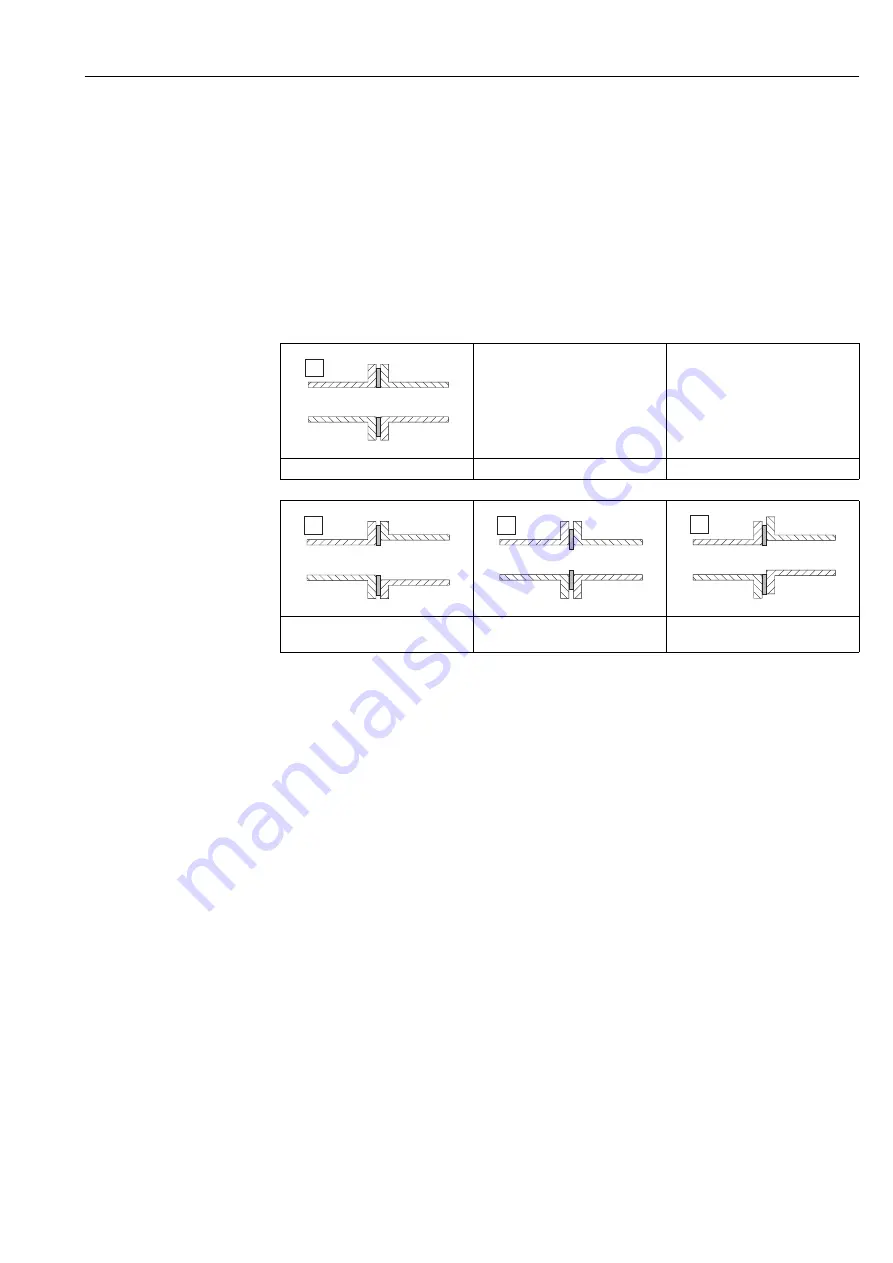
Proline t-mass 65 PROFIBUS DP/PA
Installation
Hauser
13
3.2.3
Pipework requirements
Good engineering practice should be followed at all times:
• Correct preparation, welding and finishing techniques
• Correctly sized gaskets
• Correctly aligned flanges and gaskets
• Connecting pipe work should match the internal diameter of the flowmeter.
Maximum pipe diameter mismatch should not exceed:
– 1 mm (0.04 inch) for diameters < DN 200 (8")
– 3 mm (0.12 inch) for diameters
DN 200 (8")
For further information please refer to ISO 14511.
"
Caution!
New installations should be free of metallic and abrasive particles to prevent damage to the sensing
elements on start-up.
a0005103
Correctly aligned flanges and gaskets
a0005104
a0005105
a0005106
Pipe diameter one is not equal pipe
diameter two
Incorrectly sized gaskets
Incorrectly aligned flanges and gaskets
Ã
✘
✘
✘