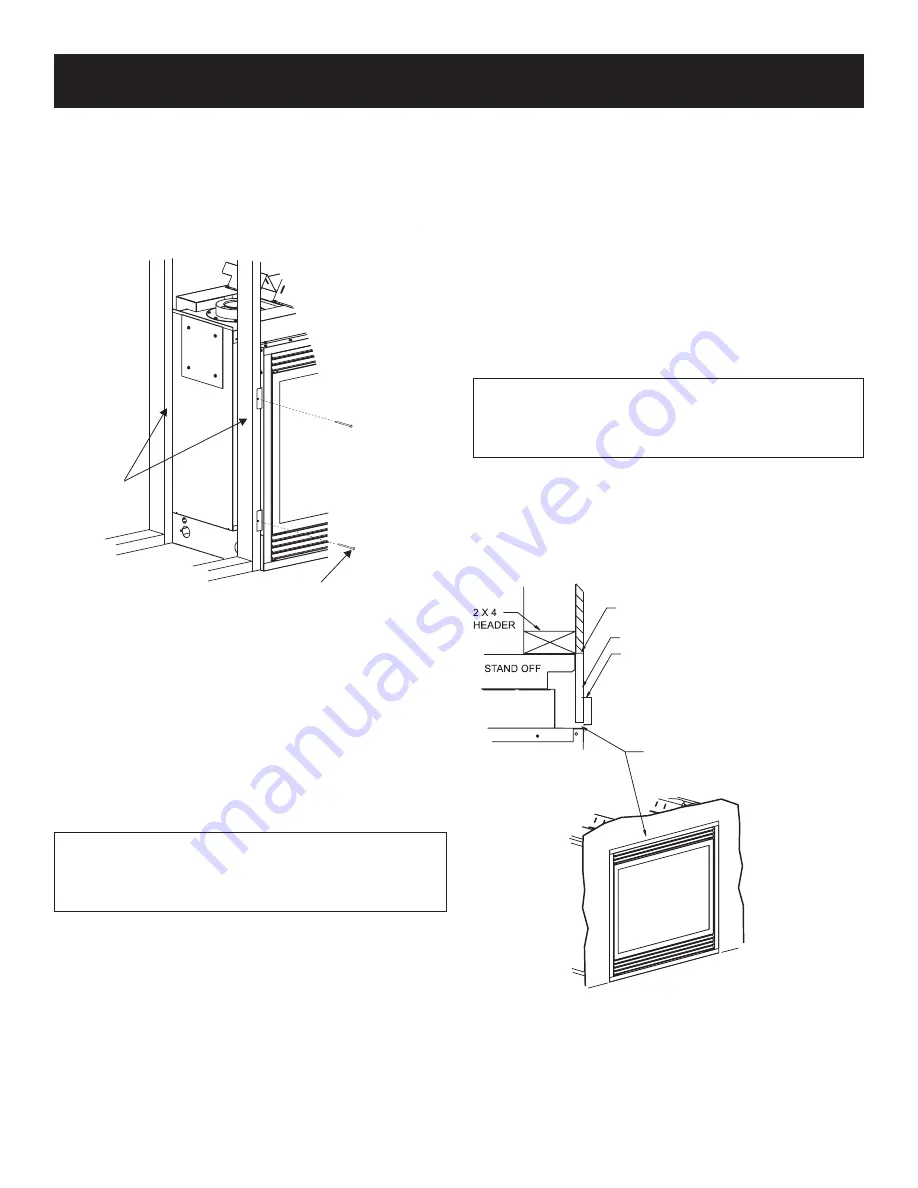
30786-7-0415
Page 17
instALLAtiOn
Flush Mount Mantel installation - see-through Models Only
(Figure 15)
The fireplace must extend 3/4" beyond finished wall surface when
using a flush mount mantel on see-through models. Refer to Figure
15 to locate nailing flanges on fireplace sides. Use eight (8) 1/2"
hex-head screws supplied in hardware package to attach nailing
flanges to fireplace sides.
NAIL OR OTHER
SUITABLE FASTENER
FRAMING
Figure 15
Framing (see Figure 12)
Fireplace framing can be built before or after the fireplace is set in
place. Framing should be positioned to accommodate wall covering
and fireplace facing material. The fireplace framing should be
constructed of 2 x 4 lumber or heavier. The framing headers may
rest on the fireplace standoffs.
cAUtiOn: MeAsUre FirepLAce DiMensiOns AnD veriFY
FrAMinG MethODs, AnD WALL cOverinG DetAiLs BeFOre
FrAMinG cOnstrUctiOn BeGins.
Framing dimension "A" (Figure 12) includes the clearance
for standoffs on fireplace. After installing fireplace into
framing, the finished non-combustible wall surface must
extend down to the top edge of the fireplace face.
Attention:
Add 3-3/4" to “A” dimensions when using a flush mantel
base.
Attention:
If a base or mantel is not used and the appliance is
installed directly on carpeting, tile or other combustible material
other than wood flooring, it shall be installed on a metal or wood
panel extending the full width and depth of the appliance. The
vertical dimension must be adjusted when a metal or wood panel
is placed beneath the appliance.
Finishing (Figures 16 and 17)
Finish the walls with the material of your choice. Figure 3 on page 10
shows the minimum vertical and corresponding maximum horizontal
dimensions of mantels or other combustible projections above the
top front edge of the fireplace.
Only non-combustible materials may be used to cover the black
fireplace front.
Warning: When finishing the fireplace never obstruct
or modify the air inlet/outlet louvers in any manner.
provide adequate clearances around air openings into the
combustion chamber.
caution:
If the joints between the finished wall and the fireplace
surround (top and sides) are sealed, a 300°F minimum sealant
material must be used. These joints are not required to be sealed.
Only non-combustible material (using 300°F minimum adhesive if
needed), can be applied as facing to the fireplace surround.
Flush Wall installation - see through Models
6 3/8” (162 mm) OF NON-COMBUSTIBLE MATERIAL
FINISHED WALL
FRONT TRIM OR NON-
COMBUSTIBLE MA TERIAL
(INSTALLA TION IS OPTIONAL)
JOINT BETWEEN FINISHED
WALL AND UNIT SEALED
WITH 300° F, 149° C SEALANT
MATERIAL (SEALANT IS OPTIONAL)
Figure 16