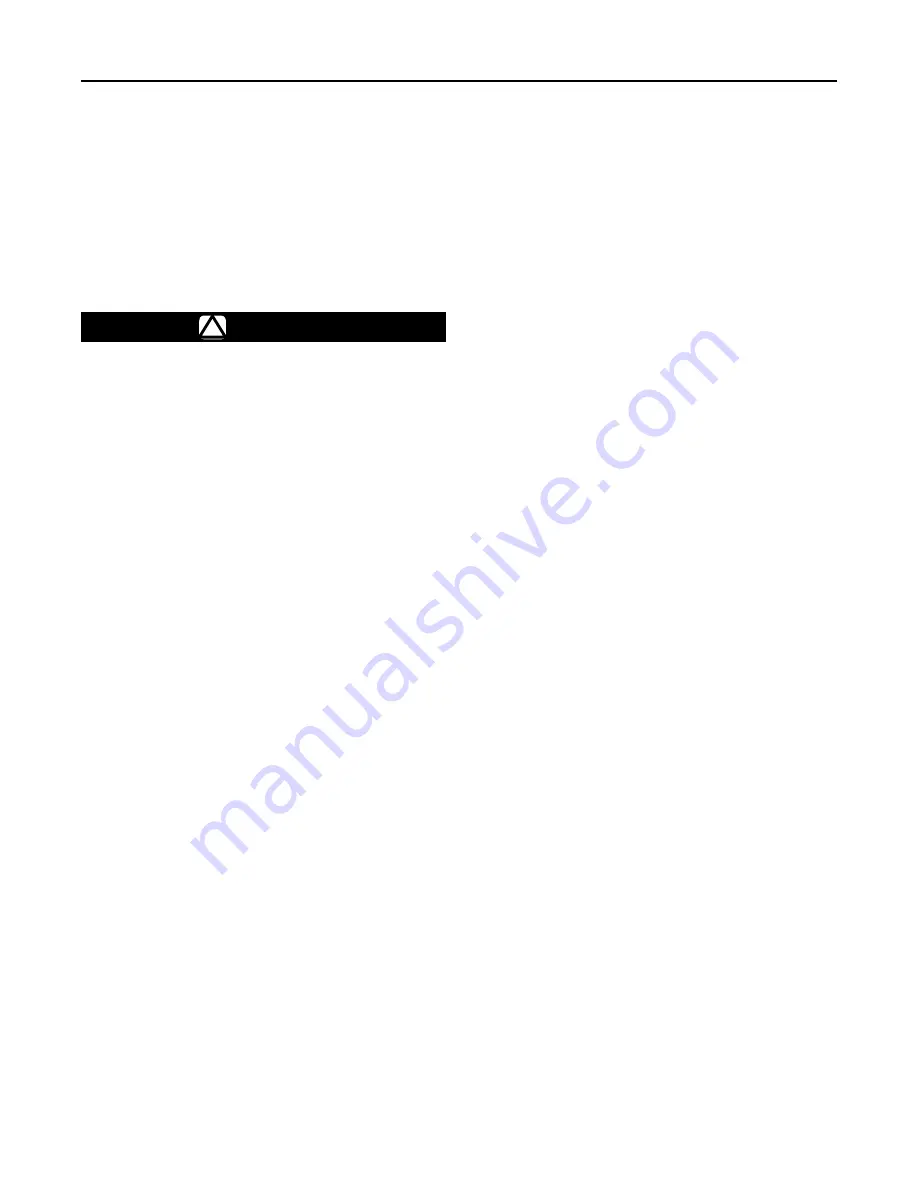
Type 99
11
diaphragm plate (key 10), pusher post assembly
(key 8) and diaphragm rod (key 4) must be mounted
on the ball of the lever (key 9) so that the pusher
post (key 8) orientation is as shown in Figure 9.
12. Install the upper casing (key 56, Figure 9)
and secure it to the lower casing (key 29) with
the twelve cap screws (key 12) torque 580 to
920 in-lbs / 65.5 to 104 N•m and hex nuts (key 13).
Put lower casing (key 29) back on body and install
union nut (key 14).
CAuTION
To avoid part damage due to over
compressing the main spring seat (key 2),
always use main spring seat 1E242724092
with main spring 0W019127022.
13. Thread the main spring seat (key 2) to the bottom
of the diaphragm rod (key 4) threads and then
back out 1 revolution.
14. Install a new spring case gasket (key 57,
Figure 9), the spring case (key 1) and the four
cap screws (key 58) with 340 to 420 in-lbs /
38.4 to 47.5 N•m of torque, making sure the
indicator stem, O-ring and gaskets (keys 103, 111
and 108, Figure 6) are installed, if used.
15. Connect the loading tubing, then refer to
the Startup section for putting the regulator
into operation.
Type 61L, 61LD, 61LE (Low) or 61H
(High Pressure) Pilot
This procedure is to be performed if changing the
control spring for one of a different range or if inspecting,
cleaning or replacing any other pilot parts. Key numbers
are referenced in Figure 9 through 15.
1. Remove the closing cap (key 46), if used, and
unscrew the adjusting screw (key 45) to relieve
control spring compression.
2. Disconnect the loading tubing (key 53) and pilot
supply tubing (key 24).
3. Unscrew the eight cap screws (key 47) and remove
the pilot assembly from the lower casing (key 29).
4. Use the projecting prong in the relay valve
body (key 39) as the restraining member and
remove the diaphragm nuts (key 13, Figure 9 and
key 51, Figure 11). Separate the parts and inspect
the diaphragms (keys 30 and 40) and O-ring seal
(key 33). Replace if worn or damaged.
5. Unscrew the bleed orifice (key 52, Figure 11) from
the yoke (key 37). Also to be removed with the
bleed orifice are the relay disk assembly (key 48)
and bleed valve (key 50). These parts can be
unthreaded for inspection and replacement,
if necessary.
6. When reassembling the pilot, the relay disk holder
assembly (key 48, Figure 11) and both diaphragms
(key 30, Figure 11 and key 40, Figure 12) should
be tightened on the yoke (key 37) after it is placed
in the body.
Note
Before putting the relay spring case over
the diaphragm, make certain the yoke is
square with respect to the prong in the
relay body. (The yoke can bind on the
prong if it is not square.)
7. Use care in reassembly to be sure the edges of
the diaphragms (key 30, Figure 11 and key 40,
Figure 12) slip properly into the recess on the
lower casing (key 29, Figure 9) and relay valve
body (key 39). With the pilot in place, check to
see if it can be rocked. If it does not rock, it is
in place and the diaphragms (key 30, Figure 11
and key 40, Figure 12) are free of wrinkles. With
both diaphragms firmly in place, install the cap
screws (key 47, Figure 9) using torque 150 in-lbs /
16.9 N•m of torque. Tighten using a crisscross
pattern to avoid placing a strain on the unit. Set
the pilot control spring (key 43) according to the
adjustment information in the Startup section.
8. Reinstall the closing cap (key 46, if used). If you
have a plastic closing cap, be sure that you have a
vent (key 60) in place of the pipe plug installed in
the low-pressure pilot spring case (key 44).
Type 61HP (Extra High Pressure) Pilot
This procedure is to be performed if changing the
control spring for one of a different range, or if
inspecting, cleaning or replacing any other pilot parts.
Key numbers are referenced in Figure 18 unless
otherwise specified.
1. Unscrew the adjusting screw (key 45) to relieve
control spring compression.
2. Disconnect the loading tubing (key 53, Figures 9
and 18) and pilot supply tubing (key 24, Figure 9).
3. Remove the six cap screws (key 123) which fasten
the spring case (key 44), spring seat (key 68) and
control spring (key 43) to the pilot body (key 39).