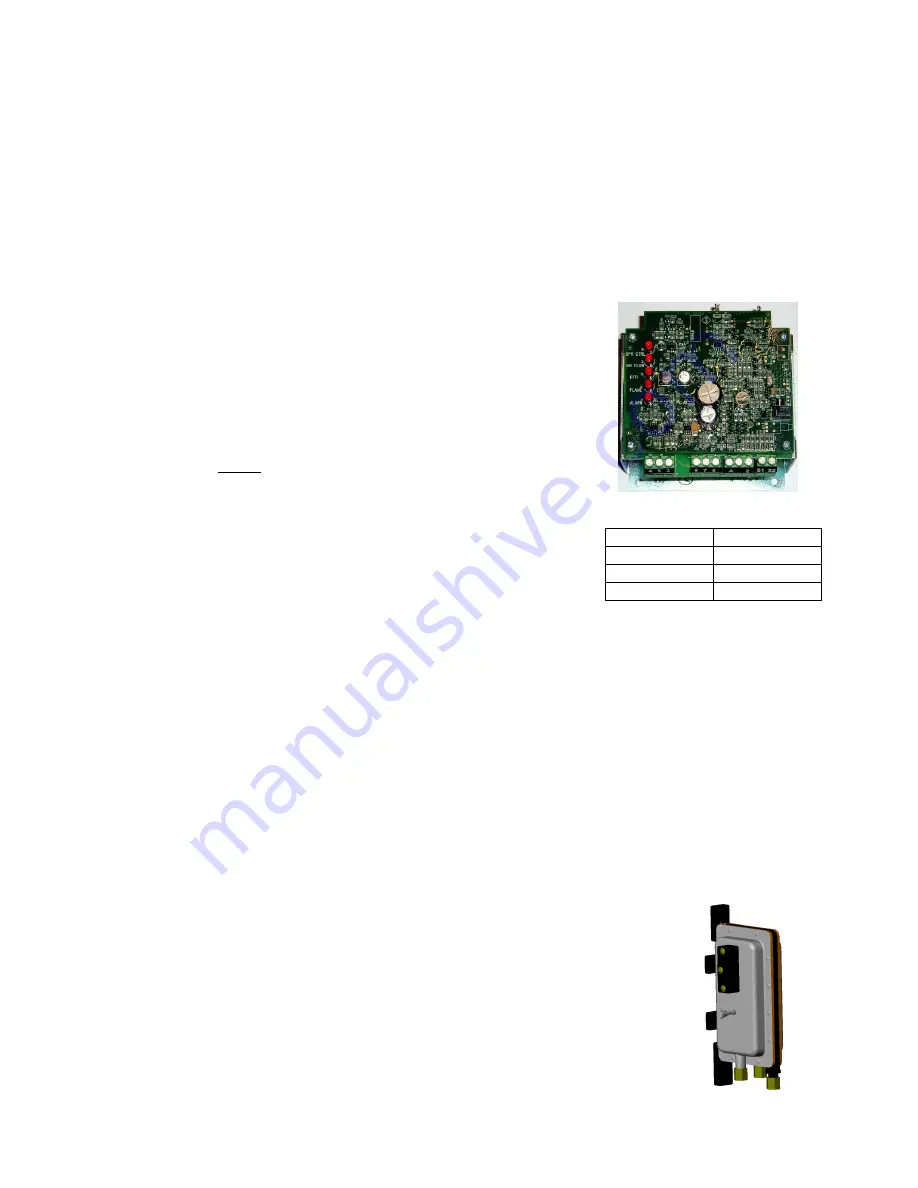
16
Flame Safety Controller
Air Flow Switch
DC Flame Signal
DC Voltage
Flame Status
0 to 5 VDC
No Flame
6 to 11 VDC
Weak Flame
12 to 18 VDC Strong Flame
Sequence of Operation
The direct-fired heater is most easily understood when broken down into smaller individual systems.
There are two main systems, a make-up air fan and a heater. The make-up air fan consists of a blower
and motor. The heater may be further broken down into two control systems, the Flame Safety Control
(FSC) and the Modulating Gas System (MGS). The burner mixes air with the gas (Natural or LP) which
heats the air.
Flame Safety Control
The first system to understand is the
Flame Safety
Control
. The FSC
is there
only
to monitor the flame, NOT to control temperature. The
FSC uses a flame rectification sensor mounted on the pilot assembly
to detect the presence of flame in the burner. Flame strength and
presence can be measured at the FSC by reading the rectified flame
signal. This is done by using a DC voltage meter attached to the test
jacks on the top of the control. Flame is present when the DC voltage
reads between
6 and 18 VDC
. Ideal flame intensity produces a signal
of
12 VDC
or greater. The FSC is also wired into an airflow switch,
which tells it whether there is proper airflow through the unit (not
just
any airflow, but
proper
airflow). Proper airflow occurs when there is a
.15 in. w.c. to .80 in. w.c. differential pressure drop across the
burner
. When the airflow through the heater produces a pressure
drop in this range, the FSC indicates so by illuminating the AIRFLOW
LED. The FSC controls the opening of the redundant solenoid gas
valves and the operation of the spark igniter to initiate a pilot flame
upon start-up.
The
OPR CTRL
LED indicates that there is power to the FSC. Next,
the
AIRFLOW
LED will come on if there is proper airflow through the
unit. Third, the unit will pause to purge any gasses or combustible vapors before attempting flame
ignition. Then, there is a Pilot Trial For Ignition (PTFI) and the
PTFI
LED comes on. During PTFI, the FSC
opens the pilot gas valve and allows gas to flow to the pilot assembly. At the same moment, the spark
igniter is started, causing the spark to ignite the pilot gas. When the flamerod sensor detects the flame, it
turns on the
FLAME
LED, turns off the PTFI LED, and powers the modulating gas system. This is the
normal operating mode. The FSC continues to monitor the flame and airflow. Once this occurs, the unit is
in a main flame cycle and thus powers the main gas valve and the modulating gas system. This is the
normal operating mode. The FSC continues to monitor the flame and airflow. The last LED on the FSC is
the
ALARM
LED. This will turn on when the FSC determines an unsafe condition has occurred, and will
not allow the unit to recycle for heat until it has been properly reset. Anytime the FSC has gone into
“Alarm” mode, the problem must be diagnosed and corrected to avoid future lockouts after resetting. To
begin troubleshooting, or to reset the FSC, shut down power to the heater and restart the heater. This
will clear the alarm from the flame safety.
Air Flow Switch
There are both high and low
airflow switches
contained within one housing
measuring the pressure drop across the burner. This is to insure that there is
proper airflow
(.15 in. w.c. to .80 in. w.c.
) across the burner and proper
combustion at all times. Both switches are wired in series and have single pole
double throw (one common contact, one normally open contact, and one normally
closed contact) switches that are ‘switched’ by air pressure. There are two airflow
tubes in the heater, located near the burner and profile plate assembly (profile
plates surround the burner and control air into the burner section). In the case of
clogged filters, blocked intake, excessive duct static pressure, or a broken belt, the
correct burner differential pressure may not be achieved, not allowing the low