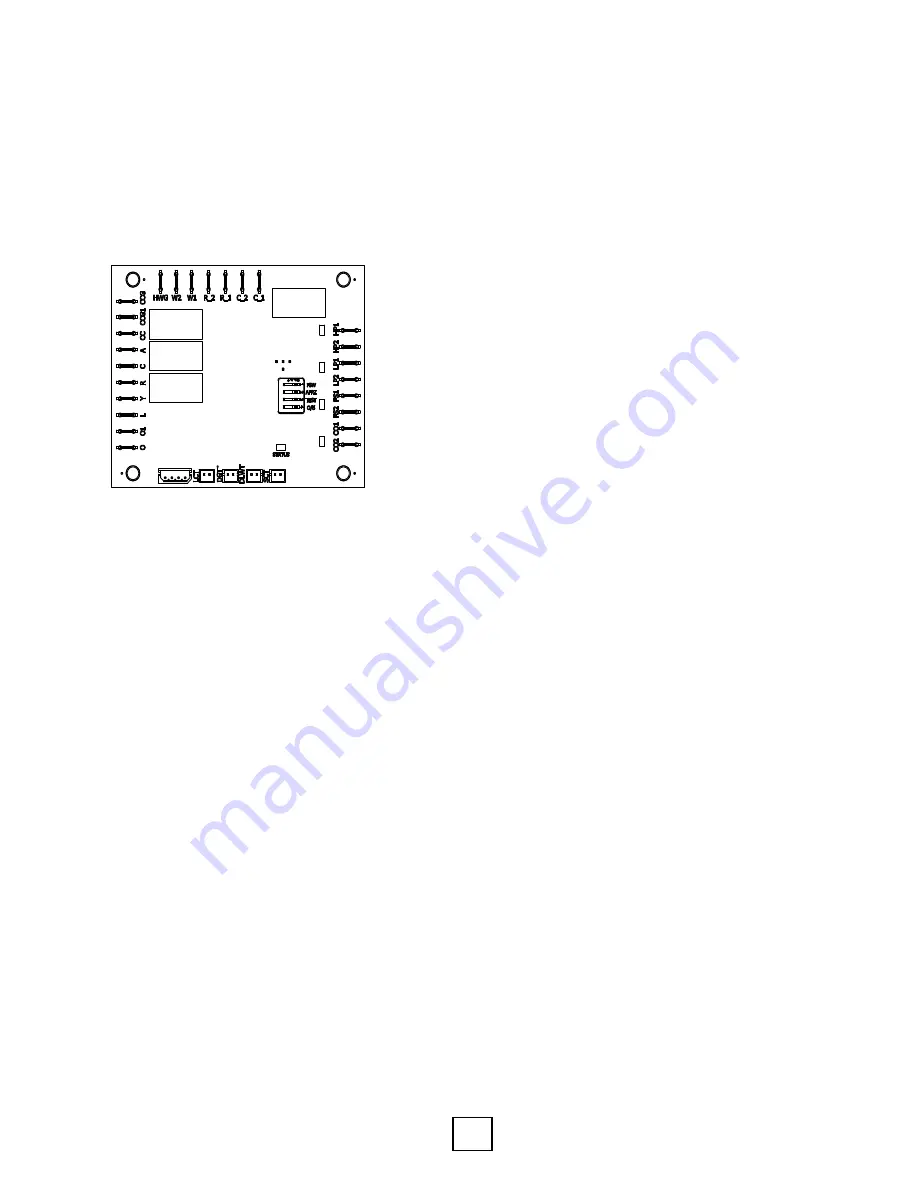
13
IOM, WD Models
Enertech Global
Features
Enertech Global geothermal heat pump controls leverage a
modular approach for controlling heat pump operation. The
control system uses a combination of printed circuit boards,
depending upon the features equipped in a particular unit.
This approach simplifies installation and troubleshooting, and
eliminates features that are not applicable for some units.
Section 7: Controls
Lockout Board Layout
20D239−01NN
REVISION HISTORY
REV
DESCRIPTION
ECN
DATE
APPROVED
A
INITIAL RELEASE FOR UPDATED CONTROLS
SECTION IN IOM
4−29−16
KW
GREEN
HIGH PRESSURE
ORANGE
LOW PRESSURE
RED
FLOW SWITCH
YELLOW
CONDENSATE
OVERFLOW
GREEN
STATUS
ICM LOCKOUT BOARD
The Lockout Board controls the inputs to the unit as well as
outputs for current mode, faults, and diagnostics. A status
LED and different combination of four LEDs for each fault are
provided for diagnostics. The Lockout Board Terminal (L) puts
out the number of corresponding 24VAC pulses to indicate the
Lockout condition on the Thermostat (if equipped and wired).
Startup/Random Start
The unit will not operate until all the inputs and safety controls
are checked for normal conditions. A ten to twenty second
random start delay is added at power up and whenever a Y1
call is received. This avoids multiple units from being energized
at the same time after events such as power loss or brown
outs.
Short Cycle Protection
A built-in five minute anti-short cycle (ASC) timer provides
short cycle protection ensuring that the compressor isn’t
damaged due to rapid cycling.
Test Mode
The Lockout Board allows the technician to shorten timing
delays for faster diagnostics by placing the DIP switch ‘TEST’
switch in the ON position (See ‘Settings’ section). It should be
moved back to OFF for normal operation after testing. The
status LED will not be illuminated during the TEST mode.
4-Way Valve Control
When 24Vac is applied to the O terminal on the field wiring
block, the controller energizes its O1 output to provide 24Vac
power to the reversing valve to switch the refrigerant circuit to
the cooling mode.
Changeover from heating to cooling can be achieved in two
ways:
1. A manual toggle switch to select the heating or the
cooling hydronic control (Aquastat), or.
2. A cooling thermostat which powers the coil of a single
pole/double throw relay to select the heating hydronic
control (normally closed contact) or the cooling hydronic
control (normally open contact).
Compressor Control
When 24Vac is applied to the Y terminal on the controller
wiring block, the controller decides, based on lockout and
anti-short-cycle periods, when to turn on the compressor
contactor. The CC output of the controller energizes the
contactor(s) until 24Vac is removed from the Y terminal or a
fault is detected.
Safety
The lockout board receives feedback signals for high pressure,
low pressure, load heat exchanger temperature, source
heat exchanger temperature, condensate overflow, and
hot gas temperature faults. Upon a continuous 10-second
measurement of all faults (except the high pressure) the
compressor operation is suspended. The high pressure fault is
tripped instantly. The different combination of LED(s) indicate
each temporary fault. Once the unit is locked out (see fault
retry below), the Lockout Board outputs a number of 24VAC
pulses equal to the numbered fault code. In lock out the unit
will not start until a soft or hard reset.
Low Pressure (LP)
If the low pressure switch is open continuously for 10 seconds,
the compressor operation will be interrupted and the control
will go into fault retry mode. At startup, the low pressure
switch monitoring is suspended for 30 seconds to avoid
nuisance faults. However, if the low pressure switch is open
before startup then the unit will not start upon receiving an Y1
call and will lock out instead.
Note: Flow switches are not equipped with this unit. A jumper
wire overrides this feature. A flow switch kit is available to add
on: Part Number: 28K053-05NN.
Flow Switch (FS)
Flow switches ensure the source and load water maintain
the minimum required flow rate. This ensures that pumps
are working and water connections remain intact. If the flow
switch is open continuously for 10 seconds, the compressor
operation will be interrupted with a FS fault. At startup, the
flow switch monitoring is suspended for 30 seconds to avoid
nuisance faults. The flow switches will also trip when the
water begins to freeze, providing additional protection.