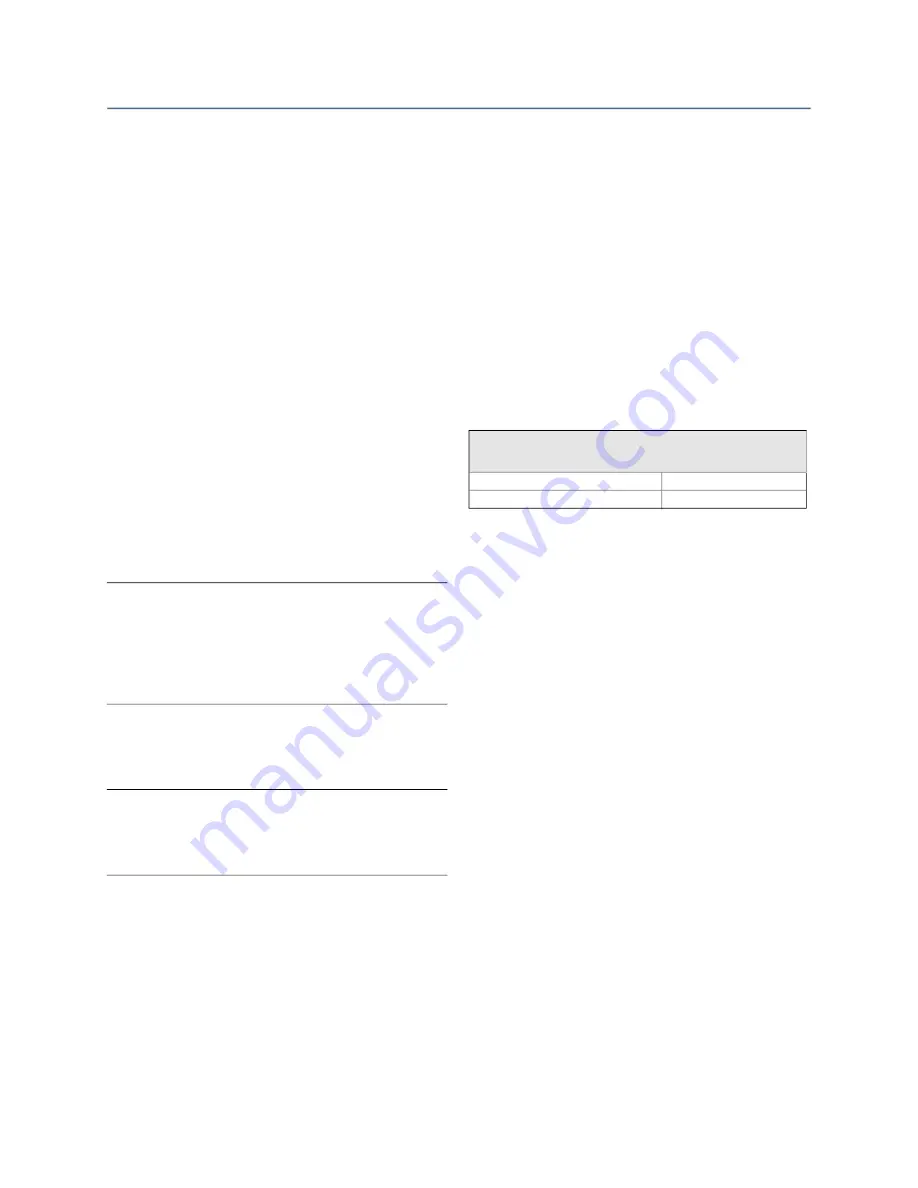
95
Rosemount 8600 Vortex Flow Meter
Reference Manual
May 2019
Specifications and Reference Data
00809-0100-4860, Rev BF
A.4 Performance specifications
The following performance specifications are for all
Rosemount models except where noted. Digital
performance specifications applicable to Digital HART
output.
A.4.1 Flow accuracy
Includes linearity, hysteresis, and repeatability.
Liquids - for Reynolds Numbers over 20,000
Digital and pulse output
± 0.75% of rate
Analog output
Same as pulse output plus an additional 0.025% of span
Gas and steam - for Reynolds Numbers over 15,000
Digital and pulse output
± 1% of rate
Analog output
Same as pulse output plus an additional 0.025% of span
Accuracy limitations for gas and steam:
Max velocity of 100 ft/s (30.5 m/s)
Note
As the meter Reynolds Numbers decreases below the
stated limit to 10,000 the accuracy error band will
increase linearly to +/-3.0%. For Reynolds Numbers
down to 5,000 the accuracy error band will increase
linearly from +/-3.0% to +/-10.0%.
Process temperature accuracy
2.2 °F (1.2 °C).
Note
For remote mount installations, add ±0.018 °F/ft.
(±0.03 °C/m) of uncertainty to the temperature
measurement.
Mass flow accuracy for temperature compensated mass
flow
Digital and pulse output
± 2.5% of rate (Nominal)
Nominal conditions include temperature variation in
saturation and superheat at 150 psig (10 bar-g) and
above.
For pressure below 150 psig (10 bar-g), add 0.08% of
uncertainty for every 15 psi (1 bar) below 150 psig (10
bar-g).
Analog output
Same as pulse output plus an additional 0.025% of span
Repeatability
± 0.2% of actual flow rate
Stability
± 0.1% of rate over one year
Process temperature effect
Automatic K-factor correction with user-entered process
temperature.
indicates the percent change in K-factor per 100
°F (55.5 °C) in process temperature from reference
temperature of 77 °F (25 °C).
Ambient temperature effect
Digital and pulse outputs
No effect
Analog output
±0.1% of span from –58 to 185 °F (–50 to 85 °C)
Vibration effect
An output with no process flow may be detected if
sufficiently high vibration is present.
The meter design will minimize this effect, and the factory
settings for signal processing are selected to eliminate
these errors for most applications.
If an output error at zero flow is still detected, it can be
eliminated by adjusting the low flow cutoff, trigger level, or
low-pass filter.
As the process begins to flow through the meter, most
vibration effects are quickly overcome by the flow signal.
Vibration specifications
Integral aluminum housings and remote aluminum
housings
At or near the minimum liquid flow rate in a normal pipe
mounted installation, the maximum vibration should
be 0.087-in. (2,21 mm) double amplitude displacement
or 1 g acceleration, whichever is smaller. At or near the
minimum gas flow rate in a normal pipe mounted
installation, the maximum vibration should be 0.043-in.
(1,09 mm) double amplitude displacement or
1
/
2
g
acceleration, whichever is smaller.
Table A
-
13. Process Temperature Effect
Percent Change in K-Factor per
100 °F (55.5 °C)
< 77 °F (25 °C)
+ 0.23
> 77 °F (25 °C)
- 0.27