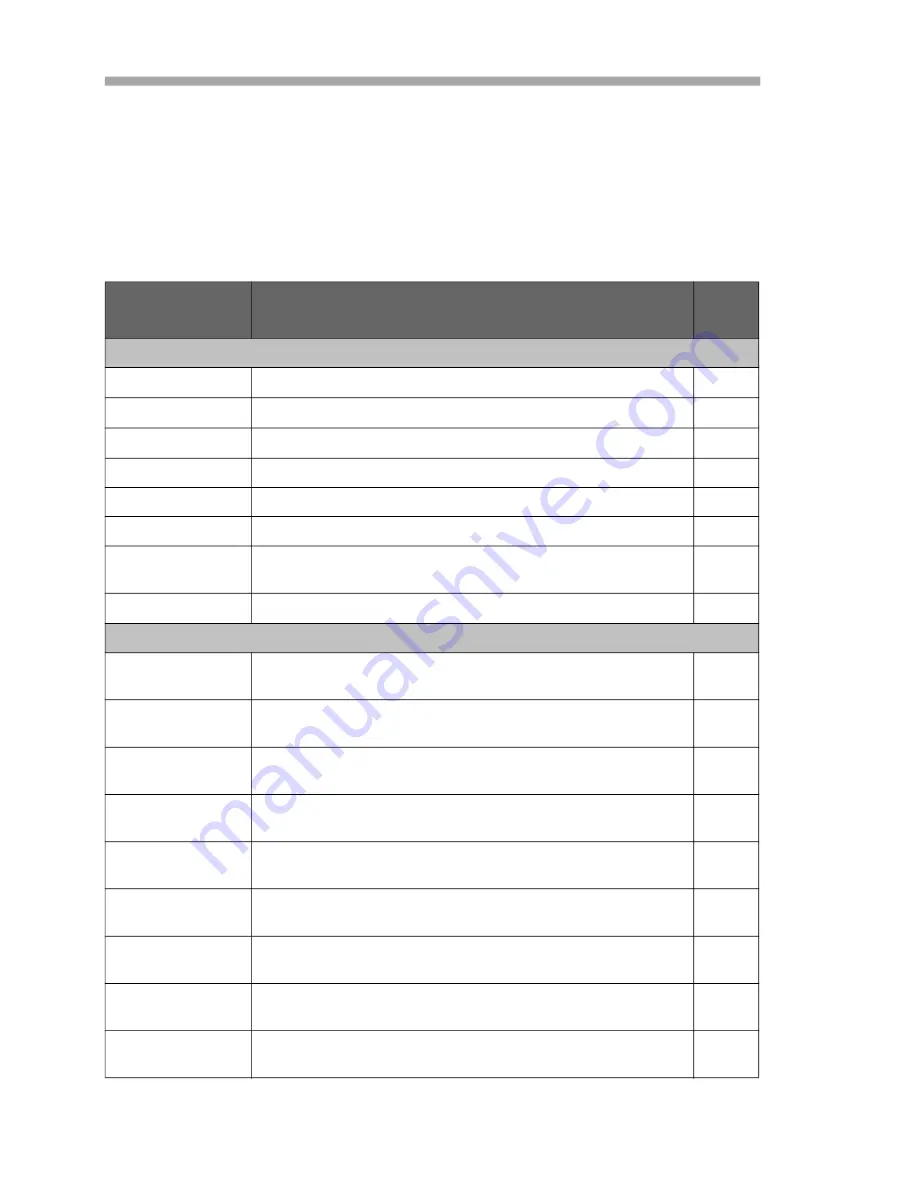
OXY5500 Optical Oxygen Analyzer
BA02195C
A
–
6
Hauser
Spare Parts
Below is a list of spare parts for the OXY5500 Optical Oxygen Analyzer with
recommended quantities for 2 years of operation. Not all parts listed are
included on every analyzer. When ordering, please specify the system serial
number to ensure that the correct parts are identified.
Table A–2
Replacement parts for OXY5500 analyzer
Part Number
Description
2 YR
QTY
Electronics Assembly Components
EX3700000001
Window, Enclosure
1
1. Consult with Technical Support (refer to page B–19) before attempting replacement.
-
EX1600000001
Window Gasket, Enclosure
1
-
2400002173
OXY5500 Display
1
-
EX1100000002
Replacement Kit, Transmitter, OXY5500
-
EX4000000001
Power Supply, Module, AC100-240V to DC24V 1.3A
1
EX4000000003
Power Supply, DC/DC Conv., 15W, 24V, DIN
1
4300002034
Cartridge Fuse, 216 Series, 5 x 20mm, Fast Act 800 mA,
250V
1
EX3100000004
Communication Board
1
-
Optical Fiber Probes and Installation Accessories
3100002235
Optical Fiber Assembly, OP-9 Sensor Probe, 1000ppm,
0.7 m, SMA
1
3100002242
Optical Fiber Assembly, OP-9 Sensor Probe, 1000ppm,
2.5 m, SMA
1
3100002243
Optical Fiber Assembly, OP-9 Sensor Probe, 1000ppm,
5.0 m, SMA
1
3100002239
Optical Fiber Assembly, OP-6 Sensor Probe, 5%, 0.7 m,
SMA
1
3100002240
Optical Fiber Assembly, OP-6 Sensor Probe, 5%, 2.5 m,
SMA
1
3100002241
Optical Fiber Assembly, OP-6 Sensor Probe, 5%, 5.0 m,
SMA
1
3100002236
Optical Fiber Assembly, OP-3 Sensor Probe, 50%,
0.7 m, SMA
1
3100002237
Optical Fiber Assembly, OP-3 Sensor Probe, 50%,
2.5 m, SMA
1
3100002238
Optical Fiber Assembly, OP-3 Sensor Probe, 50%,
5.0 m, SMA
1
Summary of Contents for SpectraSensors OXY5500
Page 145: ......