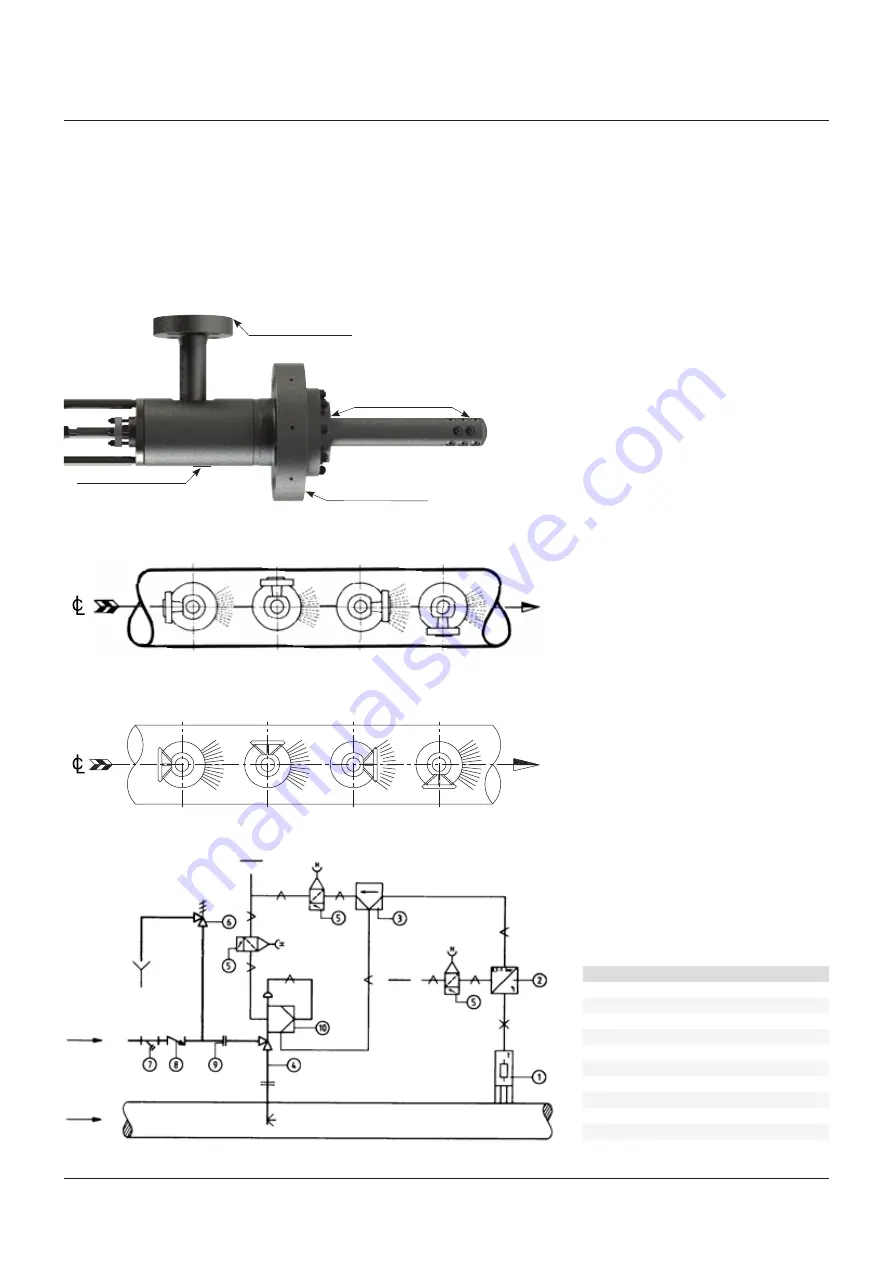
2
HWW HWN HWe HWs
Fp9
Fp12
Fp3
Fp6
FIgure 4
FIgure 3
Water flange positions
steam line
steam flow
Handwheel positions
steam line
steam flow
air
air
Water
steam
YArwAY
TemplowHT desuperHeaTer
InstallatIon and MaIntenance InstructIons
The minimum pipe run, required downstream
of the TemplowHT desuperheater, varies
with each individual application and would
be specified by Yarway at the enquiry stage.
This straight run is needed to prevent erosion
due to impingement of water droplets against
pipewalls, valves and fittings and is normally
item
Description
1
Temperature sensor
2
Temperature transmitter
3
Temperature controller
4
TemplowHT desuperheater
5
air filter regulator
6
safety relief valve
7
strainer
8
Check valve
9
Flange
10
e/p-positioner
FIgure 1 - Model 59/69/79
Check for damages
Identification plate
Check for damages
Check for damages
in the order of 4 to 6 meters, as a minimum (no
upstream straight length is normally required).
The distance from the TemplowHT desuperheater
to the temperature sensor is nominally 12 to
15 meters, although the distance specific to
the application would be advised by Yarway at
the enquiry stage. longer distances will ensure
that full evaporation of the water will take place
at lower steam velocities.
The temperature sensor should be located in
the upper half of the pipe, avoid branching of
the steam pipework between the TemplowHT
desuperheater and the sensor (see figure 4).