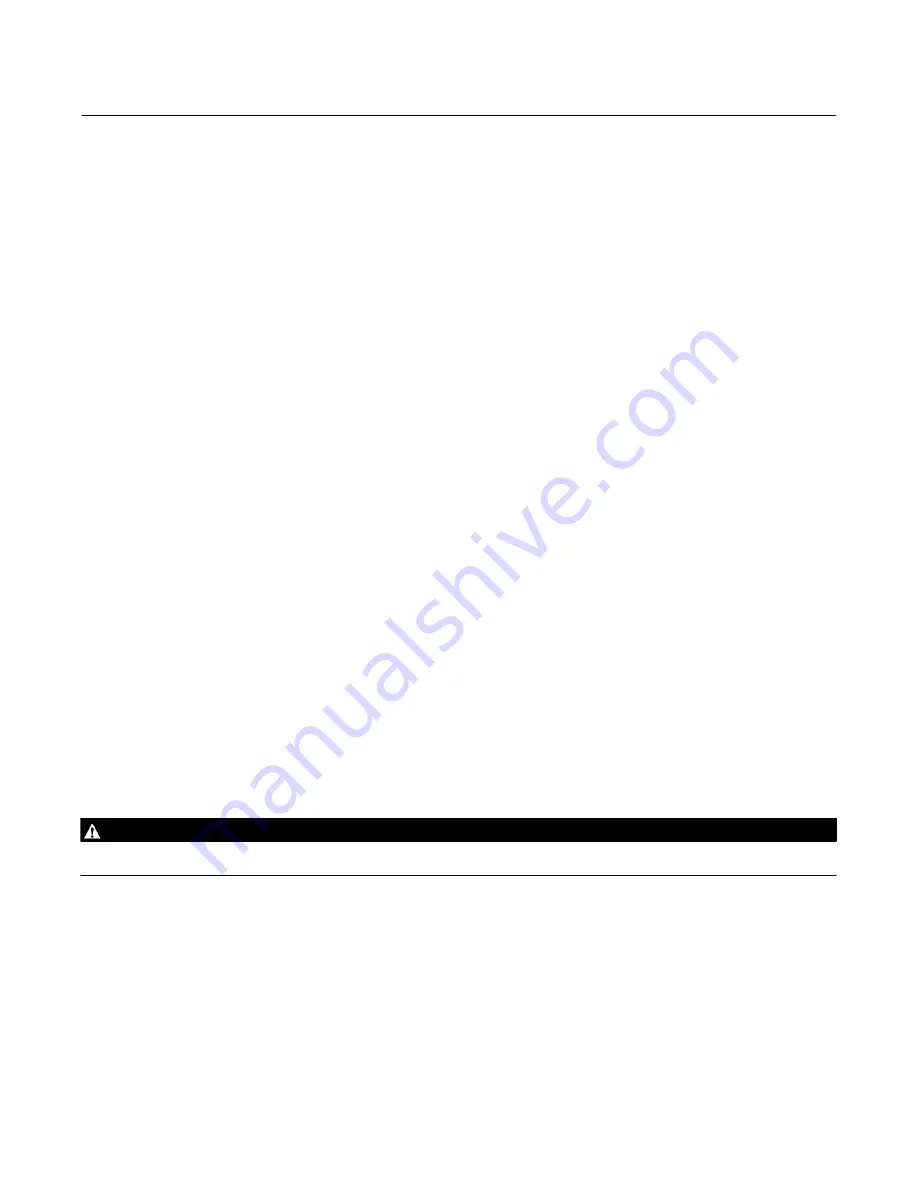
Instruction Manual
D200158X012
4194S Controllers
July 2018
44
a. Turn the span adjustment screw clockwise. (Adjust the span to correct one‐half the error).
b. To increase the span further than the adjustment will allow, move both ends of link 5 (key 88) down one set of
holes. Refer to figure 4-12 for link location.
c. Make fine adjustments with the span adjustment screw.
8. To decrease the span, proceed as follows:
a. Turn the span adjustment screw counterclockwise. (adjust span to correct one‐half the error).
b. To decrease the span further than the adjustment will allow, move both ends of link 5 (key 88) up one set of
holes.
c. Make fine adjustments with the span adjustment screw.
9. Repeat the adjustments until zero and span indications are within
±
1 percent of input span.
10. Check the pointer position at 50 percent of full process pressure input span. If the error is greater than
±
1 percent of
input span, perform the procedures in the Linearity Adjustment procedure. Remove process pressure from the
controller.
11. Install the proportional band indicator cover (key 36), and tighten the two screws (key 6).
Linearity Adjustment
Adjust the linearity by turning the linearity adjustment screw in the curved slot on the lever arm of the short pivot
assembly (key 89). Adjusting the linearity affects the zero and span.
1. Adjust the process differential pressure to 50 percent of input span. The process pointer should indicate the 50
percent mark on the scale.
2. If the pointer indicates high, turn the linearity screw counterclockwise in the slot. If the pointer indicates low turn
the linearity screw clockwise in the slot.
3. Check the zero and span as described in the Zero‐and‐Span Adjustment procedures and make any necessary
adjustments.
4. Repeat steps 1 through 3 until zero, span, and linearity indications are within
±
1 percent of input span.
Flapper Alignment
WARNING
Refer to the Maintenance WARNING on page 21.
Leveling screws numbers and adjustments are shown in figure 3-1. Provide a means of applying process differential
pressure and supply pressure to the controller and a means of measuring output pressure. After flapper alignment, go
to the appropriate prestartup instructions in the controller operation procedures.
1. For controllers with manual set point, move the set point adjustment to 50 percent of the scale range. For
controllers with remote set point (option M), adjust the remote set point pressure until the set point indicator is at
50 percent of the scale range.
2. Remove the two screws (key 6) and lift off the proportional band indicator cover (key 36).
3. Adjust the proportional band adjustment to 5 percent direct acting.