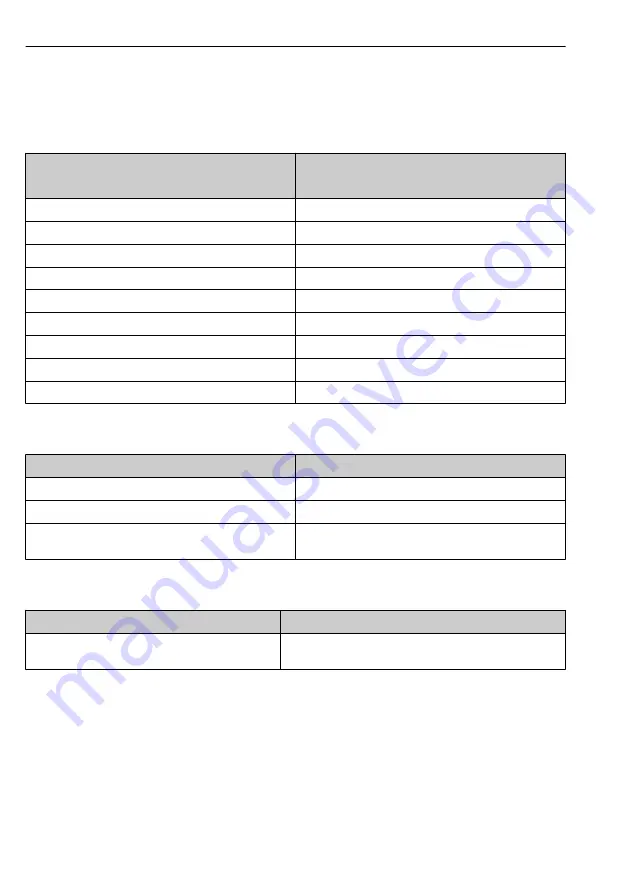
Permitted device types
Proline Promass 500
12
Hauser
3.4.2
Device-dependent additional documentation
Safety instructions
Safety instructions for electrical equipment for hazardous areas.
Contents
Documentation code
Measuring device
ATEX/IECEx Ex i
XA01473D
ATEX/IECEx Ex ec
XA01474D
cCSAus IS
XA01475D
cCSAus Ex i
XA01509D
cCSAus Ex nA
XA01510D
INMETRO Ex i
XA01476D
INMETRO Ex ec
XA01477D
NEPSI Ex i
XA01478D
NEPSI Ex nA
XA01479D
Special Documentation
Contents
Documentation code
Information on the Pressure Equipment Directive
SD01614D
Functional Safety Manual
SD01729D
Radio approvals for WLAN interface for A309/A310
display module
SD01793D
Installation Instructions
Contents
Comment
Installation instructions for spare part sets and
accessories
For an overview of the accessories available for order, see the
Operating Instructions for the device
4
Permitted device types
The details pertaining to functional safety in this manual relate to the device versions listed
below and are valid as of the specified software and hardware versions. Unless otherwise
specified, all subsequent versions can also be used for safety functions. A modification process
according to IEC 61508 is applied for any device modifications.
Summary of Contents for HART Proline Promass 500
Page 2: ......
Page 8: ...Certificate Proline Promass 500 8 Endress Hauser 2 Certificate A0033748 ...
Page 50: ......
Page 51: ......
Page 52: ...www addresses endress com ...