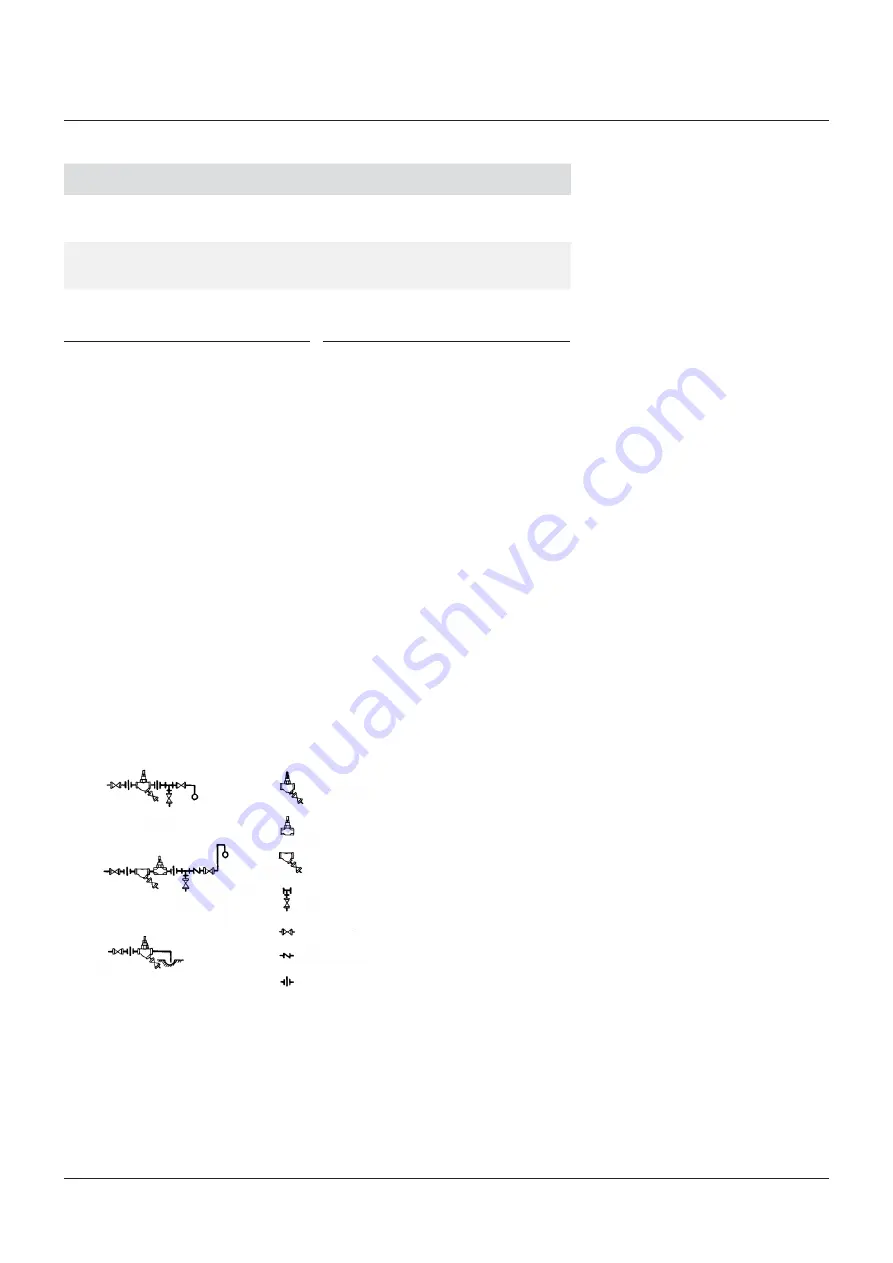
2
YARWAY
IMPULSE STEAM TRAPS, SERIES 60Y AND 60R
INSTALLATION, OPERATION AND MAINTENANCE MANUAL
RATINGS TABLE
Series
Max. working pressure
(MPa)
Max. working temperature
(°C)
DN
Strainer
60Y
4
400
15
Built-in
20
Built-in
25
Built-in
60R
4
400
32
-
40
-
50
-
SECTION 1 - INSTALLATION
1. Before installing trap, blow out piping
thoroughly to remove dirt, scale and metal
chips. Particularly with new piping systems,
be sure to blow out thoroughly.
2. Install trap in lowest position possible so
that condensate can flow to trap.
3. When trap is installed above the equipment
to be drained, provide a U-tube or lift
fitting at the bottom of riser in front of trap.
(This is done to attain a water seal effect.)
4. The trap can also operate when installed in
a vertical line discharging downwards, but
disassembly and inspection are easier to
carry out when installed horizontally with
bonnet on top. Verify that arrow on top of
body agrees with direction of flow.
5. Where freezing can occur, pitch line
downwards to assure no condensate
remains inside trap.
SECTION 2 - PIPING ARRANGEMENT
1. Follow the typical piping arrangement
shown in Figure 1.
2. Piping should be equal to or one size larger
than trap size.
3. Discharge piping should be at least equal
to trap size. Longer lines should be amply
sized to handle condensate and flash steam
simultaneously. If several traps discharge to
a common return line, amply sized lines must
be used to prevent excessive back pressures.
4. If discharge is to a closed return system,
install tee and test valve to enable inspection
of trap operation (Figures 1a and 1b).
5. If discharge of condensate is to discharge
piping above steam trap, install a check
valve to prevent backflow upon shutdown.
FIGURE 1
Trap strainer and fitting assembly detail
a. Discharge to return line below trap
(Trap series 60Y)
b. Discharge to overhead line
(Trap series 60R)
c. Discharge to Atmosphere
(Trap series 60Y)
Legend
Steam trap 60Y with blow down valve
Steam trap 60R
Strainer with blow down valve
Tee with test valve
Gate or globe valve
Swing check valve
Union