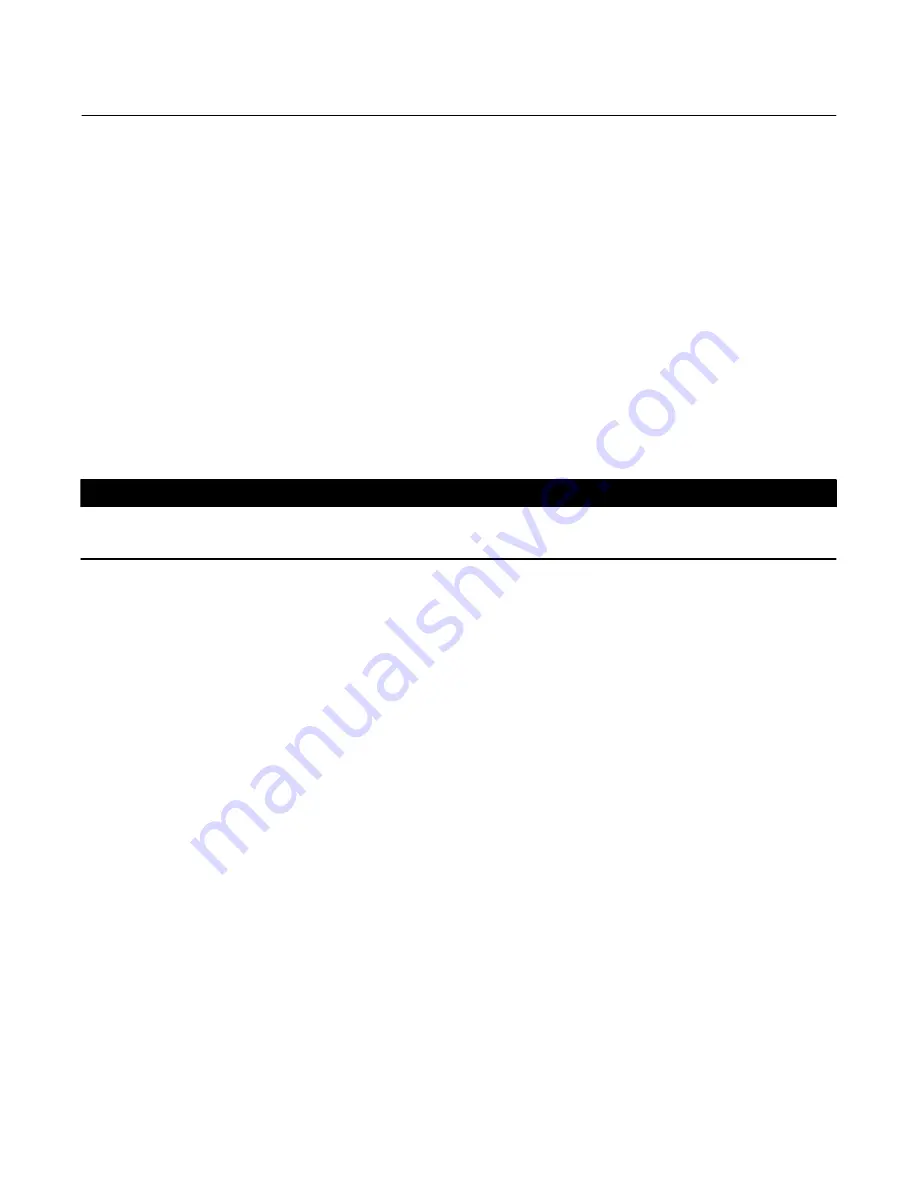
Instruction Manual
D200158X012
4194S Controllers
July 2018
49
3. Apply 50 percent of full span remote set point pressure.
4. The drive flexure (key 79) should be straight. If not, proceed as follows:
a. Loosen the screw on the adjustment arm on pivot assembly A (key 114) and the screws holding the drive flexure.
b. Set the length of the adjustment arm so that the drive flexure is parallel to the centerline of the capsules.
c. Tighten the screw on the adjustment arm.
d. Set pivot A in the middle of the bushing end play.
e. Tighten the screws that hold the drive flexure in place.
5. The guide flexure should also be straight. If not, loosen the screw (key 122) on the end of the flexure that is
attached to the top of pivot A (key 114), and allow the flexure to straighten itself. Tighten screw on the flexure.
Setting the Travel Stops
1. Loosen the set screw in the travel stop nut (key 86).
CAUTION
Make sure the loose travel stop nut does not bind up on the diaphragm capsule extension when pressurizing the capsules.
Damage to the capsules may result.
2. Full span stop—Adjust remote set pressure input to 5 percent greater than full span pressure.
Loosen the two screws mounting the travel stop (key 83) to the mounting plate. Slide the travel stop until it is just
touching the end of the capsule stack. Tighten the travel stop mounting screws to lock it into that position.
3. Zero Stop—Adjust remote set point pressure input to 0 psig.
Slide the travel stop nut (key 86), along the diaphragm capsule extension (key 134) until it is approximately 0.4 mm
(1/64 inch) away from the travel stop (key 83). Tighten the set screw to lock the travel stop nut in that position.
Aligning the Linkage
1. Adjust the remote set point pressure to the capsules to 50 percent of full span.
2. Set the linearity adjustment screw in the center of the slot on the lever arm of pivot clevis assembly B (key 115).
3. Set the length of link B (key 126) in the middle of its adjustment.
4. Set the length of link A (key 116) so that the lever arms of pivots A and B are parallel and that link A is perpendicular
to them.
5. To complete maintenance calibration, the zero and span adjustments must be set. Refer to the following section for
the procedures. If linearity adjustments must also be made, refer to that portion of this section.
6. Replace the tie bar (key 106).
7. Refer to the Flapper Alignment procedure.
Zero and Span Adjustment
1. Decrease remote set point pressure to 0 psig.
2. Loosen the screw on link A (key 116), and adjust the length so that the set point pointer points to scale zero.
Tighten the screw.