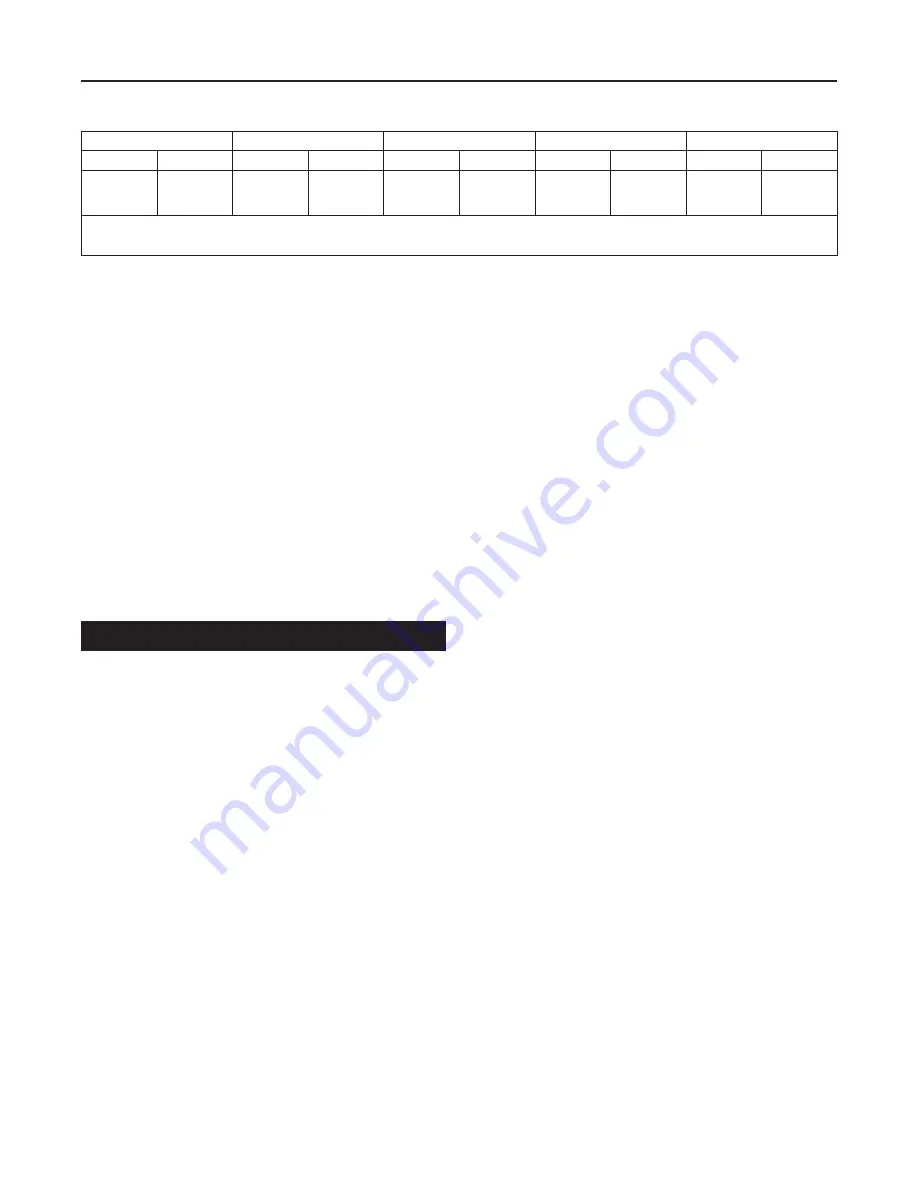
10
MR98 Series AD2000 Compliant
D-A-CH Region Only
Table 5.
Torque Specifications
BODY SIZE
SPRING CASE BOLTS
(1)
ORIFICE
VALVE PLUG GUIDE
BOTTOM PLUG
NPS
DN
Ft-lbs
N•m
Ft-lbs
N•m
Ft-lbs
N•m
Ft-lbs
N•m
1/2
3/4 and 1
1-1/2 and 2
15
20 and 25
40 and 50
10 to 13
24 to 30
40 to 50
13 to 18
33 to 41
54 to 68
34 to 38
50 to 60
180 to 200
46 to 51
68 to 81
244 to 271
70 to 90
85 to 100
125 to 150
94 to 122
115 to 136
169 to 203
75 to 90
100 to 125
170 to 200
102 to 122
136 to 169
230 to 271
1. Reduce spring case bolt’s torque by 30% when using Ethylenepropylene (EPDM) diaphragms.
Note: Pusher post lock nut (key 31) should be installed with an additional 1/8 to 1/4 turn when washer is flat. See step 10 in the “Disassembly to Replace Diaphragm and Seats” section or
detailed instruction.
Flange Cap Screw Torque Inspection
Retorquing of spring case cap screws may be
necessary for some MR98 Series Regulators after a
period of use. Retorque the cap screws as follows:
1. Shut down the relief valve or backpressure
regulator. Refer to Shutdown section for the
proper procedure.
2. Retighten the cap screws (key 16) in a crisscross
pattern. See Table 5 for proper torque values.
3. Follow the Startup section to repressurize the relief
valve or backpressure regulator.
4. Refer to the Disassembly to Replace Diaphragm
and Seats section as needed.
Disassembly to Replace Diaphragm
and Seats
△
CAUTION
Metal diaphragms have thin sharp
edges. To avoid hand cuts, be careful
when handling the diaphragm,
particularly the diaphragm edge.
If the relief valve is leaking, the diaphragm may be
ruptured or the seating surfaces nicked or scratched.
Proceed as follows to inspect or replace the
diaphragm, orifice and valve plug.
1. Shut down the backpressure regulator or
relief valve. Refer to Shutdown section for the
proper procedure.
2.
For Types MR98H and MR98HH:
Relieve
the spring tension by loosening the jam
nut (key 17) and turning the adjusting
screw (key 15) counterclockwise.
3. Remove cap screws (key 16) and lift off the
spring case (key 2), upper spring seat (key 9)
and relief valve spring (key 11). Lift out the
diaphragm unit which includes the lock nut
(key 31), lock washer (key 28), pusher post
(key 10), gasket (key 29), lower spring seat (key 8),
diaphragm (key 12), diaphragm head (key 21 for
Type MR98H, 1-1/2 and 2 in. / DN 40 and 50 body
sizes) and valve plug (key 4).
4. Check the orifice (key 3) for wear or damage. If it
needs to be replaced, unscrew the valve plug guide
(key 7) and then the orifice. The valve plug (key 4)
can be removed by sliding it off of the pusher
post (key 10).
5. Place a small amount of sealant on the threads
of the orifice (key 3) and valve plug guide (key 7)
and reinstall these to the body (key 1). See
Table 5 for torque specifications.
6. To replace the valve plug O-ring (key 53), remove
the machine screw (key 24) and O-ring retainer
(key 25) from the plug. Remove and replace
the O-ring.
7. Separate the remainder of the diaphragm unit
parts. Take the lock nut (key 31) off of the pusher
post (key 10). Slide off the lock washer (key 28),
lower spring seat (key 8), diaphragm head (key 21
for Type MR98H, 1-1/2 and 2 in. / DN 40 and 50
body sizes), diaphragm (key 12), washer (key 58)
and gasket (key 29).
8. Slip the valve plug (key 4) onto the pusher post
(key 10). Place a gasket (key 29) on the shaft
of the pusher post over the threaded portion
until it rests on the base of the post. If elastomer
diaphragm (key 12) is used, place a metal washer
(key 58) on top of the gasket. For Type MR98H,
1-1/2 to 2 in. / DN 40 to 50 with metal diaphragm,
place another gasket on the shaft of the pusher
post until it rests on the bottom diaphragm head
(key 21), see Figure 4.