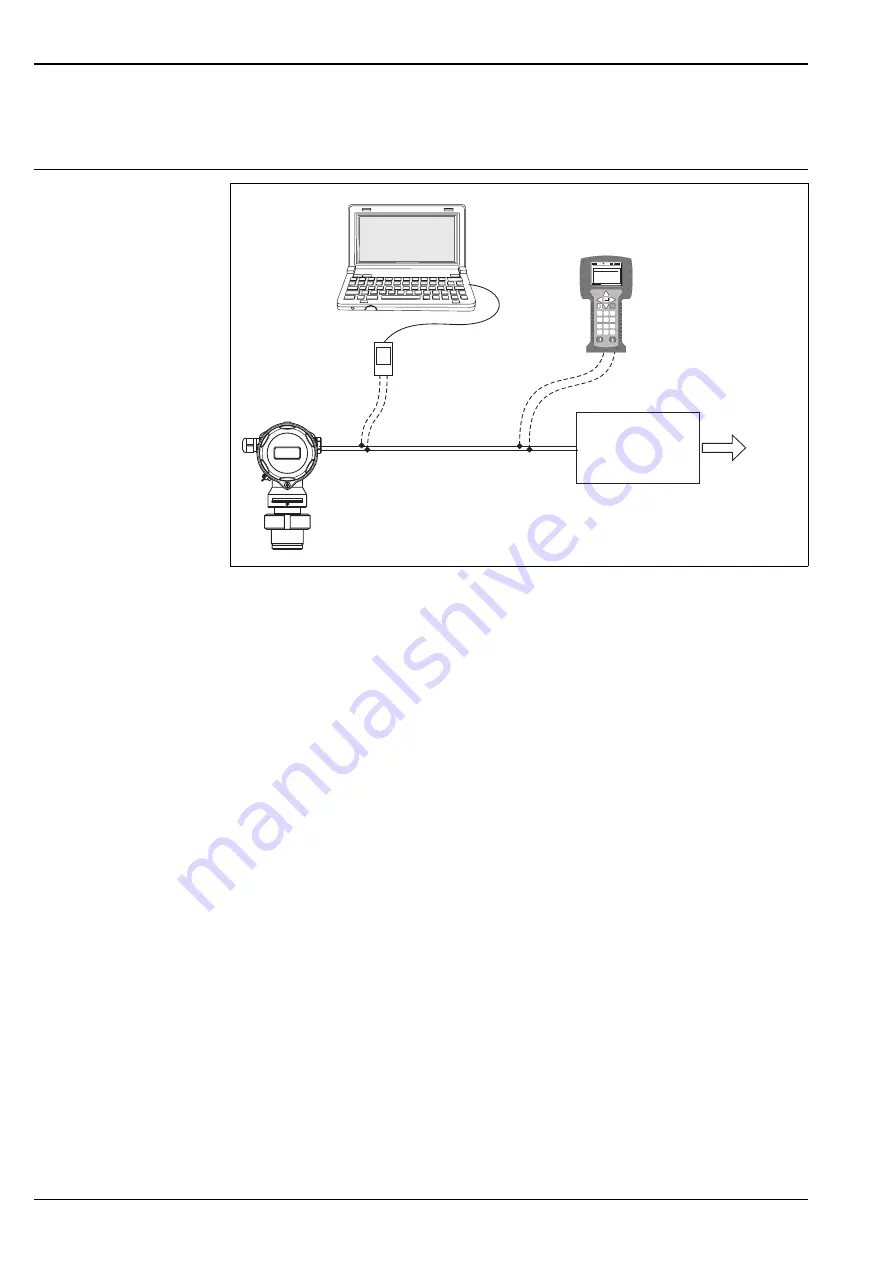
Deltapilot S
6
Hauser
Description of safety requirements
and boundary conditions
Safety function
SD213en02
Operating and configuration possibilities of the Deltapilot S
Safety-related signal
The safety-related signal of the Deltapilot S is the analog output signal 4...20 mA. All safety functions solely
refer to this output. In addition, the Deltapilot S communicates via HART and contains all HART characteristics
with additional diagnostics information.
Deltapilot S generates an analog signal (
≥
3.8...
≤
20.5 mA) that is proportional to the pressure. This signal is
sent to a logic unit located downstream, e.g. a programmable logic controller or a limit signal transmitter, and
monitored there to establish if:
– A specified value for the "Pressure" or
"Level" operating modes has been overshot or undershot ("Level Easy Pressure")
– A range to be monitored for the "Pressure" or "Level" operating modes has been violated ("Level Easy
Pressure")
– A fault has occurred (e.g. sensor error, sensor cable disconnection or short-circuit, supply voltage failure).
The following dangerous undetected failures can occur in the devices:
– An incorrect output signal which deviates from the real measured value by more than 1%, with the output
signal remaining within the 4...20 mA range.
– A settling time that is delayed by more than the specified settling time plus tolerance.
– Other deviations from specified safety-related properties.
For fault monitoring, the logic unit must be able to detect HI alarms (
≥
21 mA) and LO alarms (
≤
3.6 mA).
The transmitter output is not safety-oriented during the following activities:
– Changes to the configuration
– Multidrop
– Simulation
– Proof-test
While configuring the transmitter and performing maintenance work on Deltapilot S, alternative measures
must be taken to ensure the process safety.
4…20 mA
Commubox
FXA191/
FXA195
1
# % &
Copy
G H I
P Q R S
, ( ) ‘
A B C
Paste
Page
On
Page
Up
Delete
Bksp
Insert
J K L
T U V
_ < >
D E F
Hot Key
+ Hot Key
M N O
W X Y Z
+ * /
4
7
.
2
5
8
0
375
FIELD COMMUNICATOR
3
6
9
-
9
6
DELTABAR: * * * * * * * *
ONLINE
1 QUICK SETUP
2 OPERATING MENU
4 SV
0 °C
3 PV
352 mbar
HELP
SAVE
dsdmdm
df das.
asdas fa
asas la.
Logic unit
e.g. PLC,
limit signal generator
etc.
Computer with operating program
FieldCare as of version 2.02
Actuator
Deltapilot S
with display module (optional)
and local operation
Handheld terminal
375 Field Communicator