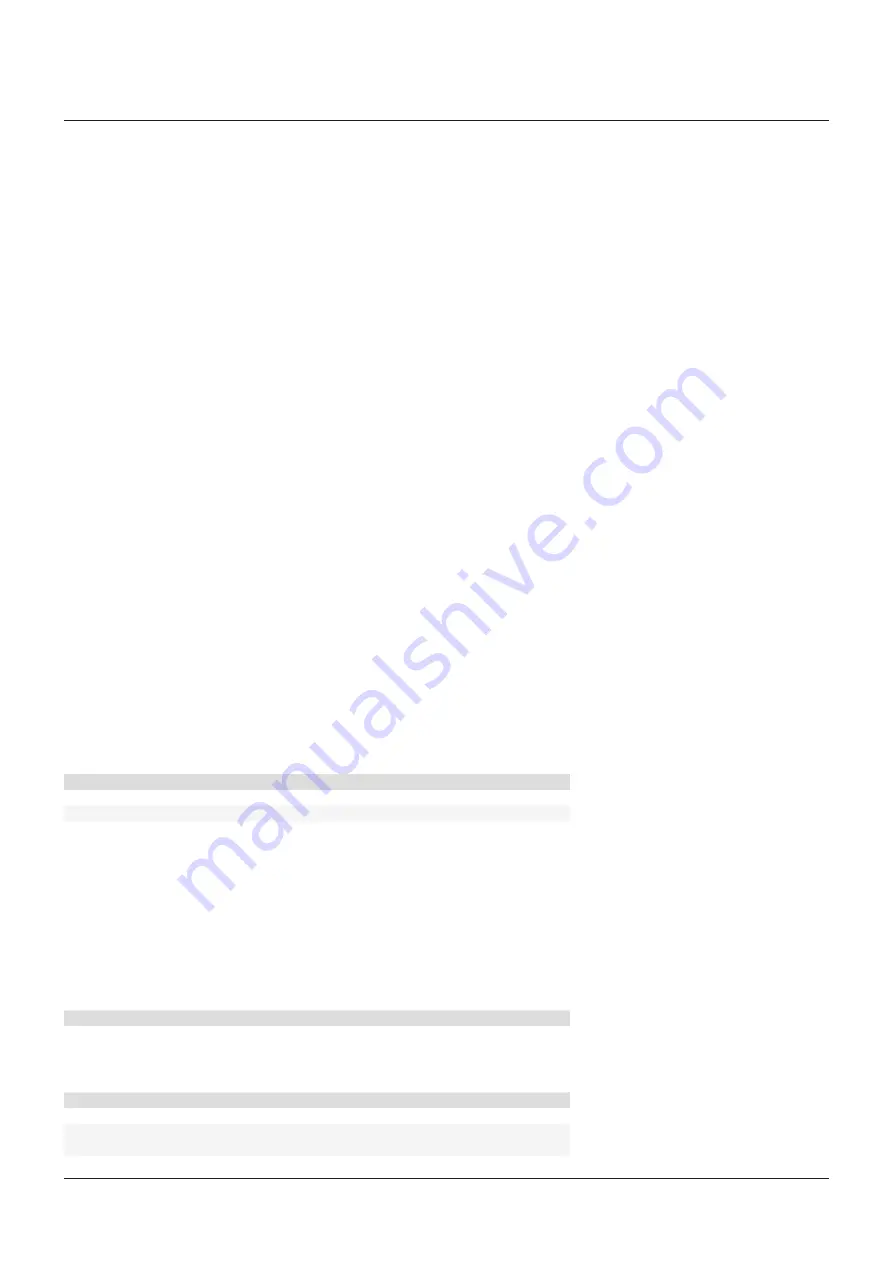
9
SEMPELL
SERIES S, TYPES SO, SC, SB, SOH FULL-LIFT SAFETY VALVES
OPERATING INSTRUCTIONS
5.3 Tools
• Torque wrench 17 - 55
• Fixed spanner 16 - 95
• Socket wrench 13 - 30
• Pin spanners in different sizes
• Safety ring pliers for outer rings
• Flatnose pliers, side cutting pliers
• Seal wire, lead seal, lead-sealing pliers
• Screwdriver for slotted-head screws long 5,5
• Screwdriver for fillister socket head
screws 5 - 14
• Hammer, punch
• Vernier calliper, depth gauge
• Lapping wheel according to valve seat
• Screw bolt M5 to M10
• Mark pen
• 2 ring screws M10 and M12
5.4 Operating materials
5.4.1 Lubricating the removable valve components
To lubricate the removable or detachable
valve components during assembly, use the
greases specified in Table A. Removable or
detachable valve components are all screw
connections, especially pressure-retaining
screw connections, and other components
within the distribution of forces. All removable
or detachable valve components are lubricated
with the same grease if they are lubricated in
the assembly process.
The operating temperature of the valve is
definitive for selecting the grease to be applied
for the removable valve components (cf. Table A).
5.5 Removing the valve bonnet
If only the seat shall be lapped, the complete
valve bonnet with compressed spring can be
removed.
Removal of valve bonnet with mounted
pneumatic drive A 160 see operating instruction
SEMSH-0067.
Remove lead seal. Take off cap (19, 20, 21).
Remove dowel (40) and turn spindle nut (22)
securely by hand (without tool!) against the
adjusting screw (17). In doing so, the spring
(15) becomes locked. Measure distance from
upper edge spindle (11) (or (7.2) (at orifice T1-Z),
SOH) to upper edge adjusting screw (17) and
register it. Loosen bonnet nuts (14) and lift off
valve bonnet with locked spring (15).
5.2 Disassembling indications
Observe disassembling sequence to preserve
the valve set pressure.
ATTENTION
Loosen bonnet nuts (14) only if the spring (15)
is locked or released as otherwise the bonnet
studs (13) cannot absorb the compression way of
the spring (15).
For working at nuts (18, 22) or adjusting
screw (17), secure the spindle (11) (or (7.2)
(at orifice T1-Z), SOH) against rotating as
otherwise the valve seat (2.1) or the bellows (8)
can be damaged.
ATTENTION
The dismounted valve bonnet must not be
disassembled further in any case.
TABLE A - Greases for lubricating the removable valve components
Design temperature of the valve T
B
Grease
T
B
< 400°C
Molykote
®
BR 2 Plus
[1]
400°C ≤ T
B
< 700°C
Molykote
®
P 37
[1]
1. Before applying the grease, ensure that the surfaces are metallically blank (free of oil, grease, etc.)
and free of dirt particles.
The greases specified in Table A are manufactured and/or supplied by the following
manufacturers and/or suppliers:
Molykote
®
BR 2 Plus - Dow Corning GmbH Wiesbaden, Rheingaustr. 34, 65201 Wiesbaden
Molykote
®
P 37
- Dow Corning GmbH Wiesbaden, Rheingaustr. 34, 65201 Wiesbaden
5.4.2 Lapping abrasives
It is necessary to use special lapping abrasives
that contain finely distributed hardened
particles for lapping seat surfaces on body and
disk seats. The lapping abrasive specified in
Table B is recommended by Sempell
5.4.3 Further operating materials
Further required operating materials and
their usage are specified in Table C and are
manufactured and/or supplied by the following
manufacturers and/or suppliers
TABLE B - Lapping abrasives, suitable for the finishing of valve seats
Lapping abrasive
Manufacturer / Supplier
TETRABOR
®
Boron carbide (F 100 - F 1200)
ESK Ceramics GmbH & Co. KG Max - Schaidhauf-Str. 35,
87437 Kempten - Germany
TABLE C - Further operating materials
Usage
Type
Manufacturer / Supplier
Degreasing agent
Isopropylalkohol (2-Propanol)
Assembly lubricant (colloidal graphite)
for parts in contact with the medium
DAG
®
156
Acheson Industries, Dornstadt
ATTENTION
For oxygen application all parts in contact with
the medium must be free from oil and grease.
Danger of explosion.