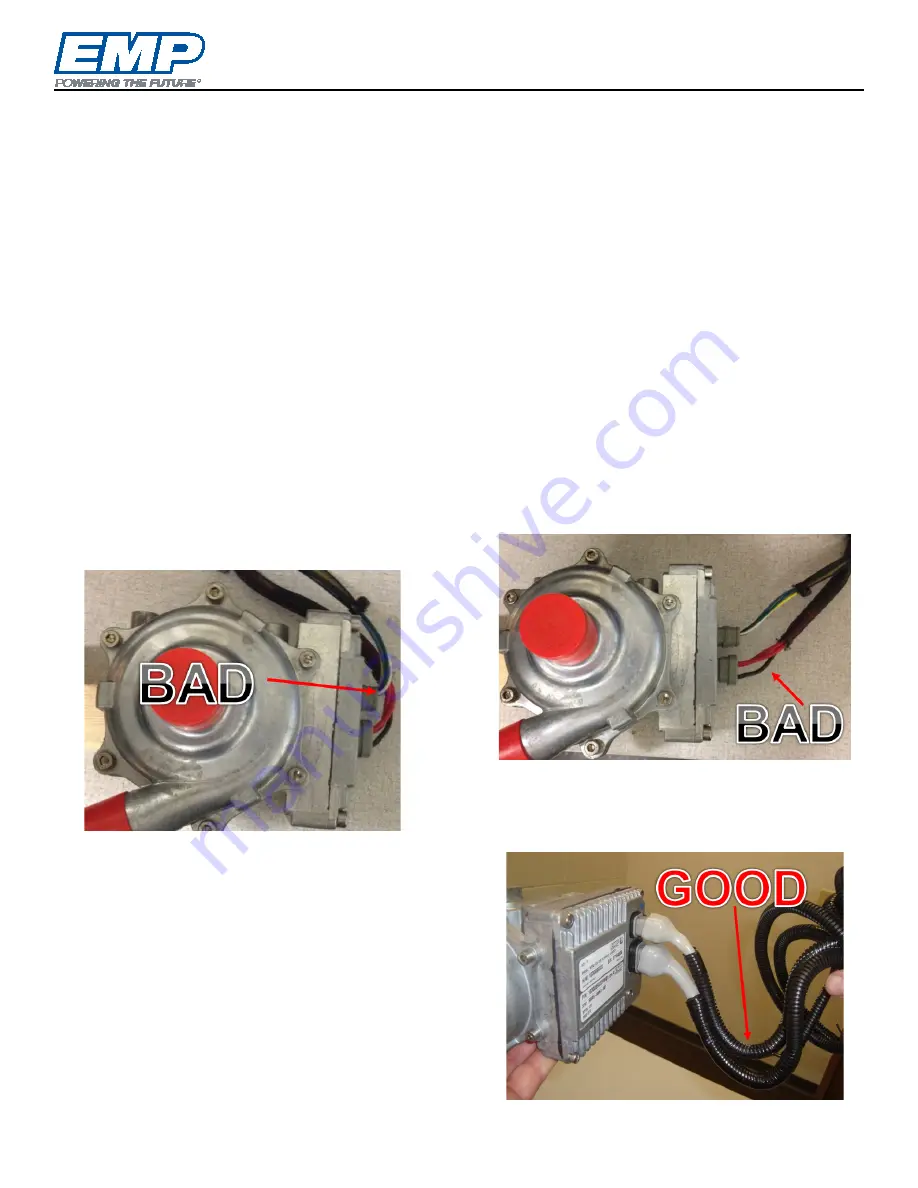
Installation
© 2017 EMP, Inc.
14
Wiring
For complete connector body sealing; the ignition, power, and ground wires should be 12ga minimum. Wire
jacket diameter must be compatible with seal requirements
Recommended Wiring Practices
•
Wiring or electrical harness must not rub on sharp edges.
•
The electrical harness should not be stressed at connections. Wires pulling on connectors can
compromise the connector body seal and possibly create a water intrusion event.
•
The voltage drop between the battery and the pump should not exceed 5% of the rated battery voltage.
This should be verified at the pump’s maximum current draw. Wiring or electrical harness must not rub
or make contact with a hot surface. There should be 5" minimum clearance from the exhaust.
•
Wiring or electrical harness should be supported at least every 18" to 20".
•
To avoid possible fire or shock, do not pinch any wiring or electrical harnesses.
•
Incorporate Drip Loops into wiring designs. The pump connectors are environmentally sealed.
However, good wire management can help ensure a good seal over the life of the product. Drip loops
collect water and shed it away from connector.
•
The use of Dielectric Grease such as Dow Corning DC-4 is acceptable as long as the connection is
mated directly after grease application to prevent dirt from being captured by the grease.
NOTE: Wires pulling on connectors can
compromise the connector body seal and possibly
create a water intrusion event. This is
unacceptable wire routing.
Bad Wiring – Harness stressed at connections
NOTE: Wire routing can provide a path for water
to flow down into the connector. This is
unacceptable wire routing.
Bad Wiring – No drop loops
NOTE: Drip loops collect water and shed it away
from connector. This is acceptable wire routing.
Good Wiring – Drip loops