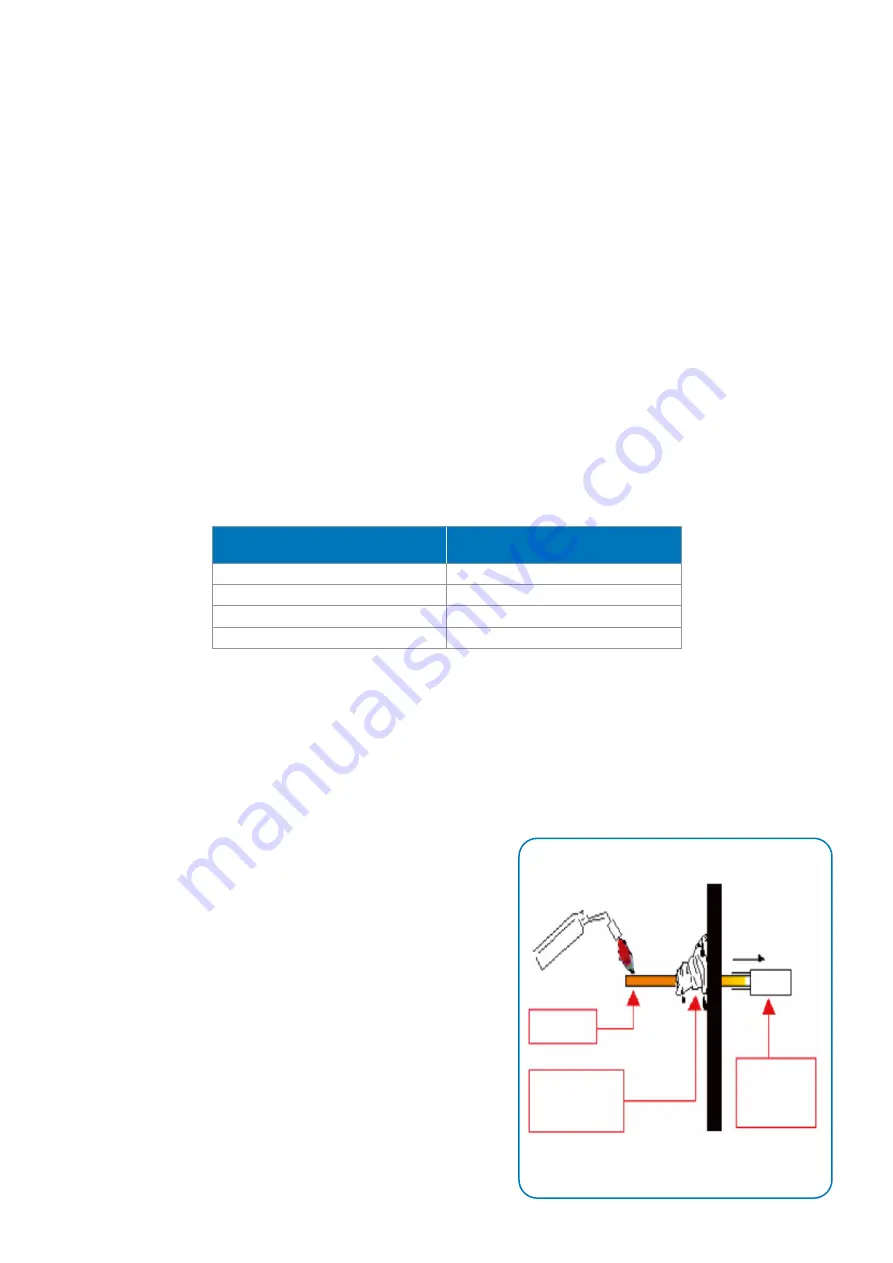
Tube Size
Max distance between
2 clamp support
12.7mm (1/2 inch)
1.20 m
16.0mm (5/8 inch)
1.50 m
22.0mm (7/8 inch)
1.85 m
28.5mm (1 1/8 inch)
2.20 m
OUTSIDE
INSIDE UNIT
End of Tube
During brazing
protecthousing
withdampcloth
During brazing
pull back fire
insulation
All interconnecting pipes should be of refrigeration grade, clean, dehydrated and must remain capped at
both ends until installation. Even during installation, if the system is left for any reasonable period (say
two hours), pipes should be re- capped to prevent moisture and contaminants from entering the system.
Do not assume that the service connection sizes on the unit (at the service valves) are the correct size to
run your interconnecting refrigeration pipes. The service valve sizes have been selected for convenience
of installation and in some cases (larger units) these may be considered too small. However, for the very
short pipe run within our units, these service connection sizes are adequate.
The pipe should be sized to ensure optimum performance and good oil return. The sizing must also take
into account the full capacity range through which this particular unit will need to operate.
Pipe runs should be kept as short as possible, using the minimum number of directional changes. Use
large radius bends and avoid trapping of oil and refrigerant. This is particularly important for the suction
line. The suction line should ideally slope gently towards the unit. Recommendation slope is
1/200~1/250. P traps, double risers and reduced pipe diameters may be required for suction lines where
long vertical risers cannot be avoided. All pipes should be adequately supported to prevent sagging
which can create oil traps.
The recommended pipe clamp support distance is shown in the table.
Refrigeration Piping Installation
Brazing Recommendations
Maintain a flow of oxygen-free nitrogen through the system at a very low-pressure during brazing.
Nitrogen displaces the air and prevents the formation of copper oxides in the system. If copper
oxidization is allowed to form, the copper oxide material can later be swept through the system and
block screens such as those protecting capillary tubes, thermal expansion valves, and accumulator oil
return holes. This minimizes any entry of contaminants and moisture.
• Remove the liquid line connection cap.
• Then remove the suction connection cap.
• Open both valves midway. Care should be taken to
avoid the holding charge from releasing too quickly.
• Be sure tube fitting inner diameter and tube outer
diameter are clean prior to assembly.
• Since both tubes are extended from the condensing
unit housing, we recommend insulating the housing by
using a wet cloth on the copper tubing.
• Recommended brazing materials: a copper /
phosphorous or copper/ phosphorous / silver alloy rod
should be used for joining copper to copper whereas to
join dissimilar or ferric metals, use a silver alloy rod,
either flux coated or with a separate.
• Use a double tip torch.
12