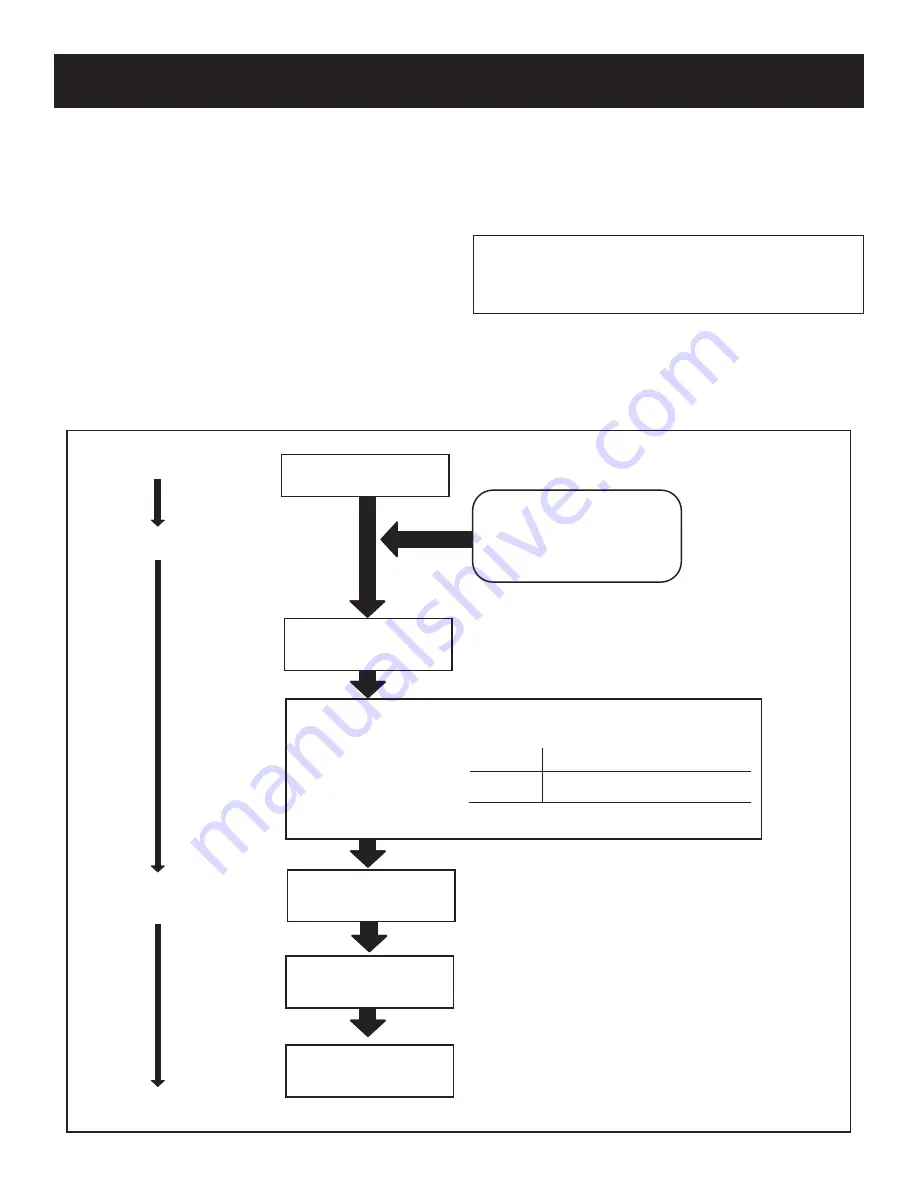
25663-0-0309
Page 49
Spark Generator Powered
First Valve (Pilot)
Operator Opens
Pilot burner lights.
Module senses flame current.
PILOT BURNER OPERATION
MODULE
S8600H
* Lockout timing is stamped on module.
RESPONSE
After 90 seconds*pilot valve
closes, spark stops.
OR
IF FLAME CURRENT SENSED
Spark generator off
Second valve operator
(Main) opens.
MAIN BURNER OPERATION
Module monitors pilot
flame current.
THERMOSTAT SATISFIED
Valves close. Pilot and
main burners are off.
START
STAGE 1
Trial for Ignition
STAGE 2
Main Burner
Operation
END
S8600H NORMAL OPERATING SEQUENCE
Pilot burner does not light
Thermostat, Wall Switch,
Remote, Etc. Calls for Heat
POWER INTERRUPTION
System shuts off. Restarts when
power is restored.
PILOT FLAME FAILURE
Second main operator closes.
Module starts trial for ignition.
safety lockout
S8600H provides 100 percent shutoff, or safety lockout. A timer
starts timing the moment the trial for ignition starts. Ignition spark
continues only until the timed trial for ignition period ends. Then
the module goes into safety lockout. Lockout de-energizes the
first main valve operator and closes the first main valve in the gas
control, stopping pilot gas flow. The control system must be reset
by setting the thermostat below room temperature for one minute
or by turning off power to the module for one minute.
Main Burner operation
When the pilot flame is established, a flame rectification circuit
is completed between the sensor and burner ground. The flame
sensing circuit in the module detects the flame current, shuts off the
spark generator and energizes the second main valve operator. The
second main valve opens and gas flows to the main burner, where
it is ignited by the pilot burner. The flame current also holds the
safety lockout timer in the reset (normal) operating condition.
When the call for heat ends, both main valve operators are de-en-
ergized, and both main valves in the gas control close.
caUtion:
Label all wires prior to disconnection when
servicing controls. Wiring errors can cause improper and
dangerous operation. Verify proper operation after servicing.
interMittent pilot troUBleshootinG