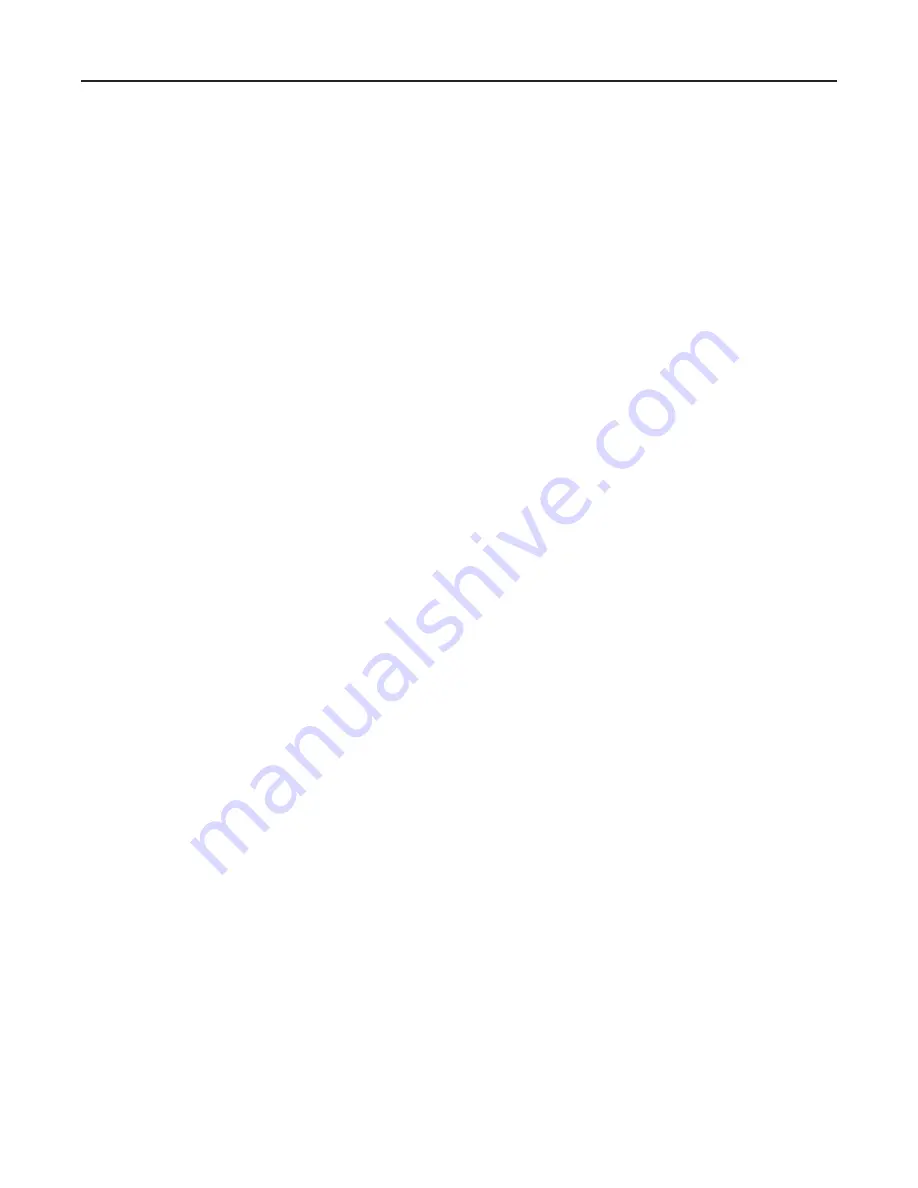
3. Take out the diaphragm assembly which consists of
two metal diaphragms (key 60), bleed fitting (key 61)
and diaphragm plate (key 59). Separate these
parts by unscrewing the bleed fitting from the
diaphragm plate.
4. Remove cap screws from bottom flange (key 52).
Take off bottom flange. The valve plug (key 56) and
spring (key 57) will drop out.
5. If the seat ring (key 58) shows signs of wear, lap
the seat ring to remove imperfections.
Pilot Disassembly
Type 92B Pilot Only
Key numbers listed are shown on the appropriate pilot
assembly drawing, Figure 9, 10, 11 or 12.
1. Remove pilot from main valve by unscrewing it from
the mounting nipple or unscrewing the nipple from
main valve.
2. Relieve the spring compression by turning the set
screw (key 15) counterclockwise after loosening hex
nut (key 16).
3. Remove the casing cap screws. Take off the spring
case, and remove upper spring seat, spring, lower
spring seat, two diaphragms and the diaphragm
gasket. Note that in a low-pressure pilot (Figure 9), the
lower spring seat and the diaphragm plate are both
parts of the diaphragm plate assembly (key 24) and
are pinned together.
4. Unscrew the bellows retainer (key 8) from the pilot
body. Take out the bellows and the valve stem
(keys 9 and 7).
5. Unscrew the valve plug guide (key 2). The valve plug
(key 4), the valve plug spring (key 3) and the strainer
screen (key 77) will come out with the guide.
6. Unscrew the orifice (key 5), if necessary.
7. Remove the check valve assembly (key 75) with
a screwdriver after having removed the pipe plug
(key 74). Be sure the check valve is not clogged.
Replace the entire check valve assembly, if
necessary. The check valve assembly should not be
disassembled in the field, because its setting is made
at the factory and will be lost by disassembling.
Main Valve Reassembly
Type 92B (Figure 8)
Inspect all internal parts for excessive wear or damage.
Use new parts when necessary (see Table 5 for torque
values). Reassemble the main valve as follows:
1. Install valve plug (key 56) and its spring (key 57).
2. Use new bottom flange gasket (key 54) and replace
the bottom flange (key 52). Lubricate and replace cap
screws (key 55) (see Table 5 for torque values).
3. Make up the diaphragm assembly by lubricating
and then screwing the bleed fitting (key 61) into the
diaphragm plate (key 59) (see Table 5 for torque
values) and clamping the diaphragm (key 60)
in place.
4. Apply a thin layer of anti-seize lubricant onto
the sealing surfaces of the diaphragm casing
(key 62) and the body (key 51) prior to installing
the diaphragm assembly. Place the diaphragm
assembly on the body and replace the diaphragm
case (key 62). Make sure assembly marks line
up. Lubricate and replace cap screws and nuts
(keys 63 and 64) (see Table 5 for proper torque
values). On cast iron bodies, install the loading
tubing compression coupling fitting on the pipe
nipple (NPS 1-1/2 through 4 / DN 40 through 100).
5. Reconnect all tubing after the pilot is mounted.
Type 92B Pilot Reassembly
(Figure 9 or 10)
Inspect all internal parts for excessive wear or damage.
Use new parts wherever necessary. Reassemble the
pilot as follows (see Table 6 for torque values):
1. Apply high temperature thread sealant to the orifice
threads. Screw in the orifice (key 5) (see Table 6 for
torque values).
2. Place valve plug spring (key 3), the valve plug
(key 4), and the strainer screen (key 77) in the valve
plug guide (key 2). Apply high temperature thread
sealant to the plug guide threads Screw guide
into body (key 1) (see Table 6 for torque values).
3. Place valve stem (key 7) in the body, smaller
diameter first.
10
Type 92B