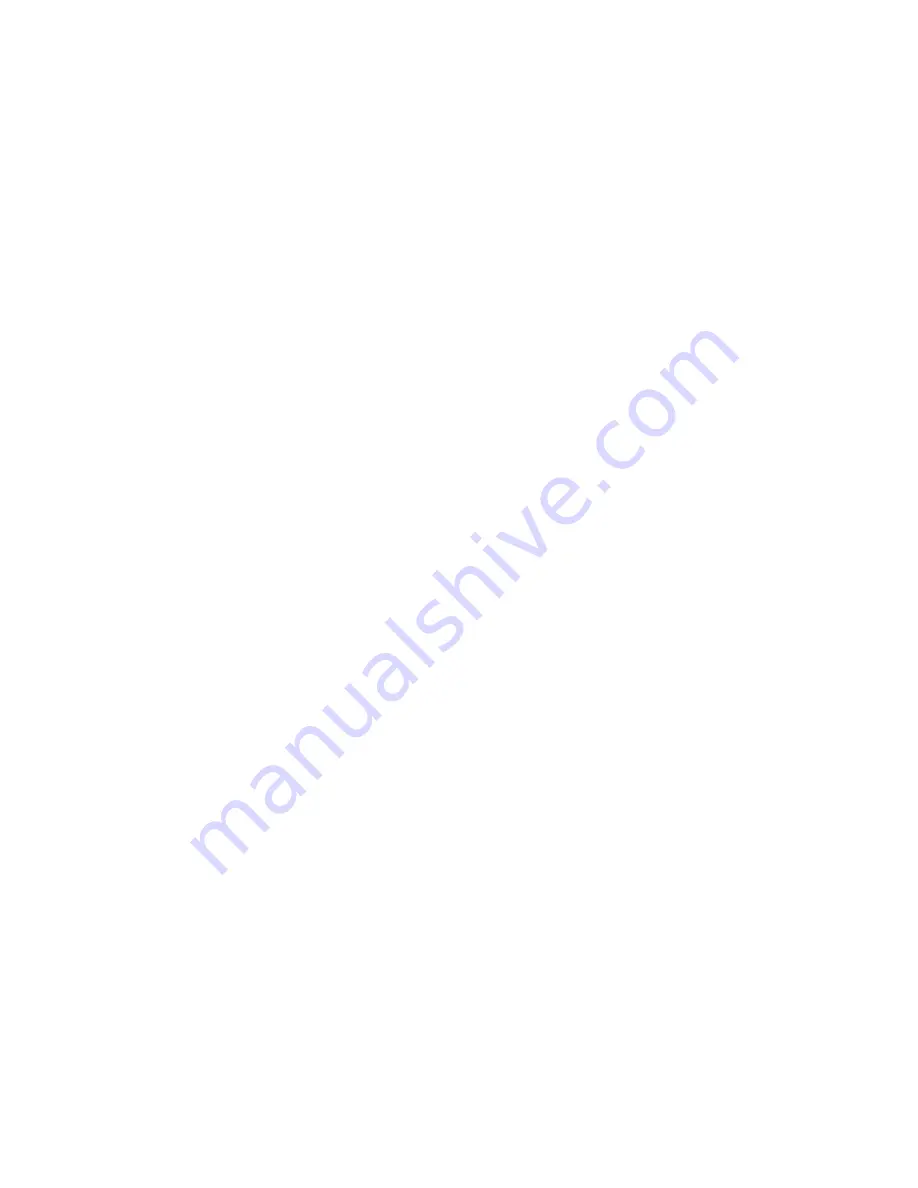
Reassembly: When assembling, use new
parts supplied in repair kit.
1.
Clean valve block and inspect all components.
Check for worn or damaged ball seats, broken or
weak springs. Inspect relief ball seats in valve
block.
2.
Carefully reseat small balls in reliefs, and replace
guides, springs, and adjusting screws. Use care
when turning adjusting screws so as not to distort
or displace springs. Pilot relief spring can be
forced into cross hole by bottoming screw. Do not
install gaskets (item 30) or screws (item 25) at this
time as adjustments to reliefs will be made during
testing of the valve.
3.
Assemble advance and retract piston sections by
installing gaskets (item 29) and lower seats (item
40). Torque lower seats to 25-30 ft-lbs. [33,9-40,7
Nm]. Install balls (item 24), spring and spacer
assemblies (item 54), balls (item 24), gaskets
(item 43) and upper seats (item 39). Torque upper
seats to 37 ft-lbs. [50,2 Nm]. NOTE: If new seats
are used, they must be seated by placing the ball
on the seat and pressing to 200 PSI [13,8 Bar] on
a 10 ton press.
A. Attach couplers to both ports. Connect each
port to hand pump and 15,000 PSI [1035,0 Bar]
gauge. Adjust each high pressure relief to
11,500-12,000 PSI [793,5-828,0 Bar]. Valve
should hold pressure at 10,000 PSI [700 Bar]
without leakage. Both seats in directional
circuits will be checked in this operation.
4.
Install new O-Rings and back-up washers on all
three pistons.
5.
Install springs (item 26) and piston assemblies
(item 51) into advance and retract sections of
valve body. Install cover seals (item 46) between
piston and cover plate.
6.
Assemble pilot piston section by installing spring
(item 37), spacer (item 55), ball (item 23), gasket
(item 43) and seat (item 38). Torque seat to 37 ft-
lbs. [50.2 Nm]. Install pilot piston assembly (item
48), spring (item 27) and spacer (item 31).
7.
Use seven cap screws (item 41) to bolt cover (item
42) and gasket (item 57). Insert adjusting screw
(item 45) and locknut (item 32). Do not install
acorn nut (item 35) at this time as adjustments will
be made during testing.
8.
Install solenoid assembly (see Figure 3) using four
cap screws and cover to valve body.
9.
Valve is now ready to be adjusted and tested.
Adjustments
1.
Mount valve on a remote block and connect to a
700 cu. in./min. [11,473 cu.cm/min.] output test
pump. Insert 2,000 PSI [138,0 Bar] gauge in
1
⁄
16
"
NPT port on block nearest cover plate (may be on
either side of block).
2.
Connect pushbutton station to the valve.
3.
With adjusting screw turned in, adjust pilot relief
setting from port end of block to 1,150-1,200 PSI
[79,3-82,8 Bar].
4.
Adjust pilot setting to 850-900 PSI [58,7-62,1 Bar].
(Adjustment screw is located under acorn nut.)
5.
Connect the ADV port to advance port on a double
acting cylinder and a 15,000 PSI [1035,0 Bar]
gauge.
6.
Connect the RET port to retract port on a double
acting cylinder and a 15,000 PSI [1035,0 Bar]
gauge.
7.
Run the cylinder back and forth under no pressure
to eliminate air.
8.
Valve should build to maximum pressure in both
advance and retract directions.
9.
Valve should hold pressure in both advance and
retract directions. At 10,000 PSI [700 Bar] there
should be less than a 300 PSI [20,7 Bar] drop in
15 seconds. When the valve is in hold, there
should be no cylinder creep.
10. Remove remote block and reassemble to original
block and onto pump.
6