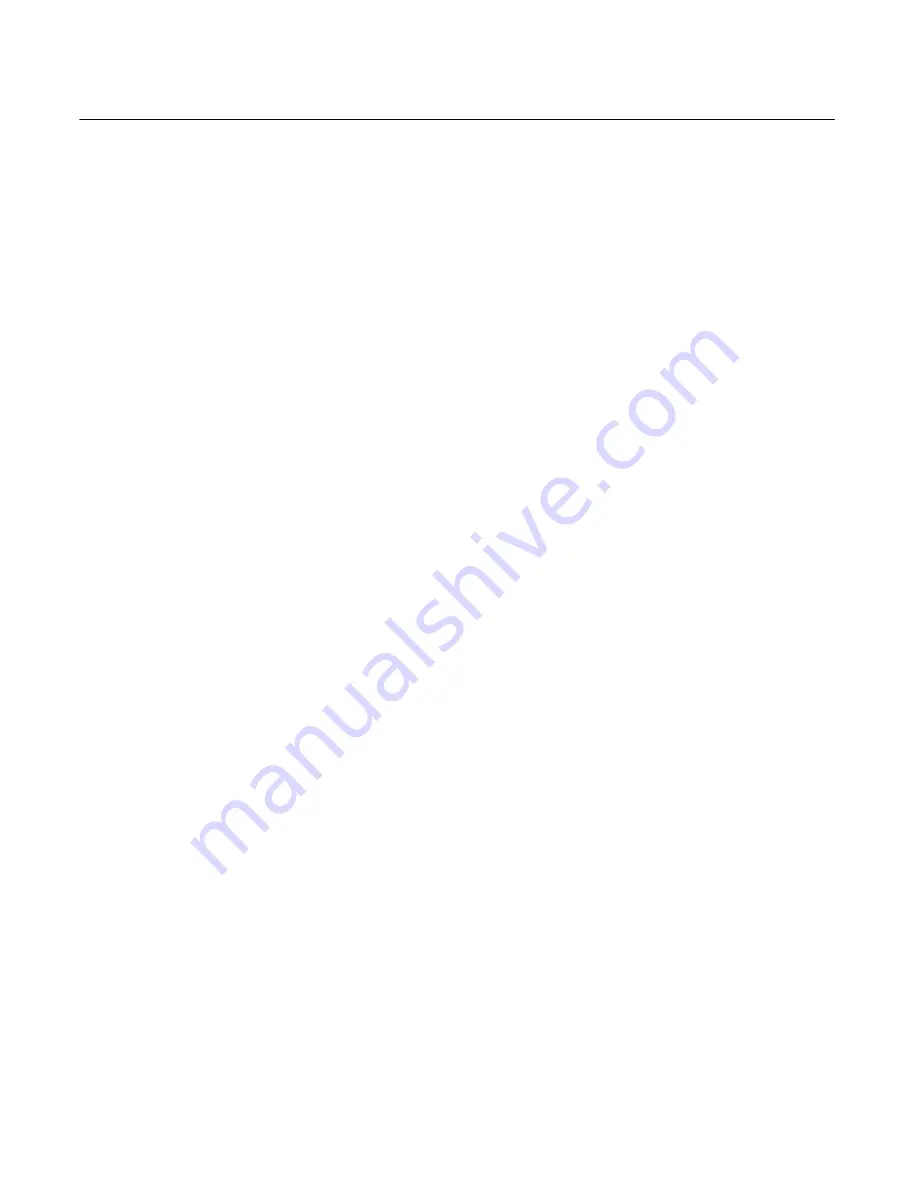
Type 2500
Instruction Manual
Form 1013
December 2005
19
D
For Reverse Acting Type 2500, 2500T
, 0.2
bar (3 psig) for a 0.2 to 1.0 bar (3 to 15 psig) output
or 0.4 bar (6 psig) for a 0.4 to 2.0 bar (6 to 30 psig)
output.
9. If the output pressure agrees with that shown in
step 8, proceed to step 10. If the output pressure
does not agree, go to step 11.
10. If the unit does not contain an indicator
assembly, go to the Startup section. If the unit
contains an indicator assembly, change the pointer
span by loosening the indicator plate screws (key
41, figure 16, detail of indicator assembly), slide the
plate until the HIGH mark is under the pointer.
Tighten the plate screws and go to the Startup
section.
Note
Any sliding of the level set arm (key
28, figure 16) in the following step
changes the zero as well as the output
pressure span.
11. To adjust the output pressure span, loosen the
two level set mounting screws (see figure 16) and
slide the flexure strip base (key 27) right or left along
the elongated slotted hole as follows:
D
To
increase
the output pressure span, slide
the flexure strip base away from the torque tube
shaft.
D
To
decrease
the output pressure span, slide
the flexure strip base toward the torque tube shaft.
Retighten the screws. If the flexure strip base has
been moved as far as possible and the output
pressure span is still too large or too small, proceed
12. Repeat the procedure from step 4 until the
required calibration points are obtained.
Note
Any change of the PROPORTIONAL
BAND or SPECIFIC GRAVITY
adjustment in the following step
changes the zero as well as the output
pressure span.
13. If the flexure strip base has been moved as far
as possible and the output pressure span is still too
large or too small, slightly adjust the
PROPORTIONAL BAND or SPECIFIC GRAVITY
adjustment as follows:
D
If the output pressure span is too large, slightly
increase the PROPORTIONAL BAND or SPECIFIC
GRAVITY setting.
D
If the output pressure span is too small, slightly
decrease the PROPORTIONAL BAND or SPECIFIC
GRAVITY setting.
14. Repeat the procedure from step 4 until the
required calibration points are obtained.
Note
If you cannot calibrate the controller or
transmitter, look for other problems as
described in the Troubleshooting
procedures, such as leaking
connections, or a binding displacer
rod. If none of these troubles are
apparent, ensure that the displacer is
sized correctly for the application.
Type 2500S and 2503 Controllers
1. Turn on the supply pressure and check that it is
set according to the appropriate prestartup checks
procedure.
2. Make sure that the PROPORTIONAL BAND
adjustment (Type 2500S only) is at the setting
determined according to the appropriate prestartup
check procedure.
3. Perform one or the other of the following:
D
For direct acting controllers
, set the RAISE
LEVEL adjustment between 1.0 and 1.5.
D
For reverse acting controllers,
set the RAISE
LEVEL adjustment between 3.5 and 4.0.
4. Set the process variable at the minimum value of
the input range as shown in table 5. For
constructions with an indicator assembly, make sure
that the pointer is over the LOW mark.
Note
In the following step, the alignment
screw (key 33, figure 16) must always
remain screwed in far enough to
provide spring tension on the
underside of the alignment screw
head.
5. Be sure the flapper is centered over the nozzle. If
not, loosen the hex nut (key 40, figure 16) and
reposition the flapper, tighten the hex nut.
6. Adjust the flapper (key 32, figure 16) as
described below. For coarse flapper adjustment,