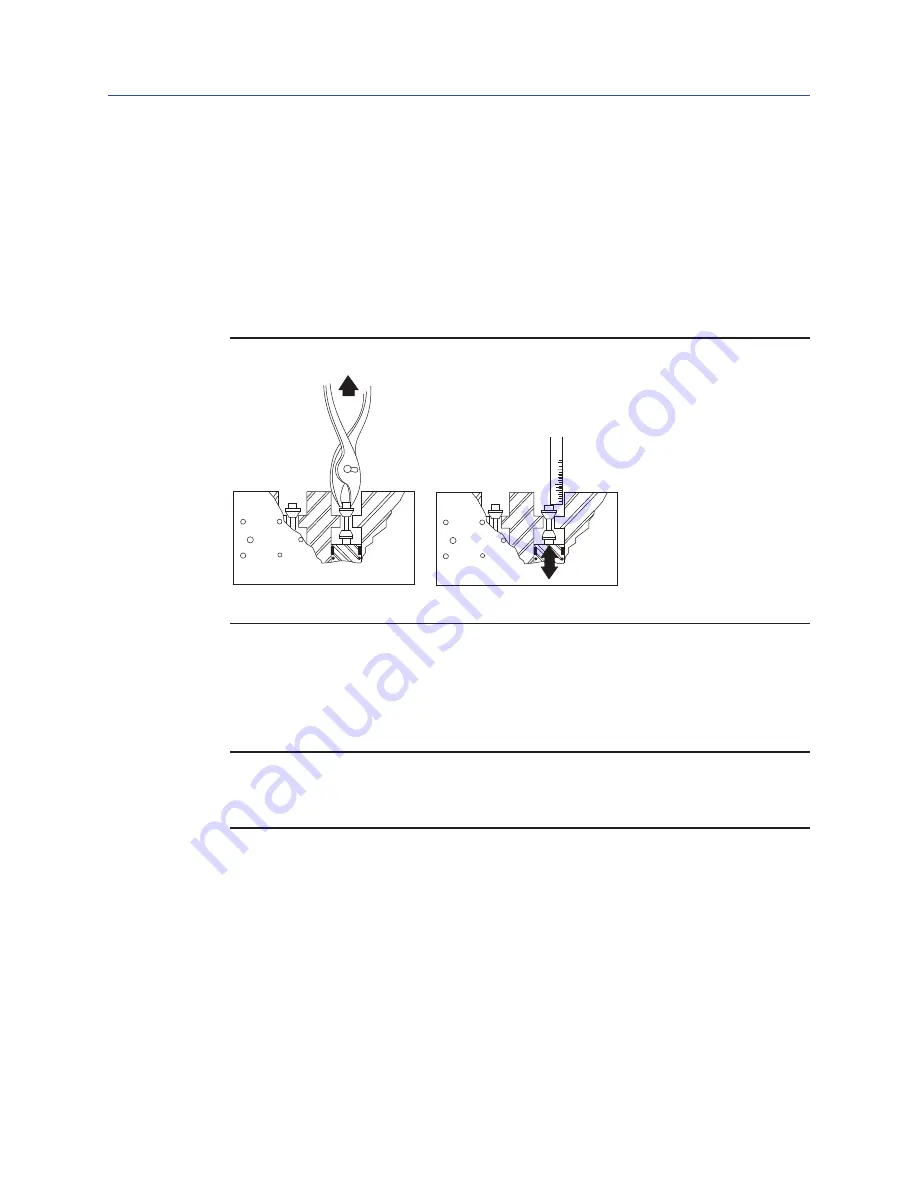
Installation, Operation and Maintenance Manual
PBC-01102001 Rev. A
January 2001
9
Section 4: Reconditioning and Assembly
Reconditioning and Assembly
Section: 4 Reconditioning and Assembly
4.1
Reconditioning
Power poppets have a raised boss for poppet spring engagement which may be grasped
with pliers for easy removal. Do not pry poppets off pins with a screwdriver as damage to
seats in the poppet block may result. Remove exhaust poppets from poppet pins.
Figure 8
FIGURE 8A
FIGURE 8B
4.2
Assembly
1.
Thoroughly clean all components. Inspect seats in poppet block for nicks,
scratches, pitting, etc.
NOTE:
Seat reconditioning may be accomplished by polishing with an emery cloth. Care must be
taken to maintain the radius at the outer edge of the poppet seat.
2.
Replace power and exhaust poppets on poppet pins. Poppets may be tapped
lightly into position with a drift pin and light hammer.
3.
Check travel of poppet assembly with the scale as shown in (Figure 8B).
Make any adjustment for travel by grinding or filing to shorten the poppet pin or
replace with a new pin if length is needed. Ref: 1/4" drill rod may be substituted
for poppet pins in the 1/4" assembly and 1/2" drill rod for the 1/2" assembly. Adjust
poppet travel to maintain 1/16" min. travel and 3/32" max. travel for both 1/4" and
1/2" assemblies (Poppet block size, 1/4" and 1/2", is designated by the diameter of
the poppet connecting pin.)
4.
Inspect and replace O-rings on pilot pistons. Place a small quantity of valve grease
in poppet spring recesses on caps (2) to insure that springs stay in place during
reassembly. Replace poppet block caps (2) insuring power poppet bosses are
engaged properly in poppet springs, replace caps (2), (6), levers, and bracket (29).