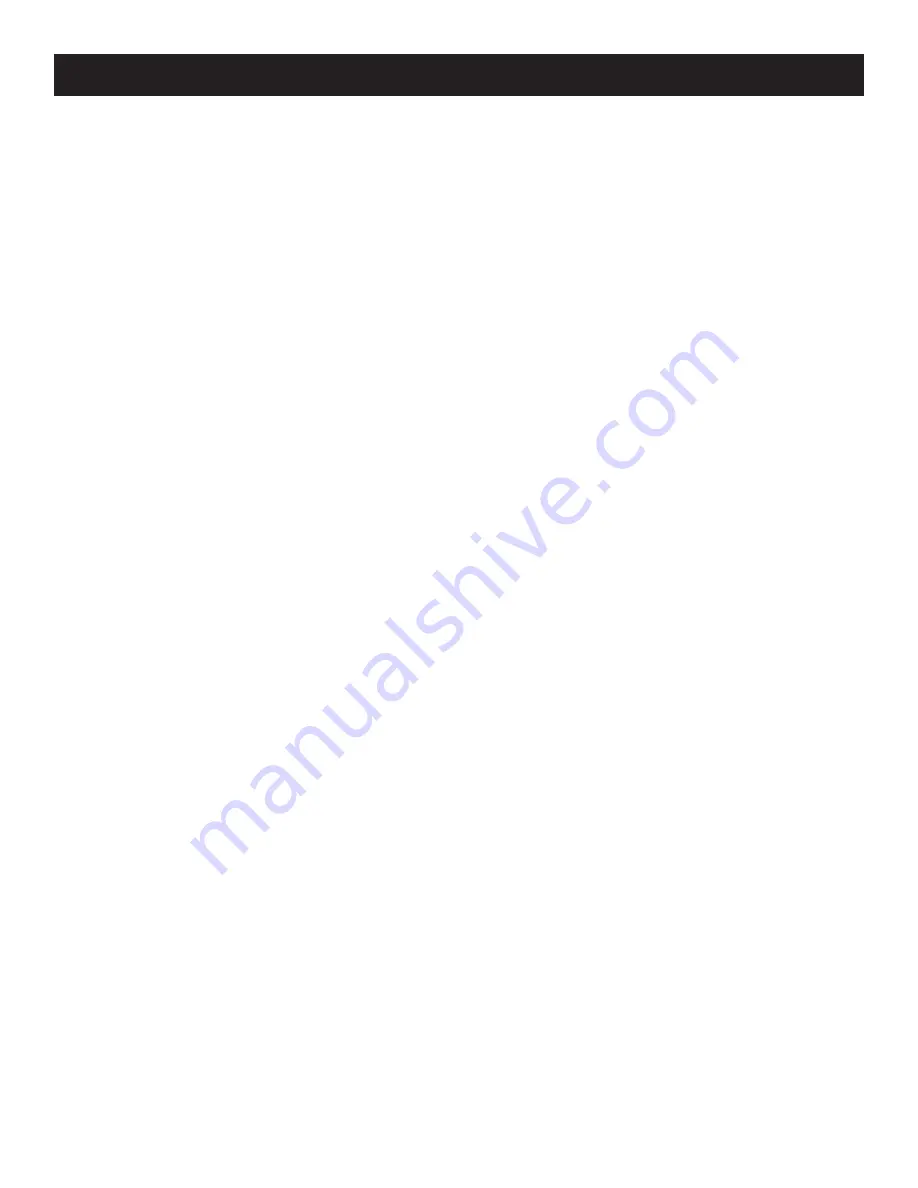
28649-2-0811
Page 64
RF MAINTENANCE INSTRUCTIONS
MAINTENANCE
Maintenance frequency must be determined individually for each
application. Some considerations are:
•
Exposure to water, dirt, chemicals and heat can damage the
gas control and shut down the control system.
•
Cycling frequency. Appliances that may cycle 20,000 times
annually should be checked monthly.
•
Intermittent use. Appliances that are used seasonally should
be checked before shutdown and again before the next use.
•
Dusty, wet or corrosive environment. Because these environ
-
ments can cause the gas control to deteriorate more rapidly,
the system should be checked more often.
•
Any control should be replaced if it does not perform properly
on checkout or service. In addition, replace any module if it is
wet or looks like it has been wet.
SERVICE
Do not disassemble the gas control; it contains non-replaceable
components. Attempted disassembly or repair can damage the
control.
Exactly follow the warnings and the lighting instructions.
1. Before lighting, smell around the appliance area for gas. If
the appliance uses LP (bottled) gas, be sure to smell next to
the floor because LP gas is heavier than air. If you smell gas,
immediately shut off the manual valve in the gas piping to the
appliance or on LP at the tank. Do not try to light any appli-
ance. Do not touch any electrical switch or use the phone.
Leave the building and call your gas supplier. If your gas sup-
plier cannot be reached, call the fire department.
2. The gas control must be replaced if it has been flooded with
water. Call a qualified service technician.
3. The gas control is a safety device. It must be replaced in case
of any physical damage such as bent terminals, missing parts,
stripped threads, or evidence of exposure to excessive heat.
Follow the operating instructions provided by the manufacturer of
your heating appliance.
TROUBLESHOOTING
IMPORTANT: All service and trouble-shooting procedures should
be performed by an experienced qualified service technician.
If the pilot will not stay lit:
1. Confirm that the “S” wire and the “I” wire are properly con
-
nected to the Control Module “S” and “I” terminals.
2. Confirm that the Spark to Pilot burner is properly grounded to
the Gas Control Valve and the Control Module.
3. Check the power source from the 6-volt power adaptor or the
Battery Back-up pack connection and condition of batteries.
4. Check the position of the CONTINUOUS PILOT switch on the
Control Module. If main burner does not come ON when the
manual switch and remote control is turned ON:
a. Confirm that the pilot sparks and lights.
b. Check the two (2) pin plastic connectors that plug into the
face of the Gas Control valve.
c. Confirm that the Gas Control valve is properly grounded
to the Control Module.
OPTIONAL GAS CONVERSION KITS
Please contact your dealer or distributor for the proper Conversion
kit for these fireplace models. Conversion kits will include com
-
plete instructions, minimum rate screw, plus the pilot and main
burner orifice for the gas type required. The AF-4040 Electronic
Gas Control Valve is convertible to use either natural or propane
gas by simply turning a small Rotary knob located at the front of
the gas valve. This rotary knob is located under a small rubber cap
and should only be adjusted when converting gas type.
CAUTION:
The gas type has been pre-set at the factory and must
not be changed unless a complete conversion is made which in-
cludes changing of the gas pilot injector, minimum rate screw and
main burner orifice.