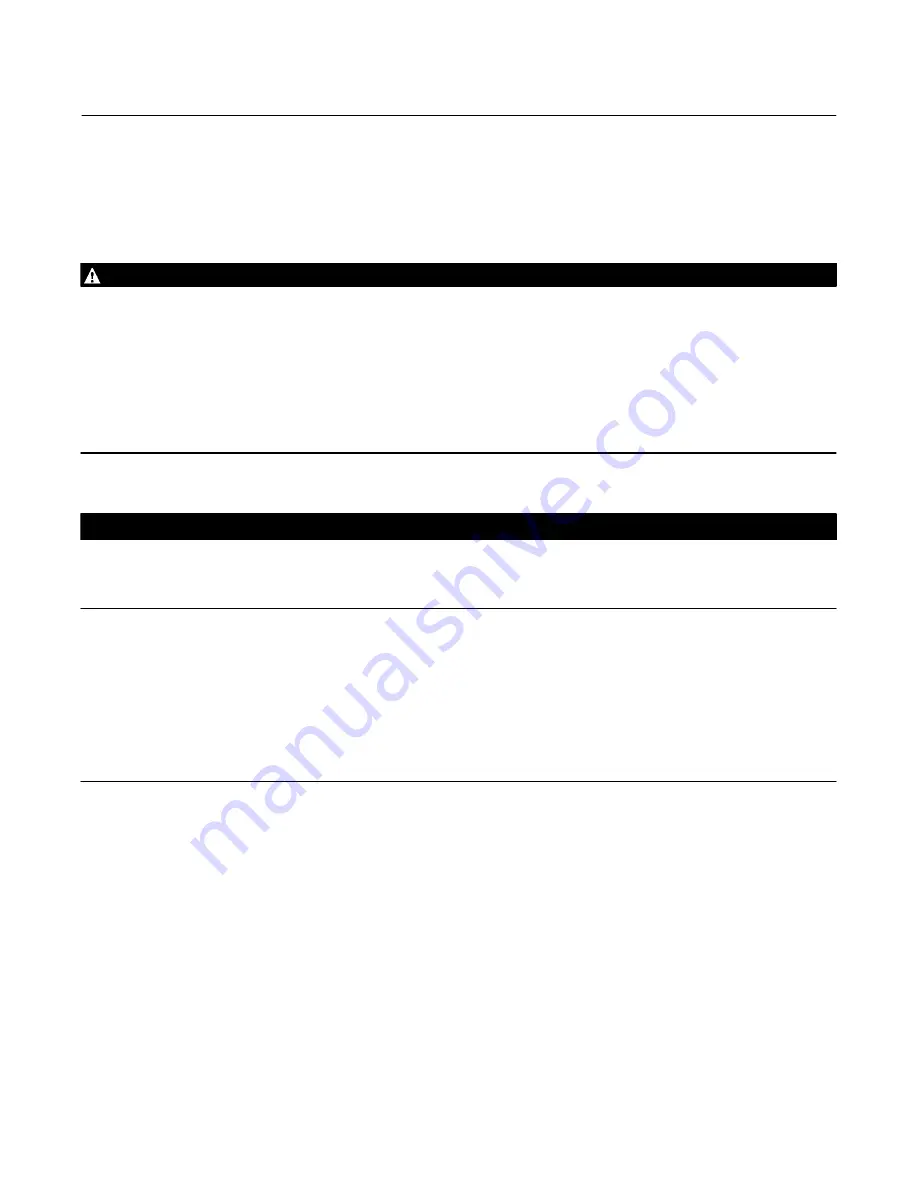
Instruction Manual
D103317X012
VBL Volume Booster
May 2017
4
Installation
WARNING
Always wear protective clothing, gloves, and eyewear when performing any installation procedures to avoid personal
injury.
System damage may result if a volume booster is installed in a way that it can be physically damaged.
Personal injury or system damage may result when service conditions exceed booster or other equipment ratings.
Exceeding the pressure specifications in table 1 may cause leakage, parts damage, or personal injury due to bursting of
pressure‐containing parts or explosion of accumulated gas.
Check with your process or safety engineer for any additional measures that must be taken to protect against process
media.
CAUTION
Do not use sealing tape on pneumatic connections. This instrument contains small passages that may become obstructed
by detached sealing tape. Thread sealant paste should be used to seal and lubricate pneumatic threaded connections.
Note
Do not use separate pressure supplies for the volume booster and associated positioner.
The volume booster may not exhaust immediately upon loss of a separate pressure supply. However, if the system is in a transient
state at the time of pressure supply loss or if changes to the booster's input signal are sufficient to overcome the deadband, the
booster will exhaust.
A loss of a pressure supply (either separate or common) to a Fisher 3582 or 3610J positioner will cause the positioners output
pressure (booster's input pressure) to decay.
Always pipe the positioner and the volume booster with one common supply. See figure 4 for typical installation
examples. A 67D, 67DR, or 95H regulator is required to provide sufficient capacity to supply both components. A
high‐capacity filter, such as the 262K, should be installed in the supply line to the regulator.
Mounting
The volume booster is typically nipple‐mounted between the pneumatic supply source and the actuator, and may be
used with piston or diaphragm actuators. Many actuators require larger casing or cylinder connections and
modifications to allow the booster to deliver the higher volume output.
The booster may also be directly mounted to the actuator by using an actuator yoke mounting bracket (see figure 2)
or casing mounting bracket. If a mounting bracket is used, remove the appropriate end cap screws and install the
mounting bracket. Install the end cap screws, re‐tightening to a recommended torque value of 12.5 N
S
m (110 lbf
S
in).