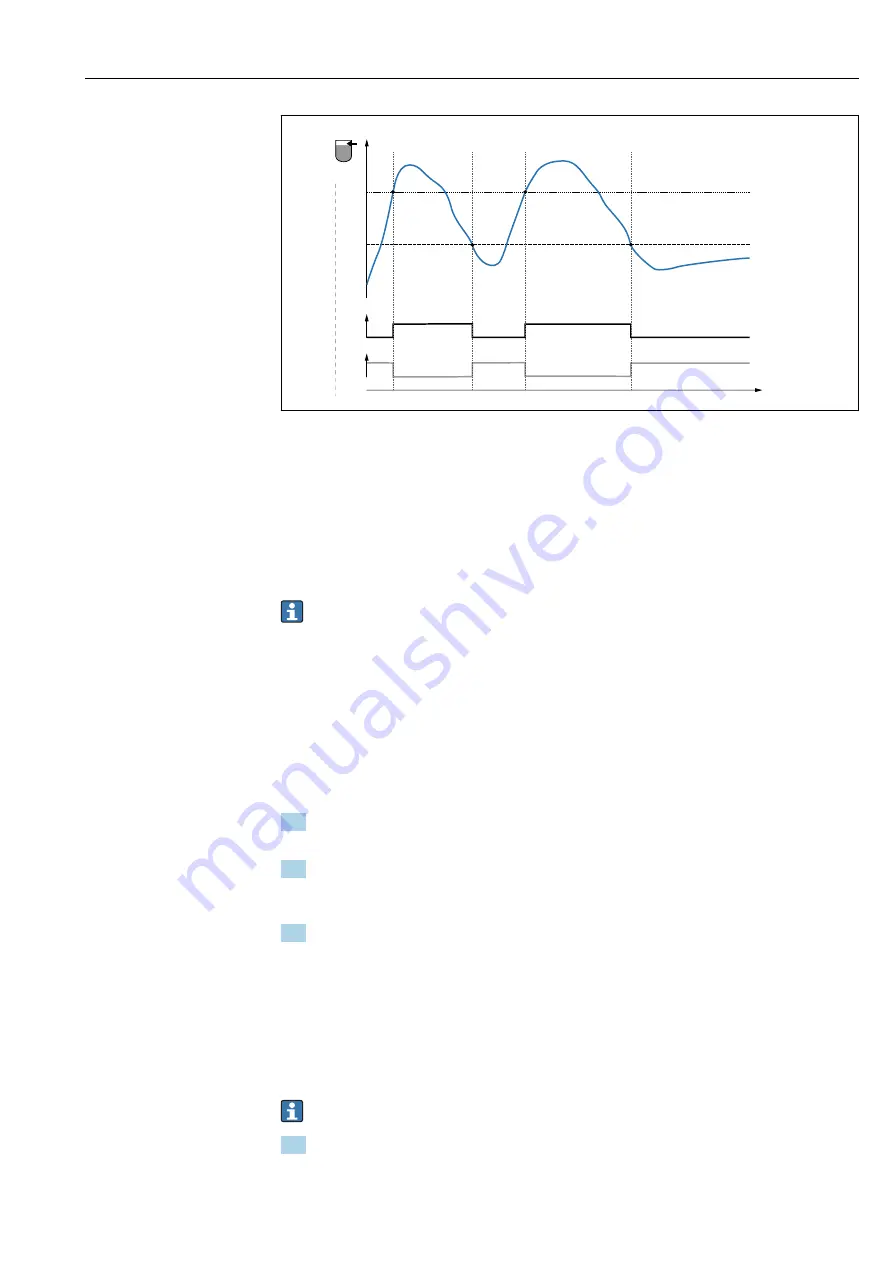
Liquipoint FTW23 IO-Link
Commissioning
Hauser
19
rP1
SP1
OU1
rP2
SP2
A
OU2
%
HNO (MIN)
HNC (MAX)
t
1
0
1
0
{
A0034529
3
Calibration (default)
0
0-signal, output open
1
1-signal, output closed
A
Hysteresis (difference between the value of the switch point "SP1" and the value of the switchback point "rP1")
%
Coverage of sensor
HNO Normally open contact (MIN)
HNC Normally closed contact (MAX)
SP1 Switch point 1 / SP2: Switch point 2
rP1 Switchback point 1 / rP2: Switchback point 2
Recommended assignment of switch outputs:
• MAX mode for overfill protection (HNC)
• MIN mode for dry running protection (HNO)
9.4
Window function, media detection/differentiation
Unlike the hysteresis, media are detected only if they are within the defined window.
Depending on the medium, a switch output can be used here.
9.4.1
Wet calibration
1. Navigate to the Application menu level
Setting:
Active switchpoints
=
User
2. Configure the behavior of the switch output.
Setting:
Output 1/2 (OU1/2)
=
Window normally open (FNO)
or
Window
normally closed (FNC)
3. Immerse the device in the medium to be detected.
Setting:
Calibrate coverage, Output 1/2 (OU1/2)
Setting:
Switch point value (Coverage), Output 1/2 (FH1/2)
and
Switchback
point value (Coverage), Output 1/2 (FL1/2)
The automatically generated switch limits can be adjusted accordingly.
9.4.2
Dry calibration
This calibration is suitable if the measured values of the medium are known.
For reliable detection of the medium, the process window must be sufficiently large.
1. Navigate to the Application menu level
Setting:
Active switchpoints
=
User
Summary of Contents for IO-Link Liquipoint FTW23
Page 39: ......