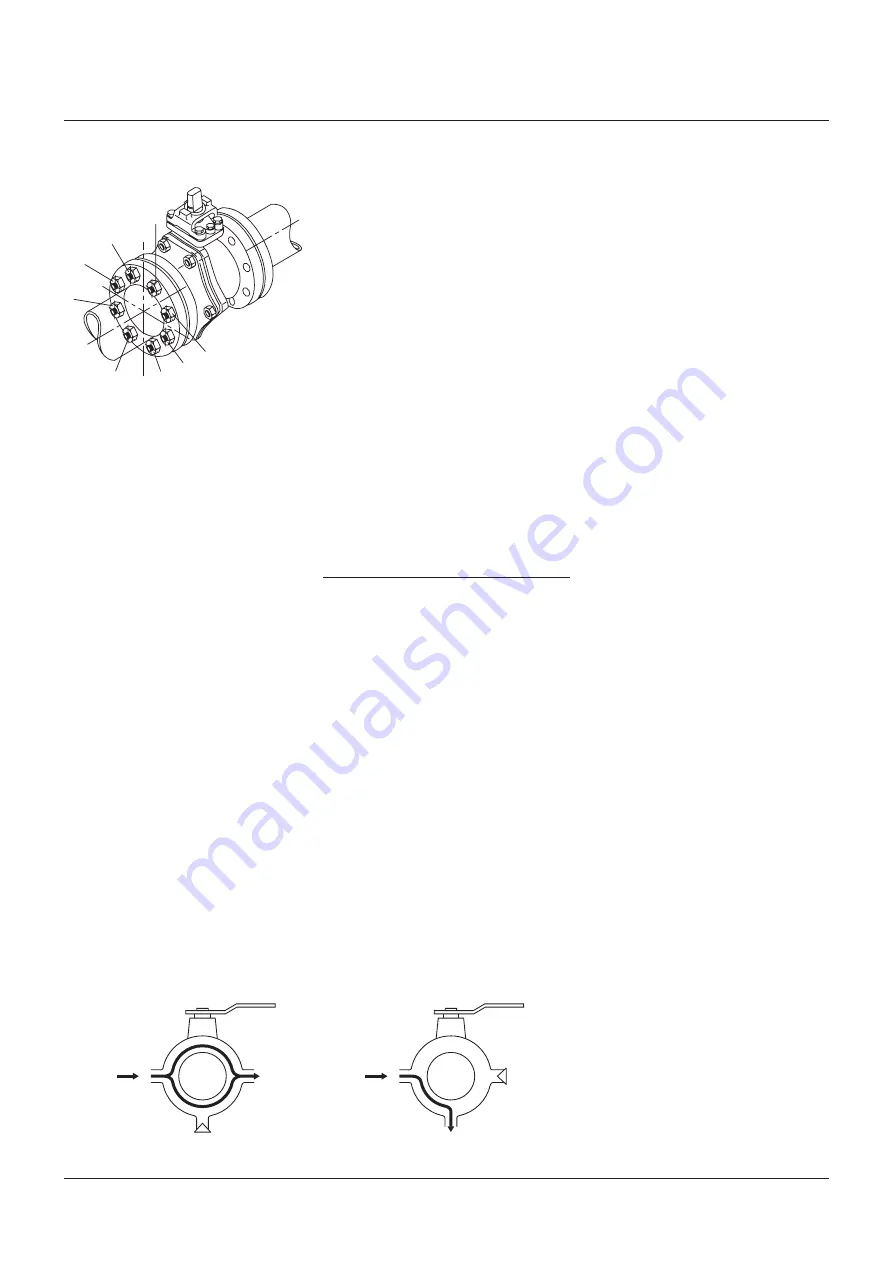
3
①
⑧
③
⑤
⑥
④
⑦
②
cauTion
1. Ensure that there are no solid objects such as
pieces of wood, plastic or packing materials
within the valve or on the valve seat. It is
recommended to flush pipes before installing
the valve. If this is not possible, the installed
valve must be in its open position before
flushing takes place.
2. Unless otherwise recommended by KTM, the
valves should be installed with the ball in open
position to ensure that the seat rings are not
damaged during installation.
3. Use appropriate gaskets which comply with
standards or specifications.
4. Tighten the flange bolts with a closed wrench;
using a ‘crisscross’ pattern that alternately
tightens the bolts located 180 degrees apart.
(see Figure 1) Unequal partial tightening
places stress on lined pipes which may
damage the flange or produce excessive
operation torque.
FIgURe 1
tightening of bolt
6 piping
When piping the Jacketed ball valves, check
that no foreign objects will block the inlet,
outlet or draining port. Proper piping enables
the steam to flow effectively to warm the
jacketed part.
proper piping
Horizontal piping
Inlet
Outlet
draining port
improper piping
Horizontal piping
Inlet
Outlet
FIgURe 2
FIgURe 3
KTM
Jacketed ball valves
InstallatIon and operatIon manual
5. Failure to fabricate pipes without excessive
stress will result in leakage, poor operation
or failure of the valves.
6. When conducting a pressure test of the pipe
system, the valves should be in a partially
open or fully open position. Testing at closed
position will impose too much load and will
cause leakage from seats. Check for any
leakage from the joint flange and gland portion
during the pressure test. After conducting
the pressure test, return to full open/close
position at once.
7. If the piping system is pressurized with water
for testing, and if the piping system has been
shut down for a long time after testing, the
following measures should be taken:
- Use corrosion inhibitor with water to
pressurize the piping system.
- After testing, the piping system should be
depressurized and the test water completely
drained.
- Ensure that the corrosion inhibitor does not
leave a residue within the system as the
particulates may damage the valve sealing
surfaces.