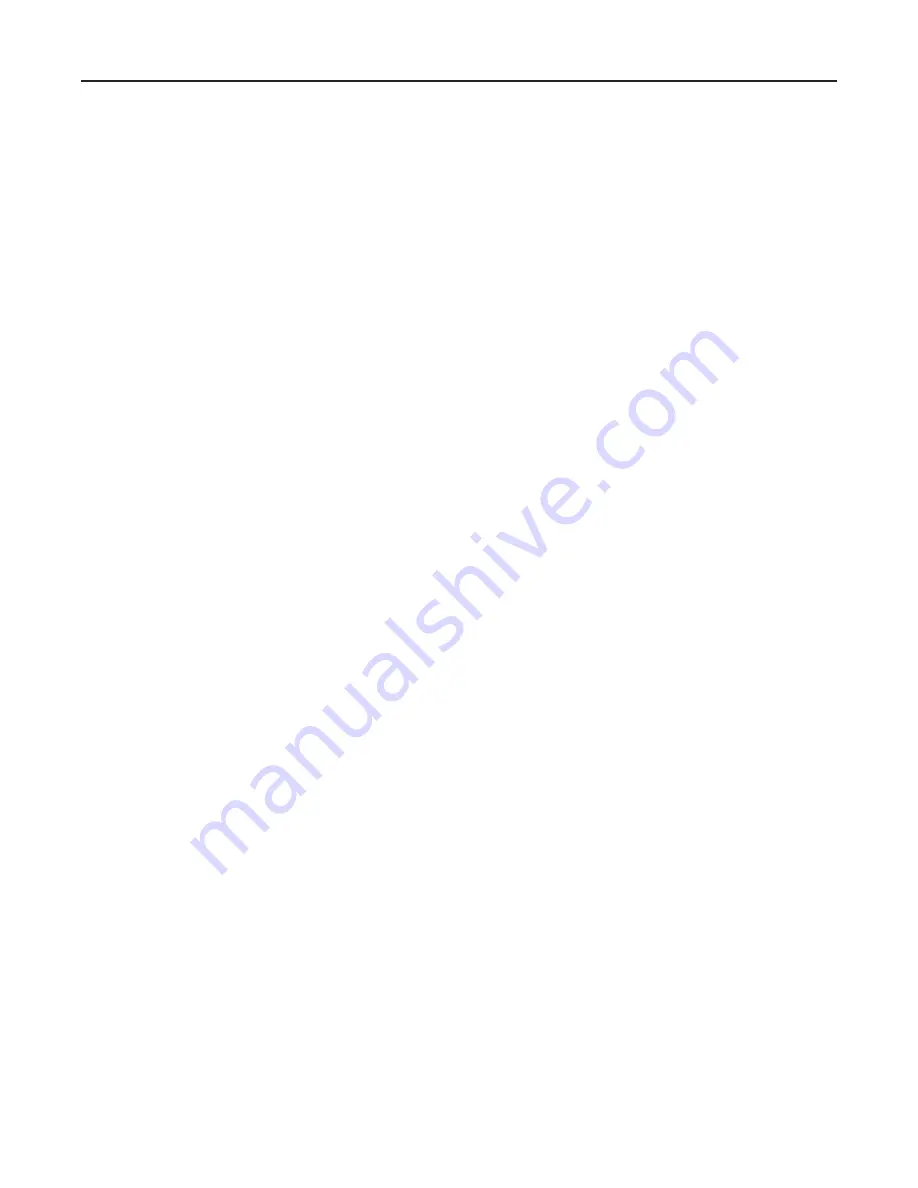
For regulator constructions with a
spring case vent, the vent should be
kept open to permit free flow of gas
to the atmosphere. Protect openings
against entrance of rain, snow, insects
or any other foreign material that may
plug the spring case vent or vent line.
All pressure equipment should be installed
in a non-seismic area; should not be
exposed to fire; and should be protected
from thunderbolt (lightning) strikes.
Planning
• Locate the valve in a straight run of horizontal pipe.
•
Allow headroom above the valve for access through
the blind flange.
•
Provide clearance for stem withdrawal underneath.
•
Prevent water hammer and erratic operation by
installing traps to provide proper drainage before
and after the valve and before secondary pressure
relief valve or control valve.
• Avoid damaging effects of scale and dirt in the pipe
lines by using a strainer as shown in Figure 3.
• Provide a 3-valve by-pass to facilitate inspection
without interrupting service.
• To eliminate excessive noise and erratic regulation
with steam and other compressible fluids, enlarge
the delivery pipe size to effect a reasonable
flow velocity at the reduced pressure. A tapered
transition is recommended.
• If possible, avoid a sharp turn close to the regulator
outlet and a bull-headed tee connection to the low
pressure main.
• Install initial and delivery pressure gages to
indicate performance.
• If the pressure rating of the delivery system or
connected equipment is less than the initial steam
pressure, provide a safety valve.
Main Valve
•
Flush the piping system thoroughly to clear it of
welding beads, scale, sand, etc.
•
Mount the main valve with diaphragm chamber
down and arrow on body pointing in the direction
of flow. Screwed end valves should be mounted
in unions.
Pilot
For Side Mount Construction
1. Mount the pilot on either side of the main valve by
means of 1/4 in. nipple and union provided.
2. Make this connection on the 1/4 in. pipe tap at the
inlet of the main valve as shown in Figure 4.
For Integral Mount Construction
1. Remove blind flange on pilot and mount on blind
flange of main valve using provided bolt.
2.
Screw 4A bleed port fitting into the 1/8 in. pipe tap
at the outlet of the main valve body. Note bleed
orifice in this fitting is vital to operation of regulator.
Note
As a general rule of thumb, tighten
1.5 to 3 turns past hand tight all NPT
connection and use thread sealant with
a temperature range up to 450ºF / 232ºC.
3.
Screw 8B tee into 1/8 in. pipe tap in pilot. Select
tap facing downstream.
4.
Screw 5A restriction elbow containing restriction
orifice into 1/8 in. pipe tap on the underside of
main valve diaphragm chamber. If the initial
pressure or pressure drop is less than 15 psi /
1.03 bar, use 5B open elbow.
5.
Connect tubing bends as illustrated in Figure 4.
Valves with condensation chamber are fitted up
according to Figure 4.
Control Pipe
1.
Use 1/4 in. pipe for this line which connect the
pilot diaphragm chamber to the desired point of
pressure control.
2. Take the control at a point of minimum turbulence.
Avoid control immediately at the valve outlet or
after a turn.
3.
When the delivery pipe expands in size, select a
spot at least 4 pipe diameters beyond the point
of enlargement.
4.
Pitch away from pilot to avoid erratic operation and
excessive fouling.
5.
Eliminate water pockets.
6. Locate delivery pressure gage in control pipe to
show pressure actually reaching pilot diaphragm
5
Type E