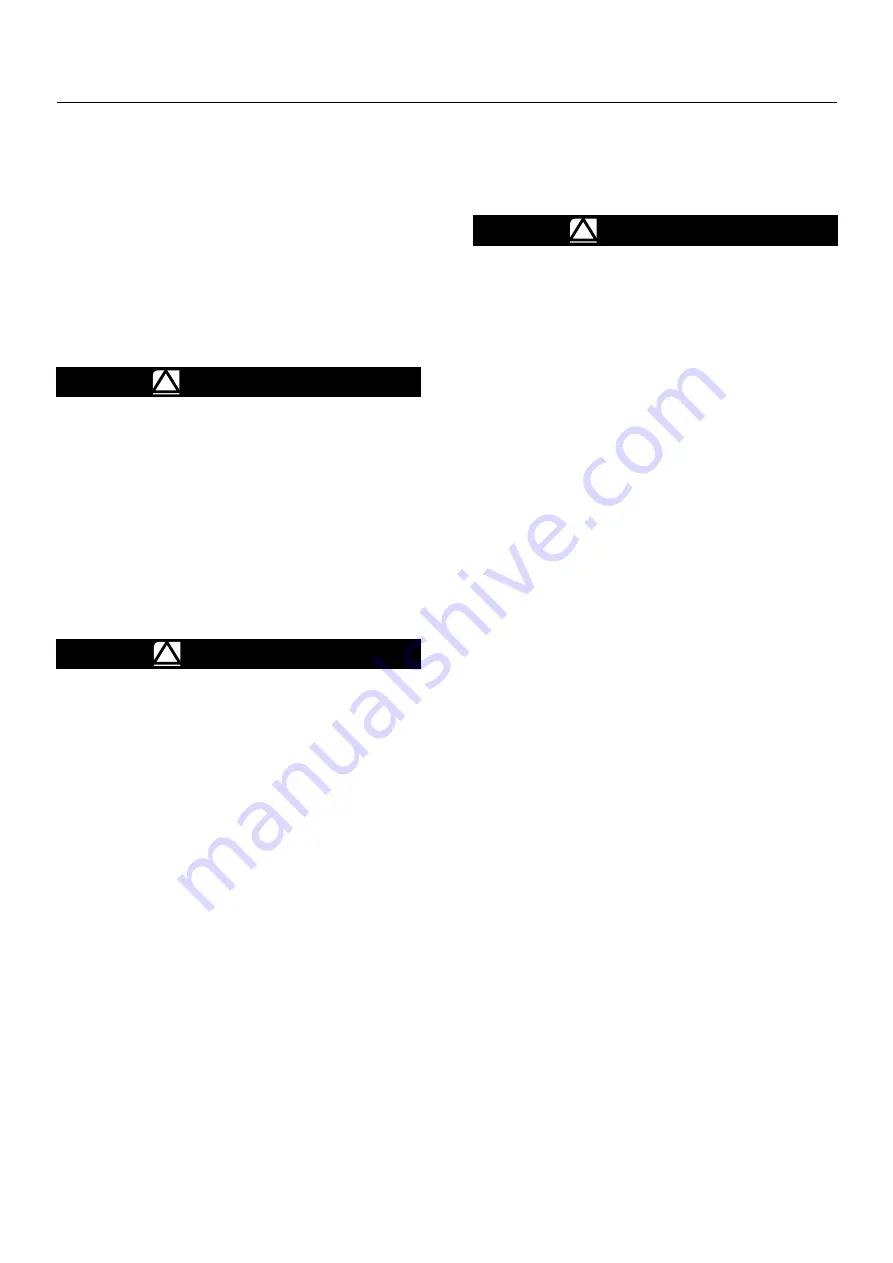
Type B/240
7
aDjuSTmENT
To change the outlet pressure, remove the closing cap
(key. 1) and turn the adjusting nut (key. 2) clockwise to
increase outlet pressure or counter clockwise to decrease
pressure.
Monitor the outlet pressure with a test gauge during the
adjustment.
Remount the closing cap (key. 1).
ShuTDOWN
!
WarNING
To avoid personal injury resulting from
sudden release of pressure, isolate the
regulator from all pressure before attempting
disassembly and release trapped pressure
from the equipment and pressure line.
In case of disassembly of main pressure re-
taining parts for checks and maintenance pro-
cedures, external and internal tightness tests
have to be done according applicable codes.
PErIODICaL ChECkS
CauTION
It is recommended that checks be made
periodically on the efficiency of the regulator
and pilots.
Regulator Checking
Slowly close the outlet cut-off valve and check pressure in
the length of pipe between the regulator and the valve.
If the system is functioning properly, an increase in outlet
pressure will be noticed due to lock-up pressure, after which
pressure will stabilize.
If, on the contrary, outlet pressure continues increasing, the
system is not functioning properly due to improper valve disc
tightness. In this case, close the valve located upstream of
regulator and carry out maintenance procedures.
Relief Valve Checking
(if installed)
Close the valve located downstream of regulator. Next,
connect a manual pump or other similar device to a
previously fitted impulse connection between the regulator
and the valve and raise the pressure until relief valve is
activated, i.e. until gas is released from vent.
Slam-Shut Controller Checking
(if installed)
See the Instruction Manual 0048EN-OS66-IM.
maINTENaNCE
(SEE FIGurE 6)
!
WarNING
all maintenance procedures must be
carried out only by qualified personnel. If
necessary, contact our technical support
representatives or our authorized dealers.
The regulator and it’s pressure accessories are subject
to normal wear and must be inspected periodically and
replaced if necessary.
The frequency of inspection/checks and replacement
depends upon the severity of service conditions and
according to applicable National or Industry codes,
standards and regulations/recommendations.
In accordance with applicable National or Industry codes,
standards and regulations/recommendations, all hazards
covered by specific tests after final assembling before
applying the CE marking, shall be covered also after every
subsequent reassembly at installation site, in order to ensure
that the equipment will be safe throughout its intended life.
Before proceeding with any maintenance work, shutoff the
gas upstream and downstream from the regulator, also
ensure that there is no gas under pressure inside the body
by loosening the upstream and downstream connections.
upon completion, check for leaks using suds.
General maintenance
a. Remove screws (key 56) and clamp (key 55) in order to
take off diaphragm case.
b. Remove bush (key 19) and balancing unit from the body
(key 21).
c. Remove centring unit (key 36) and spring holder (key 16)
and strip all parts down. Carefully clean all parts with
petrol and replace those which are found to be worn out.
d. Check pad holder unit (key 37).
e. By means of the appropriate tool, unscrew seat (key 22)
and check O-ring (key 35). Replace seat if worn or
scored.
f. Remove cap (key 1), ring nut (key 2) and spring (key 3),
taking care to mark the exact position of the ring nut for
remounting.
g. Remove screws (key 15) and take off cover (key 9).
h. Remove the diaphragm unit (key 14) from the servomotor
body (key 44).