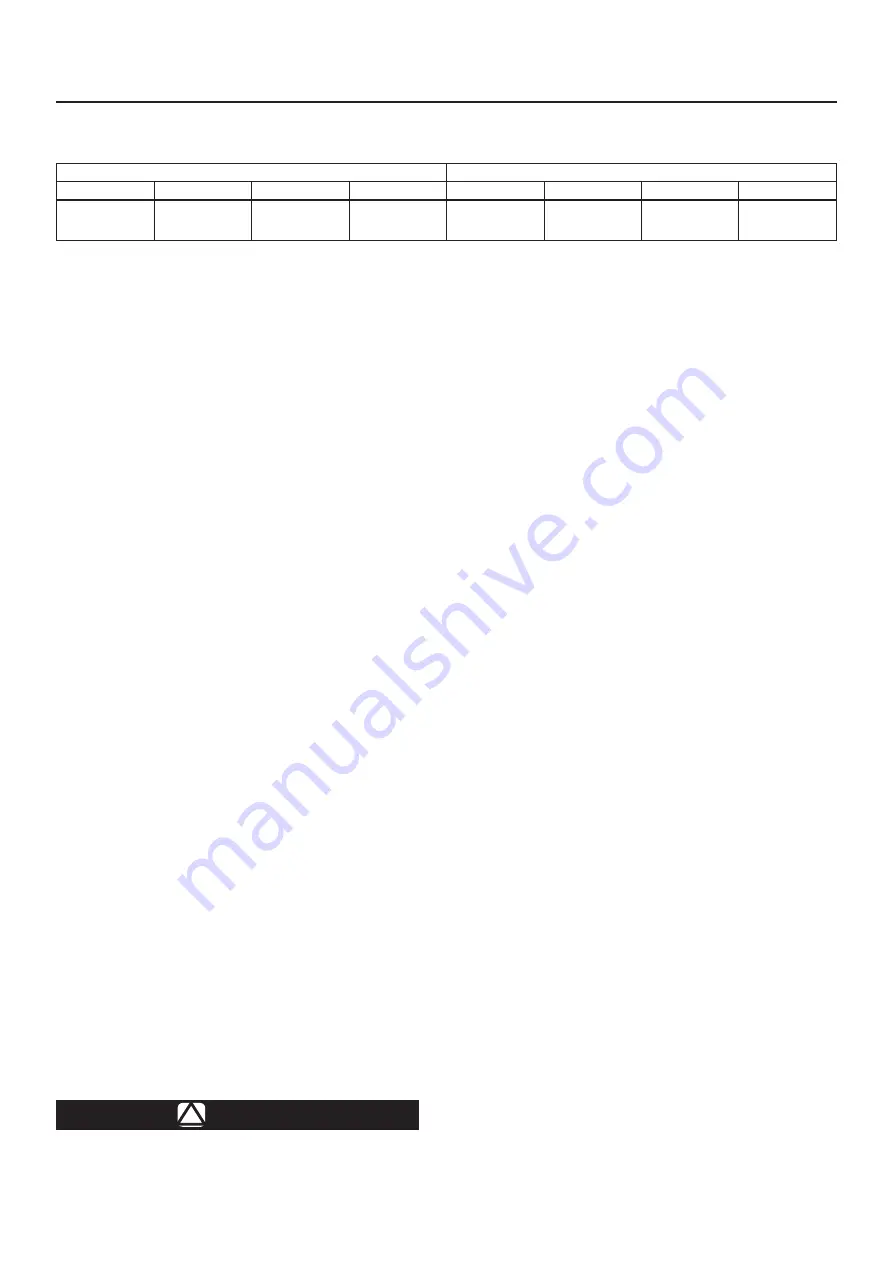
Clean out all pipelines before installation of the regulator
and check to be sure the regulator has not been damaged
or has collected foreign material during shipping. For NPT
bodies, apply pipe compound to the external pipe threads.
For flanged bodies, use suitable line gaskets and approved
piping and bolting practices. Install the regulator in any
position desired, unless otherwise specified, but be sure flow
through the body is in the direction indicated by the arrow on
the body.
Note
It is important that the regulator be installed
so that the vent hole in the spring case
is unobstructed at all times. For outdoor
installations, the regulator should be located
away from vehicular traffic and positioned
so that water, ice and other foreign materials
cannot enter the spring case through the vent.
Avoid placing the regulator beneath eaves
or downspouts and be sure it is above the
probable snow level.
Overpressure Protection
The recommended pressure limitations are stamped on
the regulator nameplate. Some type of overpressure
protection is needed if the actual inlet pressure exceeds the
maximum operating outlet pressure rating. Overpressure
protection should also be provided if the regulator inlet
pressure is greater than the safe working pressure of the
downstream equipment.
Regulator operation below the maximum pressure limitations
does not preclude the possibility of damage from external
sources or debris in the line. The regulator should be
inspected for damage after any overpressure condition.
Startup
The regulator is factory set at approximately the midpoint
of the spring range or the pressure requested, so an initial
adjustment may be required to give the desired results.
With proper installation completed and relief valves properly
adjusted, slowly open the upstream and downstream
shutoff valves.
Adjustment
To change the outlet pressure, remove the closing cap or
loosen the locknut and turn the adjusting screw clockwise
to increase outlet pressure or counterclockwise to decrease
pressure. Monitor the outlet pressure with a test gauge
during the adjustment. Replace the closing cap or tighten the
locknut to maintain the desired setting.
Taking Out of Service (Shutdown)
!
WARNING
To avoid personal injury resulting from sudden
release of pressure, isolate the regulator from
all pressure before attempting disassembly.
Parts List
161 and 161EB Series Pilots
(Figures 1 through 3)
Key Description
1
Body Assembly
2
Spring Case
3
Body Plug
4*
Valve Plug
6
Plug Spring
7*
Diaphragm Assembly
8
Upper Spring Seat
9
Control Spring
10
Diaphragm Limiter
11
Adjusting Screw
12
Locknut
13
Machine Screw (6 required)
14
Pipe Plug
15
Body Plug O-ring
16
Closing Cap
17*
Closing Cap Gasket
18
Type Y602-12 Vent Assembly
19*
Stem Guide Seal Assembly, Types 161M,
161EBM and 161EBHM
22
O-ring, Types 161M, 161EBM and 161EBHM
23
O-ring, Types 161, 161M and 161EBHM
26
Gauge, Type 161EB
38
Lower Spring Seat, Types 161EB and 161EBM
Types 161AY, 161AYM and 161AYW Pilots
(Figure 4)
Key Description
1
Body
2
Cap Screw (2 required)
3
Spring Case Assembly
4
Lower Casing
5
Orifice
6
Control Spring
7
Diaphragm Head
8
Pusher Post
10*
Diaphragm
11*
Body Seal
12*
Insert Seal
13*
Disk Assembly
14
Stem
15*
Cotter Pin (Types 161AY and 161AYM only)
16
Lever Assembly
17
Machine Screws (2 required)
18
Guide Insert
21
Hex Nut
22
Closing Cap
23
Hex Nut (8 required)
24
Cap Screw (8 required)
25
Closing Cap Gasket, for steel closing cap
26
Vent Assembly
30*
Stem Seal O-ring (Type 161AYM only)
31*
Throat Seal (Type 161AYM only)
33*
Machine Screw (Type 161AYM only)
35
Adjusting Screw
37
Spring Holder
38
Machine Screw
39
Overpressure Spring
40
Pusher Post Connector
46
Nameplate
47
Drive Screw (2 required)
48*
Post Seal
161AY SERIES
161EB SERIES
Orifice Size
C
g
C
v
C
1
Orifice Size
C
g
C
v
C
1
2.4 mm / 3/32 in.
3.2 mm / 1/8 in.
6.4 mm / 1/4 in.
6.9
12.3
50
0.20
0.35
1.43
35
35
35
3.18 mm / 1/8 in.
8.5
0.28
30.4
Table 2.
Pilot Flow Coefficients
*Recommended Spare Part
161 Series
2