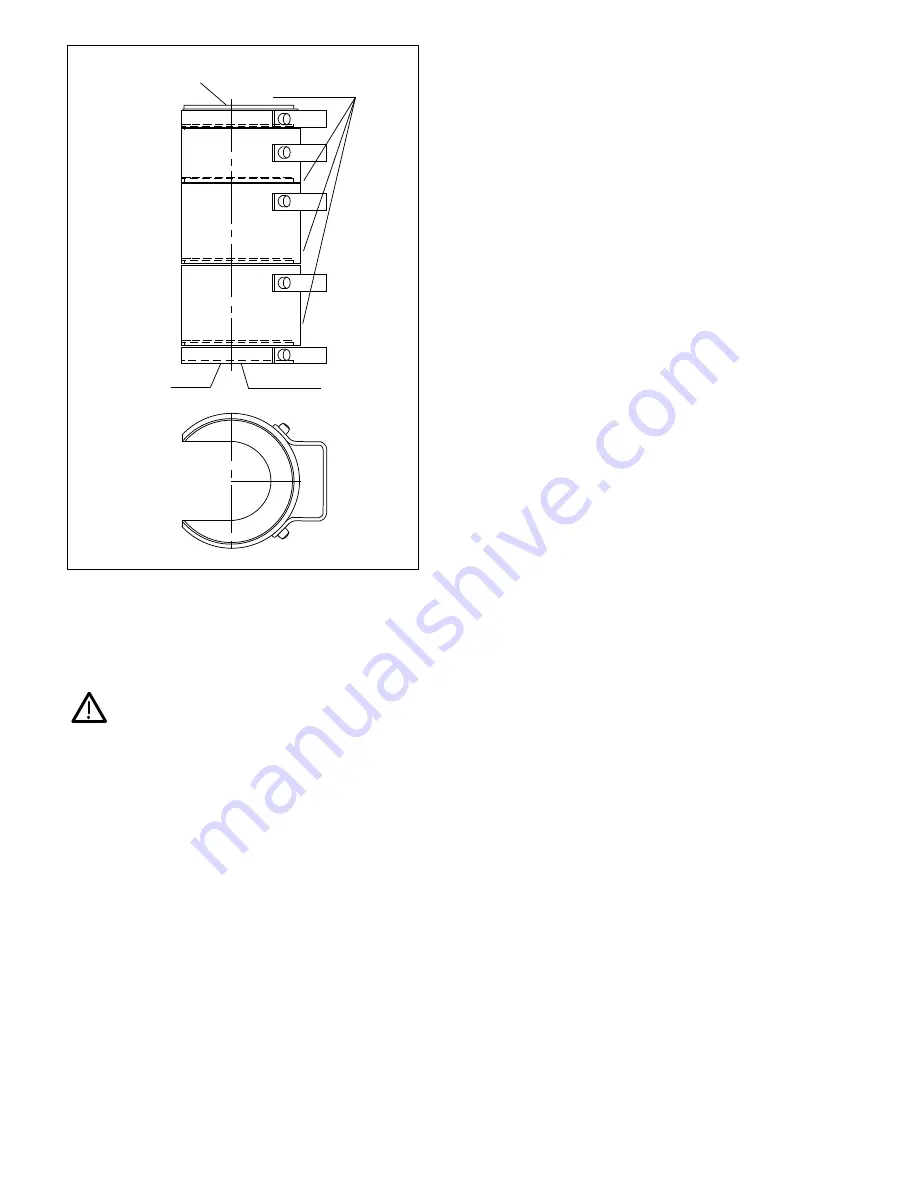
4
Steel Ring
Recess of Ring
on Cylinder
Steel Ring
Aluminum Rings
Figure 6, U-Ring Stacking
5.4 Jacking Safely
You must know the weight of what you intend to lift and choose
a jack with at least 20% more capacity.
WARNING: Never crawl or place any part of your
body under any load at any time. Insert lock rings as
you lift. Jacks are meant for lifting only and should not
be used to support the load for any period of time.
You should obtain and be familiar with the American National
Standards Institute rules that apply to hydraulic rams and jacks
(ASME ANSI B30.1).
5.5 After Completing the Job
Fully retract the cylinder, close air valve (#4) to shut off motor, shift
the hydraulic controls several times to release system pressure.
Store the unit in a clean, dry area.
6.0 MAINTENANCE
6.1 Periodic Maintenance
Change the hydraulic oil and clean the oil filter screen and magnet
(located in the reservoir) twice a year. Use Enerpac HF hydraulic
oil (model number HF-102 - 5 gallon container). Change the oil
more frequently when used in extremely dusty areas or when the
oil has been overheated. Using oil other than Enerpac brand may
void the pump warranty.
6.2 Maintain Oil Level
Check hydraulic oil level every 30 hours of operation. Add
Enerpac HF hydraulic oil (model number HF-101 - 1 gallon
container) when necessary. Oil level should be no more than 1”
from top of reservoir plate – with cylinders retracted and motor
off.
Change oil at least twice a year. The following conditions require
more frequent oil changes:
•
Rigorous duty, where oil temperature may reach 150° F.
•
High humidity environment and extreme changes in
temperature that can result in condensation inside the
reservoir.
•
Dirty or dusty environments that may contaminate the oil.
•
Frequent connection and disconnection of hydraulic hoses
and components.
6.3 Clean Oil Filter Screen Once a Year
Loosen and remove reservoir plate bolts. Lift pump unit off the
reservoir, being careful not to damage the gasket. Unscrew
screen from bottom of pump unit and clean with nonflammable
solvent. Blow dry and reassemble. Keep areas around pump
unobstructed to provide good air flow around the motor and
pump. Keep the motor and pump as clean as possible.
6.4 Flush the Pump
If you suspect your pump has been contaminated or discover
sludge or other deposits on internal components, you should
thoroughly flush the pump. Remove the old oil from the reservoir,
then thoroughly clean the reservoir and refill with a clean,
nonflammable flushing oil. Reassemble the pump and motor to
the reservoir.
Now run the pump in no load condition for 1 or 2 minutes
maximum. Unplug the pump and remove the motor and pump
assembly again. Now drain the flushing oil and re-clean the inside
of the reservoir. (Make sure flushing fluid is also drained from
pump assembly). Refill the reservoir with Enerpac HF hydraulic
oil and reassemble the pump.
6.5 Air Motor and Filter Lubricator
The air motor is a precision built rotary motor. The top clearance
(between rotor and bore) is .0015". The total end clearance
(between the sides of the rotor and the end plates is .002". The
vanes take up their own wear and will last 5,000-12,000 hours,
depending upon speed, method of oiling, operating pressure,
and lend itself to operating pressure above 100 psi (6.89 bar-
metric). Allowing excess moisture or foreign particles from the air
line to enter the motor will void the Enerpac warranty.
A moisture trap and filter has been installed in the air line ahead
of motor. For efficiency of output and control of speed, use air
line of not less then ¾ in pipe size. When coupling or connecting
the motor to a drive member, avoid any end or side thrust on the
output shaft and especially DO NOT HAMMER ON SHAFT.
The starting torque is less than the running torque and could vary
depending on the position at which the vanes stop in relation to
the air intake port. The speed and torque can be regulated by
using a pressure regulator or a simple shut-off valve. Lubrication
is necessary for the shaft seal, and rust prevention. Each air
powered jack is equipped with an automatic air line oiler set
to feed 1-3 drops per minute. Use Kilfrost 400 pneumatic tool
lubricant or equivalent. Excessive moisture in the line can cause
rust formation in the motor and might also cause ice to form in
muffler due to expansion of air through the motor.