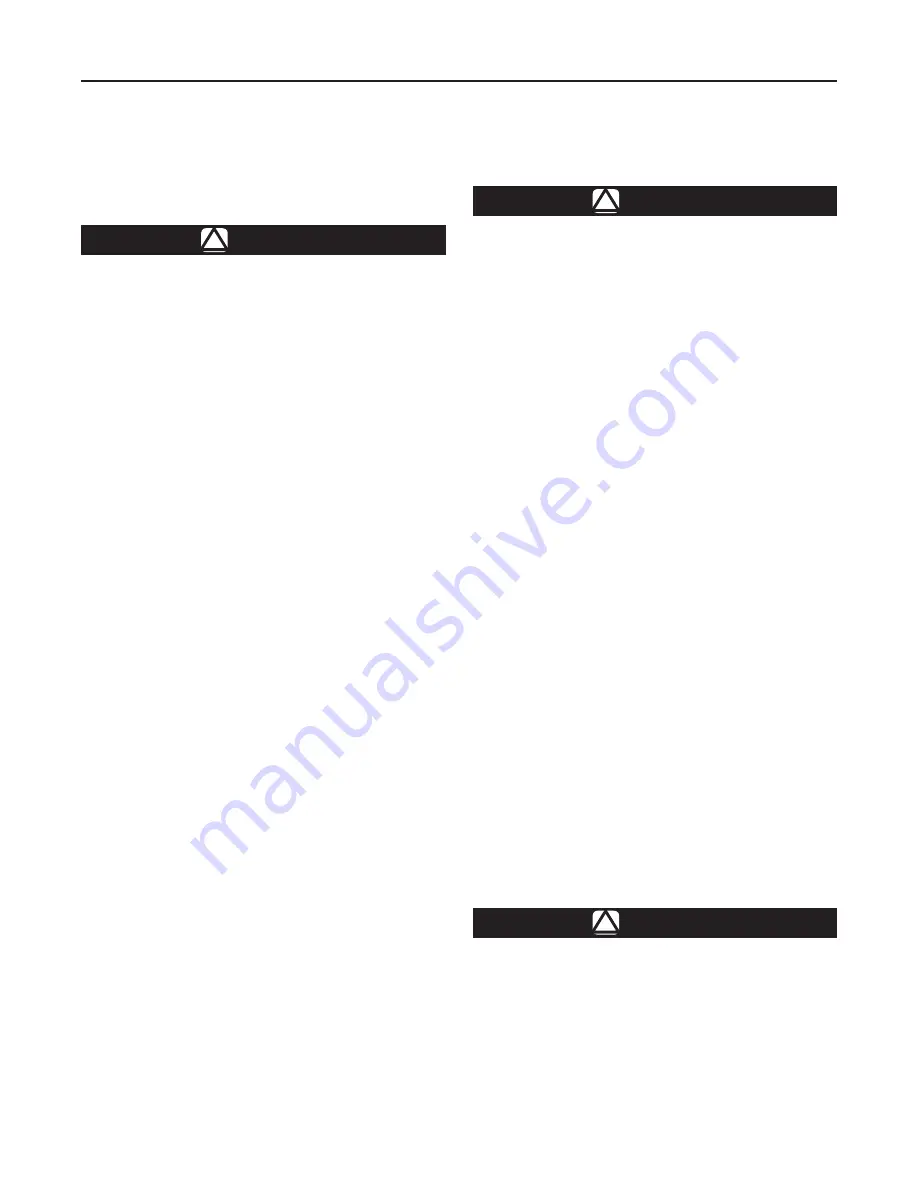
Y600A Series
3
2. The regulator may be installed in any position as
long as the flow through the body is in the direction
indicated by the arrow cast on the body. If
continous operation is required during inspection or
maintenance, install a three-valve bypass around
the regulator.
A regulator may vent some gas to the
atmosphere. In hazardous or flammable
gas service, vented gas may accumulate
and cause personal injury, death, or
property damage due to fire or explosion.
Vent a regulator in hazardous gas service
to a remote, safe location away from air
intakes or any hazardous area. The vent
line or stack opening must be protected
against condensation or clogging.
3. Be certain that the vent (key 26) is not positioned
so that it can collect moisture which may drain into
the spring case. The diaphragm casing (key 4) may
be rotated to any of four positions with respect to the
body in order to obtain desired positioning. Perform
Body Area Maintenance procedure steps 1 and 4
through 8 to rotate the diaphragm casing.
4. The Type Y600AM regulator requires a downstream
control line. Be sure to install this control line before
putting the regulator into operation. The downstream
control line pipe should be at least 1/2-inch (12,7mm)
in diameter and connected to a straight section of
outlet piping at least 5 to 10 pipe diameters downstream
of the regulator. If instability due to turbulence exists,
a hand valve can be installed in a straight section of
the control line. This hand valve can be throttled down
to dampen out pulsations.
Startup and Adjustment
A Y600A Series regulator can be placed in operation by
slowly introducing inlet pressure. The regulator takes
control when downstream pressure is established.
The regulator has been adjusted at the factory to provide
approximately the reduced pressure requested on the
order. With a spring-loaded regulator, the pressure
setting may be adjusted within the spring range shown
in Table 1. To adjust the pressure setting, perform the
following steps (key numbers are referenced in Figures 3
through 6):
1. Remove the closing cap (key 22).
!
WARnIng
2. Use a 1-inch (25,4 mm) hex rod or screwdriver to
turn the adjusting screw (key 35) either clockwise to
increase outlet pressure or counterclockwise to
decrease outlet pressure.
To avoid personal injury, property
damage, or equipment damage caused
by bursting of pressure containing parts
or explosion of accumulated gas, never
adjust the control spring to produce an
outlet pressure higher than the upper
limit of the outlet pressure range for
that particular spring. If the desired
outlet pressure is not within the range
of the control spring, install a spring
of the proper range according to the
Diaphragm and Spring Case Area section
of the Maintenance procedure.
3. After making the adjustment and replacing the
closing cap (key 22), the closing cap can be wired to
the spring
case (key 3) to discourage tampering.
Shutdown
First close the nearest upstream shutoff valve and then
close the nearest downstream shutoff valve to vent the
regulator properly. Next, open the vent valve between
the regulator and the downstream shutoff valve closest to
it. All pressure between these shutoff valves is released
through the open vent valve, since a Y600A Series
regulator remains open in response to the decreasing
downstream pressure.
Maintenance
Regulator parts are subject to normal wear and must be
inspected and replaced as necessary. The frequency
of inspection and replacement of parts depends on
the severity of service conditions and upon applicable
codes and government regulations. Key numbers are
referenced in Figures 3 through 5 unless otherwise noted.
To avoid personal injury, property damage,
or equipment damage caused by sudden
release of pressure or explosion of
accumulated gas, do not attempt any
maintenance or disassembly without
first isolating the regulator from system
pressure and relieving all internal pressure
from the regulator.
!
WARnIng
!
WARnIng