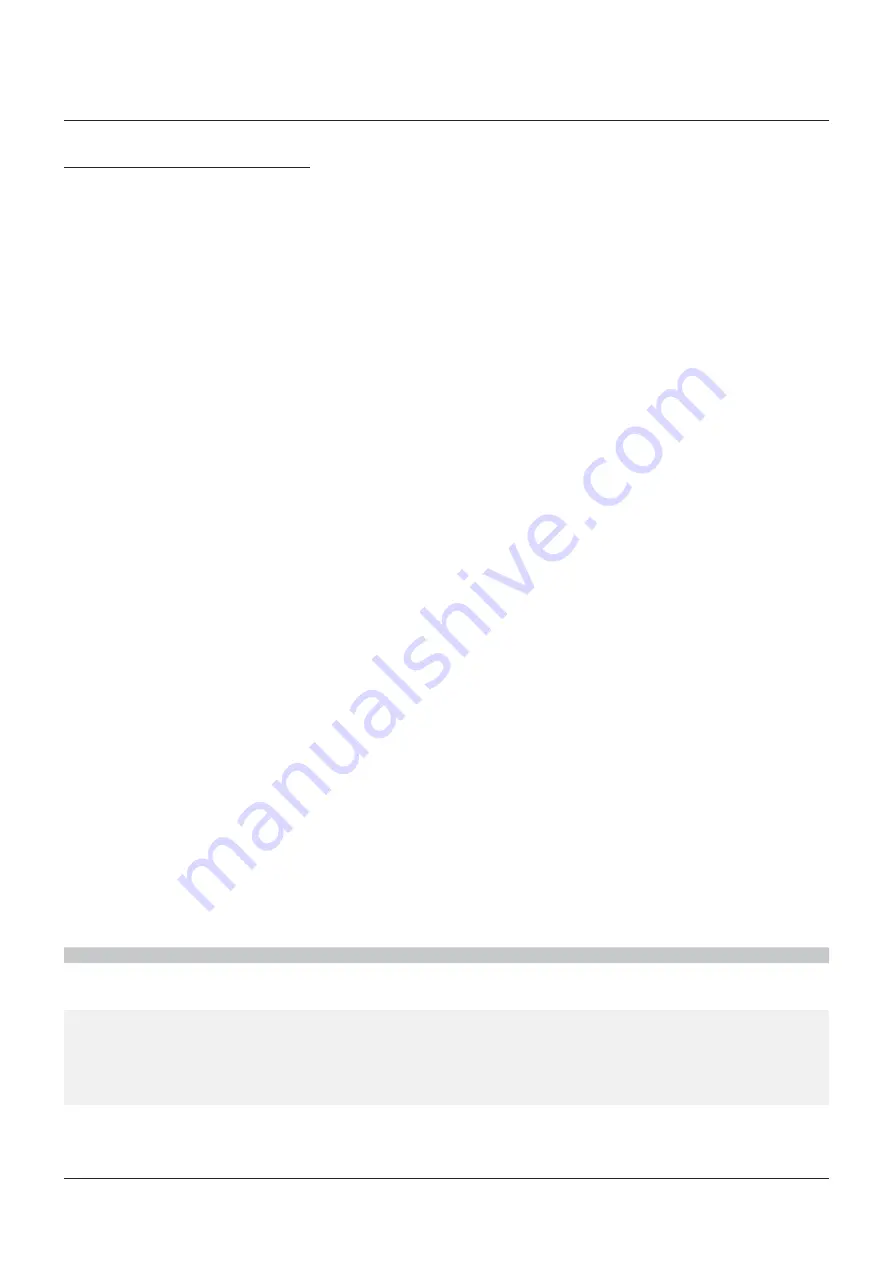
5
PENBERTHY
MODELS U, L AND 2NC FABRICATED METAL CONSTRUCTION JET PUMPS
INSTALLATION, OPERATION AND MAINTENANCE INSTRUCTIONS
6 MAINTENANCE
WARNING
Maintenance should only be undertaken by
qualified, experienced personnel who are
familiar with this equipment and have read and
understood all the instructions in this manual.
DO NOT proceed with any maintenance unless
the jet pump has been relieved of all pressure
or vacuum, has been allowed to reach ambient
temperature and has been drained or purged of
all fluids. Failure to follow these instructions may
cause a sudden release of pressure resulting in
personal injury or property damage.
6.1 Preventative maintenance
The user must create maintenance schedules,
safety manuals and inspection details for each
specific installation of a jet pump.
On all installations the following items should
be evaluated regularly by the user for purposes
of maintenance:
1. Jet pump for corrosion or debris build up.
2. Piping and fittings for corrosion or debris
build up.
3. All connections for tightness.
4. Units for wear.
5. Strainers for debris build up.
The user must determine an appropriate
maintenance schedule necessary for his or her
own specific application, upon evaluation of
his or her own operating experience. Realistic
maintenance schedules can only be determined
with full knowledge of the services and
application situation involved.
TABLE 3 - TROUBLESHOOTING
Problem
Cause
Solution
Wet steam
1. Steam temperature not high enough
1. Drain steam inlet lines and install a steam separator in the line or add a steam
superheater to raise steam temperature to about 10°F (-12°C) above saturation
temperature for particularly critical low flow units.
Jet pump not performing up to capacity 1. Low steam pressure
1. Check steam pressure with a recently calibrated steam pressure gauge.
If steam pressure cannot be increased, contact an authorized Penberthy
distributor for assistance
2. Motive steam nozzle becomes plugged 2. Clean out and install a strainer in the motive steam line
3. Air leakage into vacuum system
3. Hydrostatic and vacuum test unit to locate leaks
4. Superheated steam
4. Contact an authorized Penberthy representative for assistance
6.2 System shut down
WARNING
Safety procedures must be taken if hazardous
gases are being discharged from the Z stage
ejector. Failure to follow safety procedures may
cause severe personal injury or property damage.
Shut down of model 2NC ejector systems may
follow the start up procedure in reverse or both
stages may be shut down simultaneously.
When a system is shut down and the pressure
in the vacuum is still below atmospheric
pressure, air will rush back into the process
vacuum system. Since this action may create
a harmful result to the product or may create
a hazardous or explosive condition, it is
recommended that the customer assess this
problem prior to unit installation to protect
against the event of such occurrences.
Installing a manual shut-off valve in the suction
line as close to the ejector as possible will help
prevent such an occurrence.
Another method of preventing the back flow
of air into the vacuum system is to break the
system vacuum by admitting inert gas into the
vacuum vessel.
6.3 Troubleshooting (see table 3)