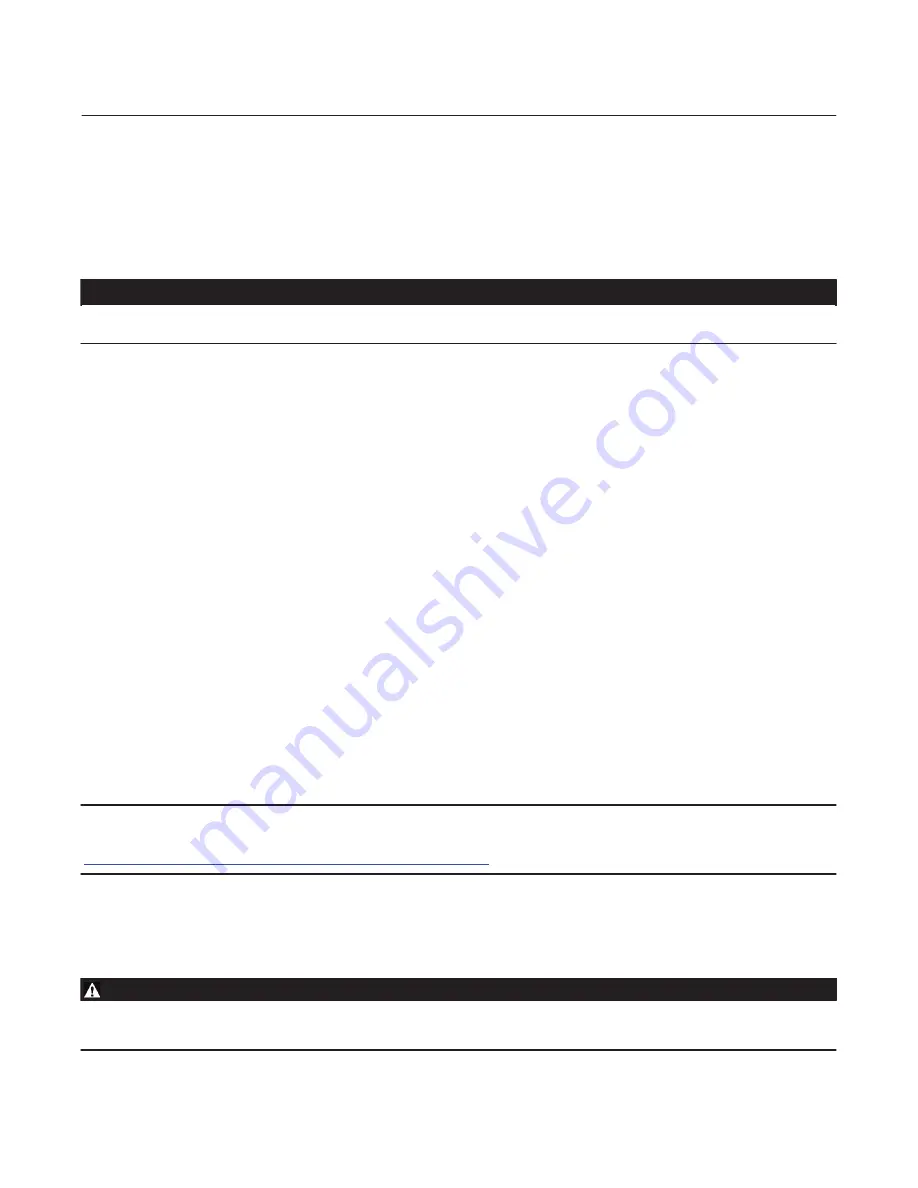
Instruction Manual
D100391X012
EDR and ETR Valves
March 2016
14
Installing Packing
If the trim is removed, refer to Trim Maintenance procedures, and install the trim (including the valve stem) before
installing the packing. If necessary, use the Lapping Metal Seats procedures before installing packing. Key number
locations are shown in figure 5 or 6 unless otherwise indicated.
CAUTION
To prevent possible product damage, take care when installing the bonnet over the valve stem in the following procedure.
1. If the bonnet has been removed from the valve body, install the replacement bonnet (see figure 4). Carefully slide
the bonnet over the valve stem without damaging the stem surfaces.
2. Refer to figure 5 or 6 for the sequence of parts to make up the appropriate packing set for your application. Arrange
the packing parts in sequence before installing them into the packing box.
3. For split‐ring packing, alternate the positions of the splits to avoid creating a leak path. Place a smooth‐edged pipe
over the valve stem and gently tap each soft packing ring into the packing box. Be sure that air is not trapped
between adjacent soft parts.
4. Install the packing follower (key 13), packing flange (key 3), and upper wiper (key 12, if required). Install the packing
flange nuts (key 5).
5. Refer to actuator installation procedures in the actuator instruction manual, and the installation procedures in the
manual when mounting and connecting the actuator to the valve. If lubrication is required, refer to the Packing
Lubrication section below.
6.
For spring‐loaded PTFE V‐ring packing,
tighten the packing flange nuts until the shoulder on the packing follower
(key 13, figure 4) contacts the bonnet.
For graphite packing,
tighten the packing flange nuts to the maximum recommended torque shown in table 4. Then,
loosen the packing flange nuts, and retighten them to the recommended minimum torque shown in table 4.
For other packing types,
tighten the packing flange nuts alternately in small equal increments until one of the nuts
reaches the minimum recommended torque shown in table 4. Then, tighten the remaining flange nuts until the
packing flange is level and at a 90‐degree angle to the valve stem.
Note
If the valve has ENVIRO‐SEAL live‐loaded packing installed (figure 8, 9, or 10), see the Fisher instruction manual entitled
ENVIRO‐SEAL Packing System for Sliding‐Stem Valves (D101642X012)
for packing instructions.
Packing Lubrication
WARNING
To avoid personal injury or property damage resulting from fire or explosion, do not lubricate packing used in oxygen
service or in processes with temperatures over 260
_
C (500
_
F).